Not dead yet
Guitar Logistics
Built to Spec
Friday, May 6, 2016
Monday, July 28, 2014
Phobos almost done.
Finish Time...
Time to wrap up some builds.
Clear a spot for the ground wire
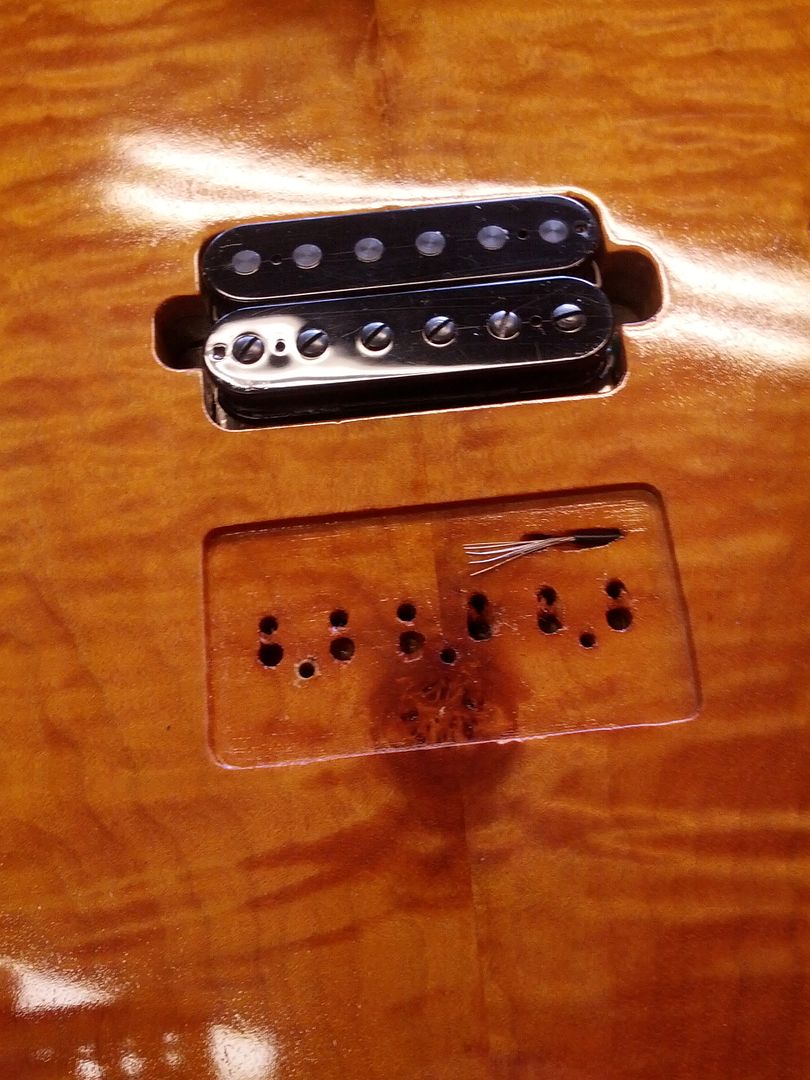
Recessed bridge plate fits nice and I like the all black pickups.
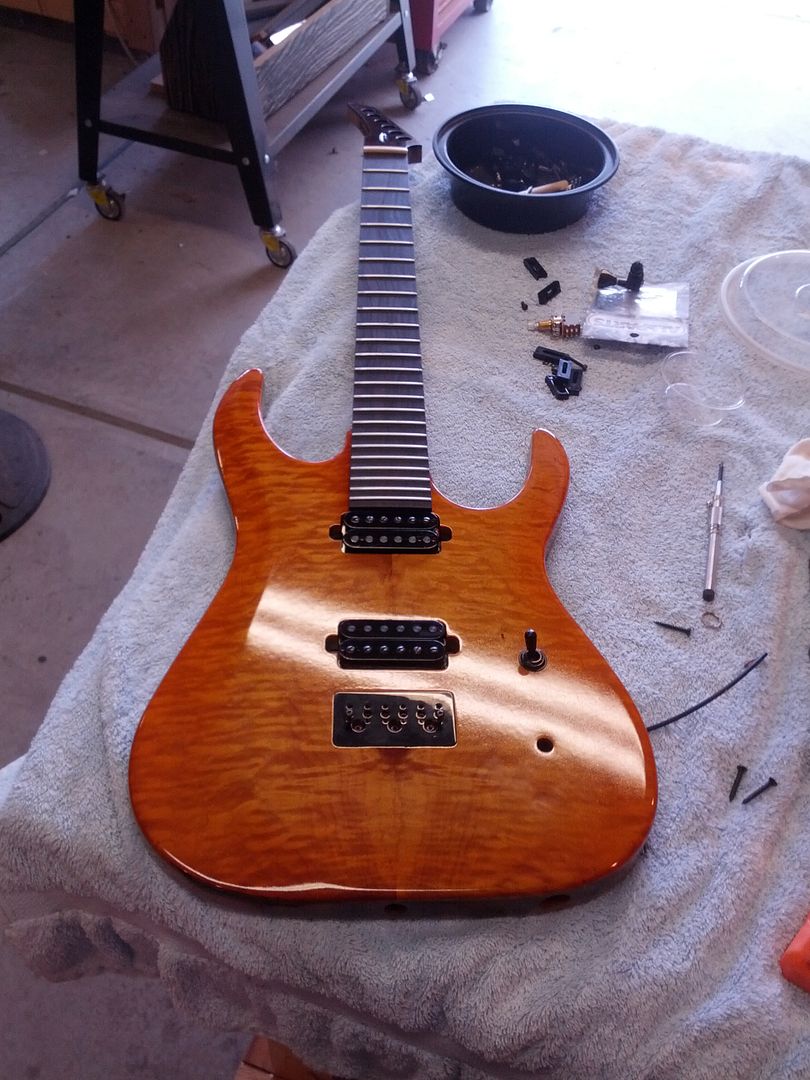
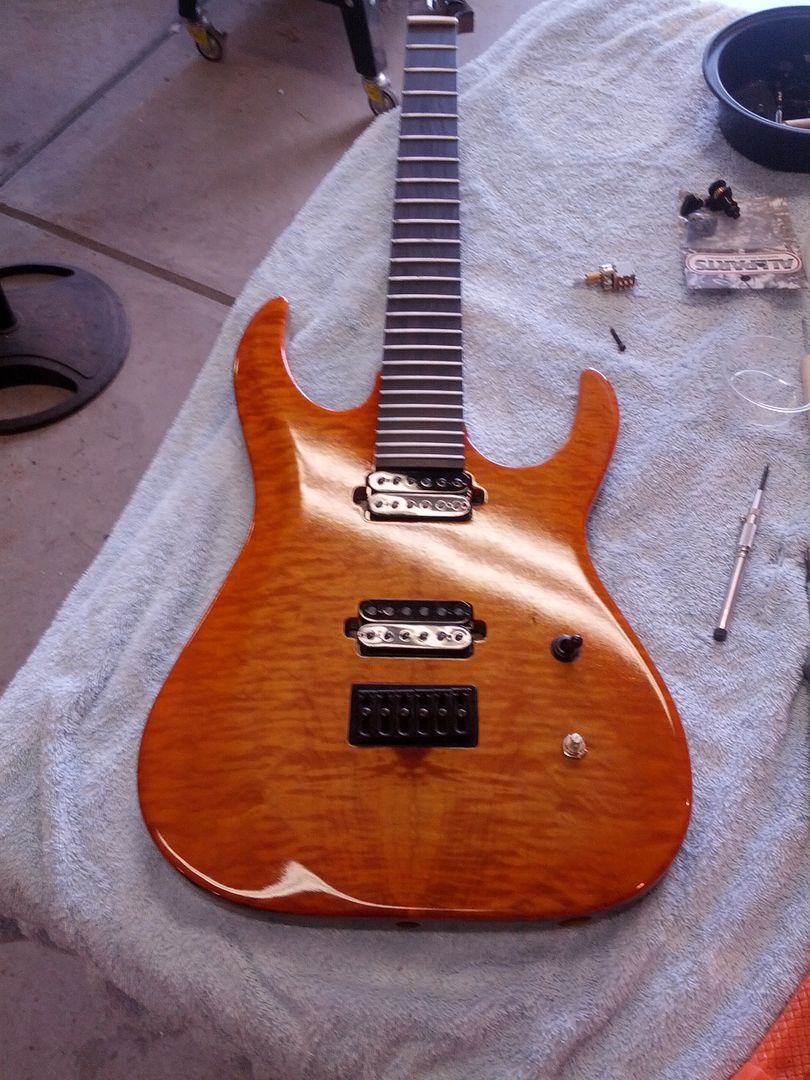
You know I will probably have to take this apart again but it is nice to get a good look at it.
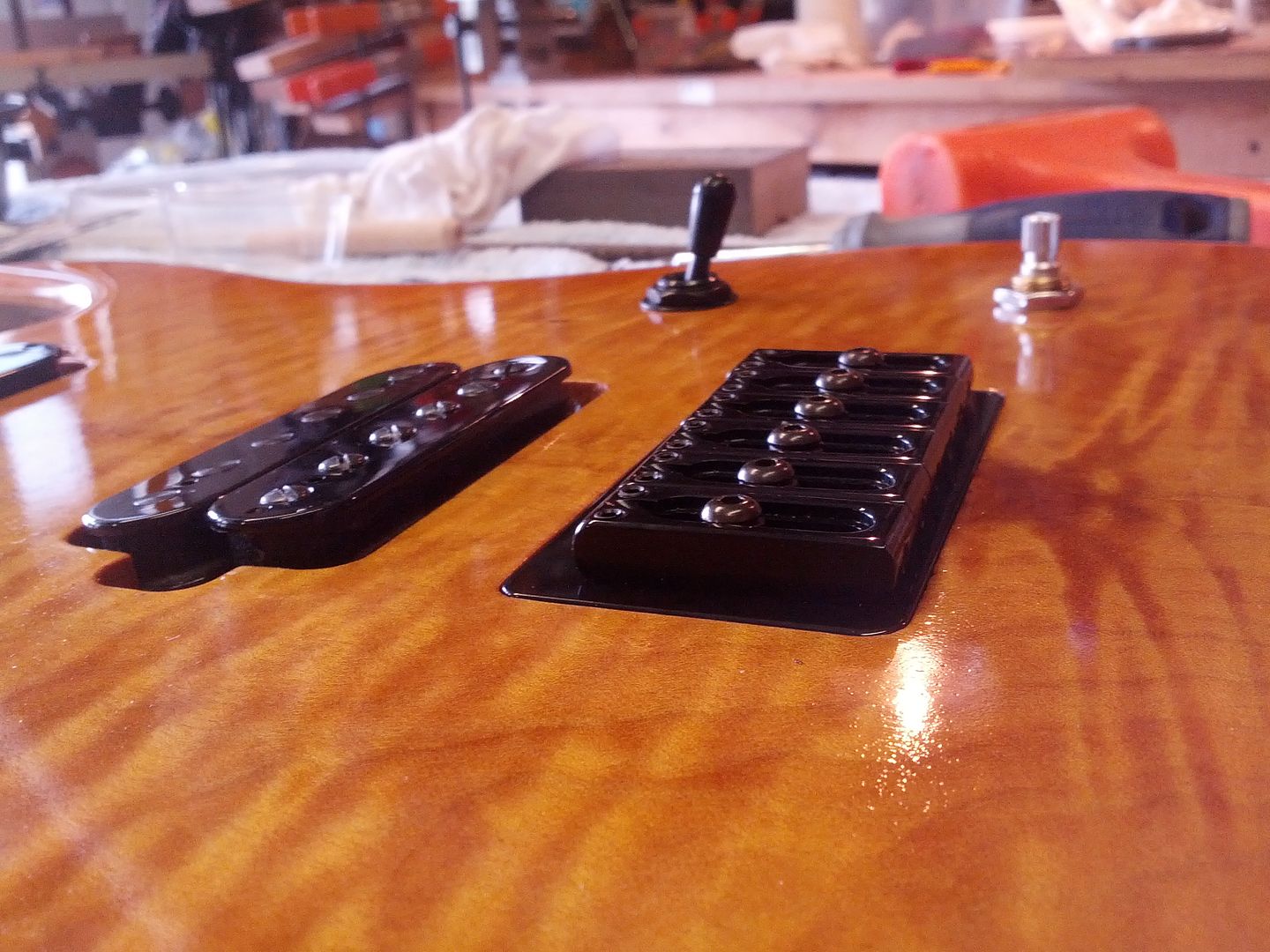
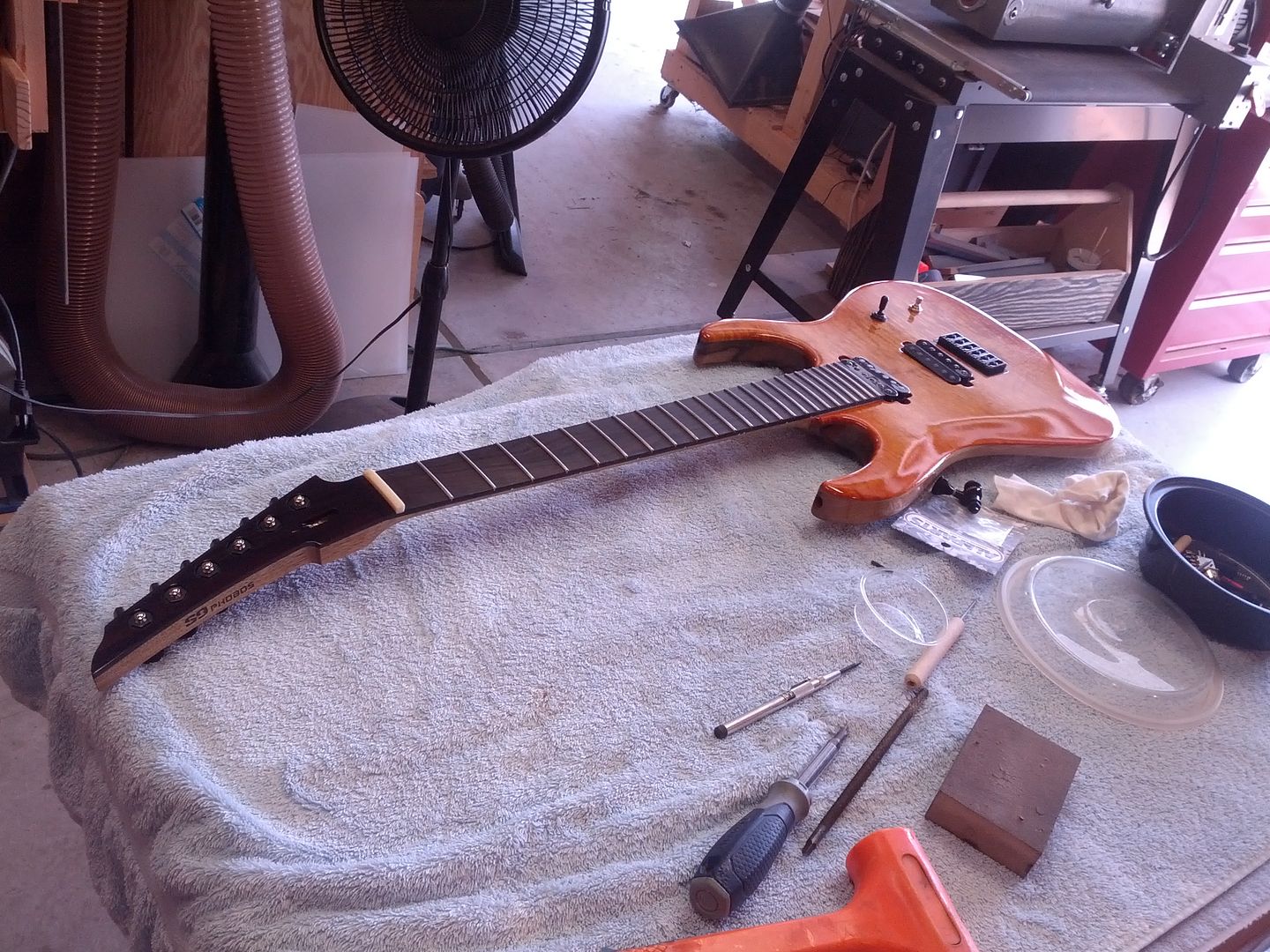
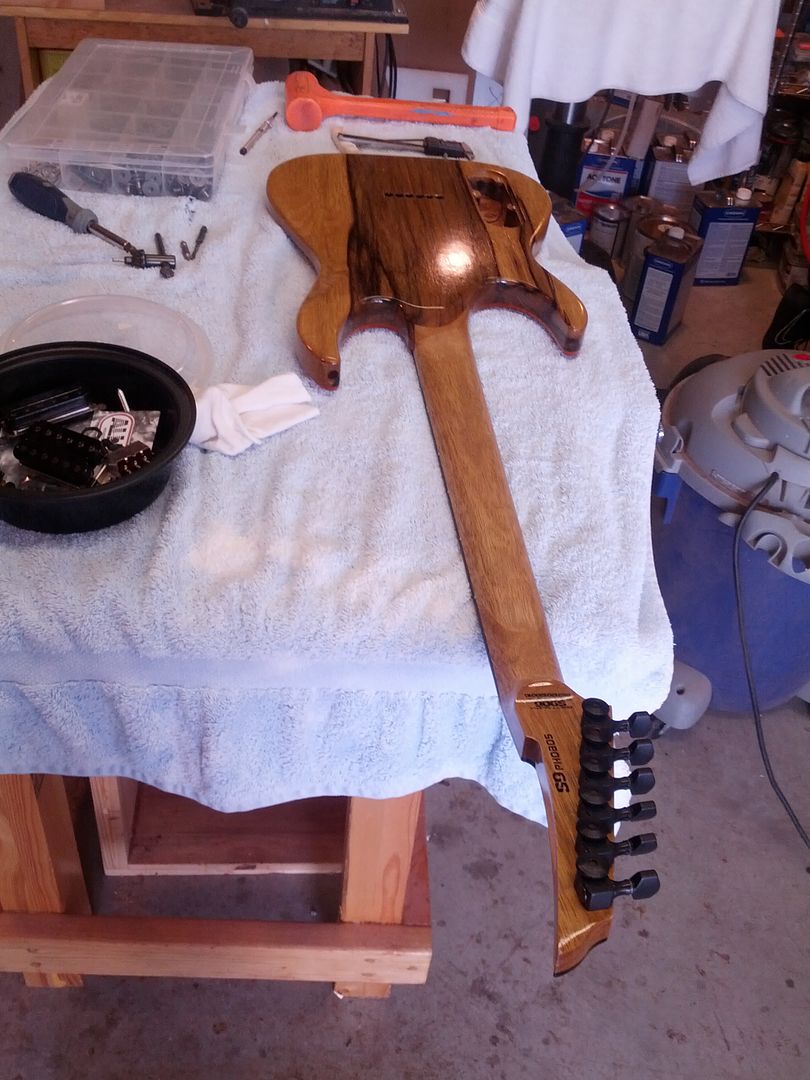
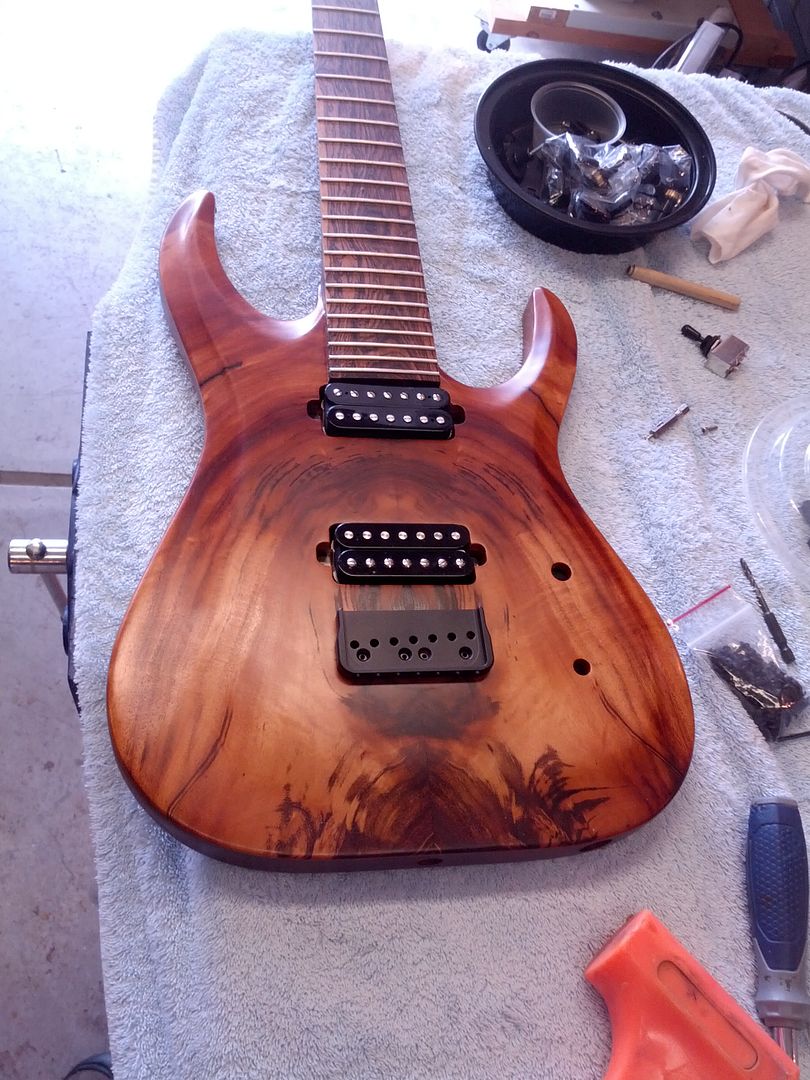
Next up its wookiee time.
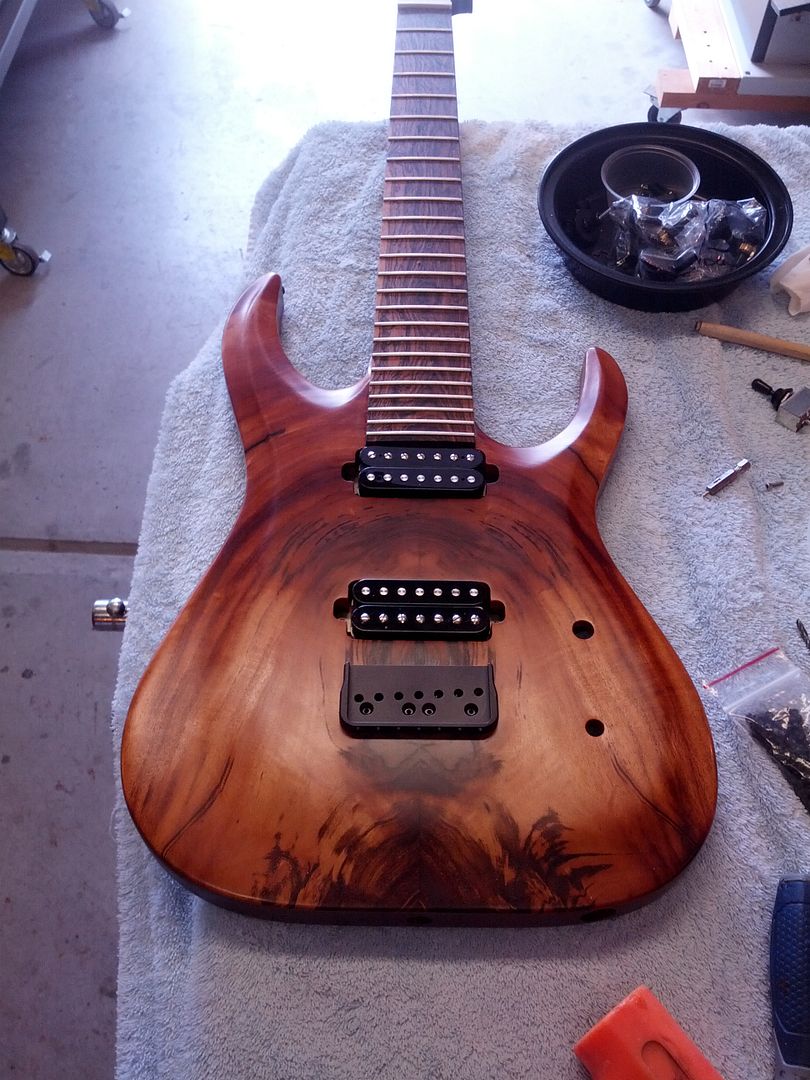
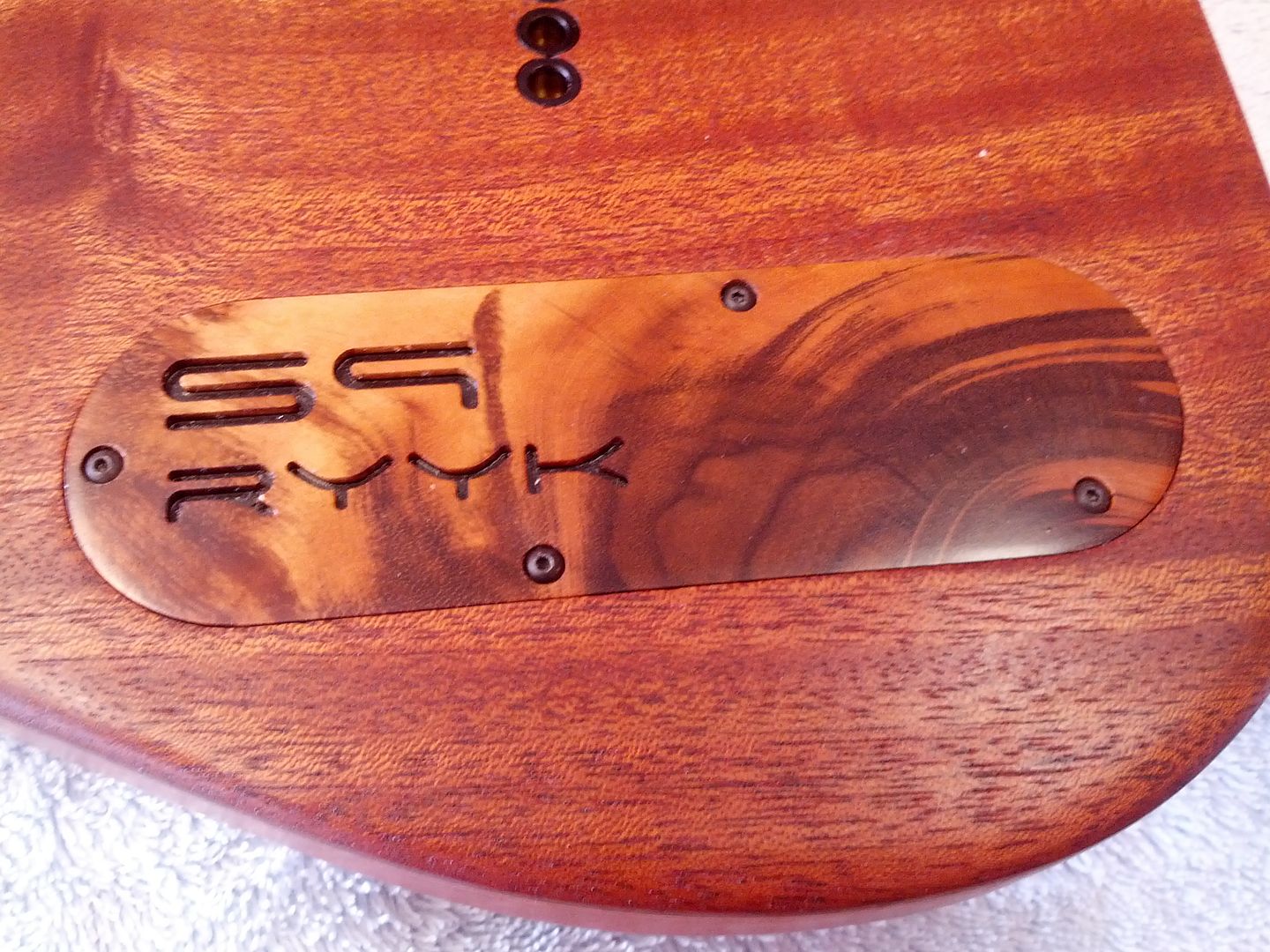
Got distracted... right in the middle of this some friends showed up for a tour of the shop. I will take some more shots this week.
Time to wrap up some builds.
Clear a spot for the ground wire
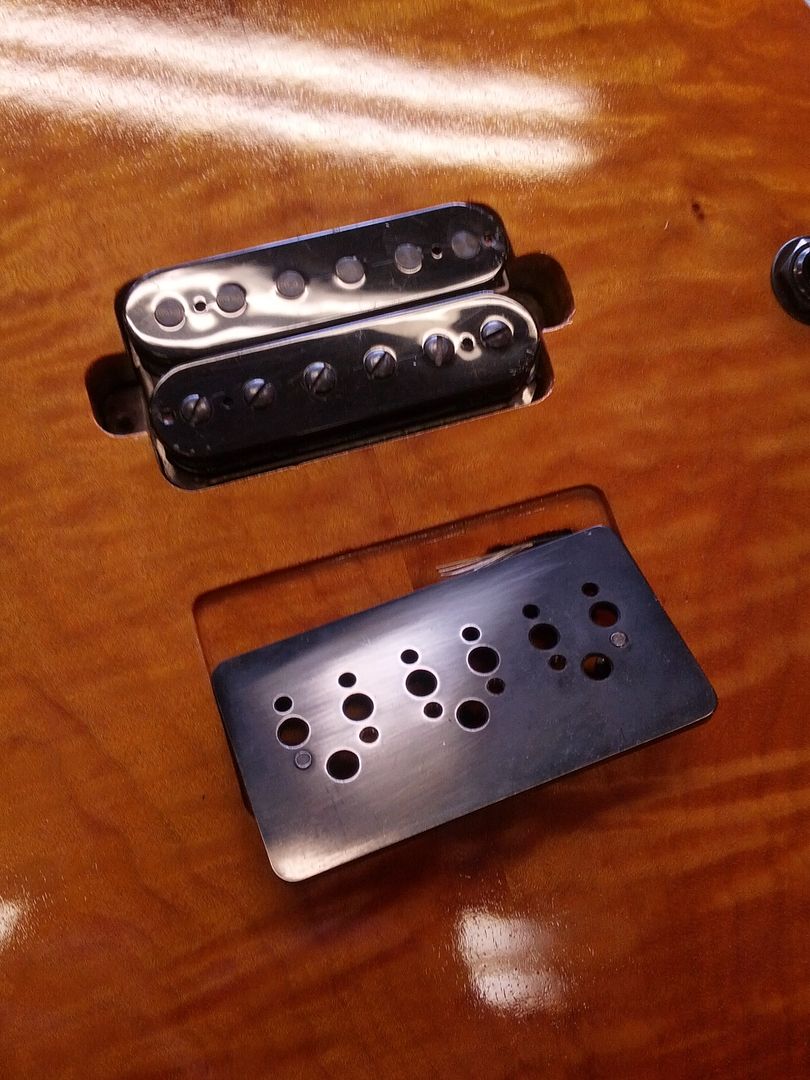
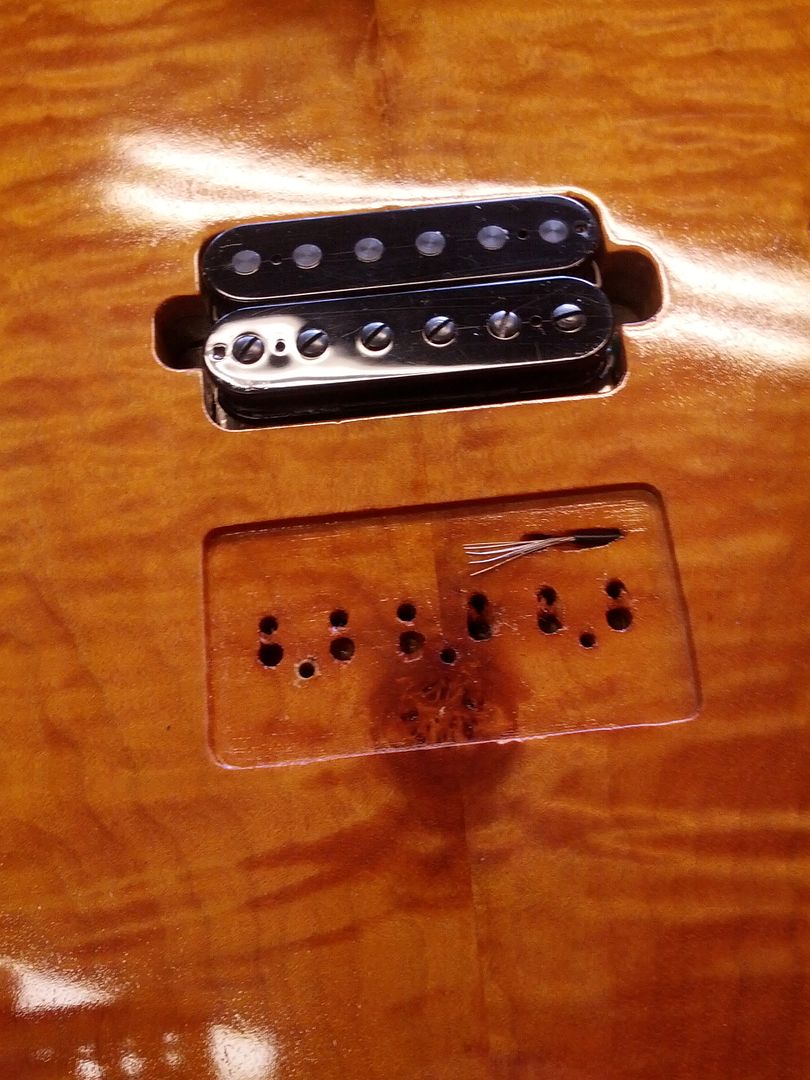
Recessed bridge plate fits nice and I like the all black pickups.
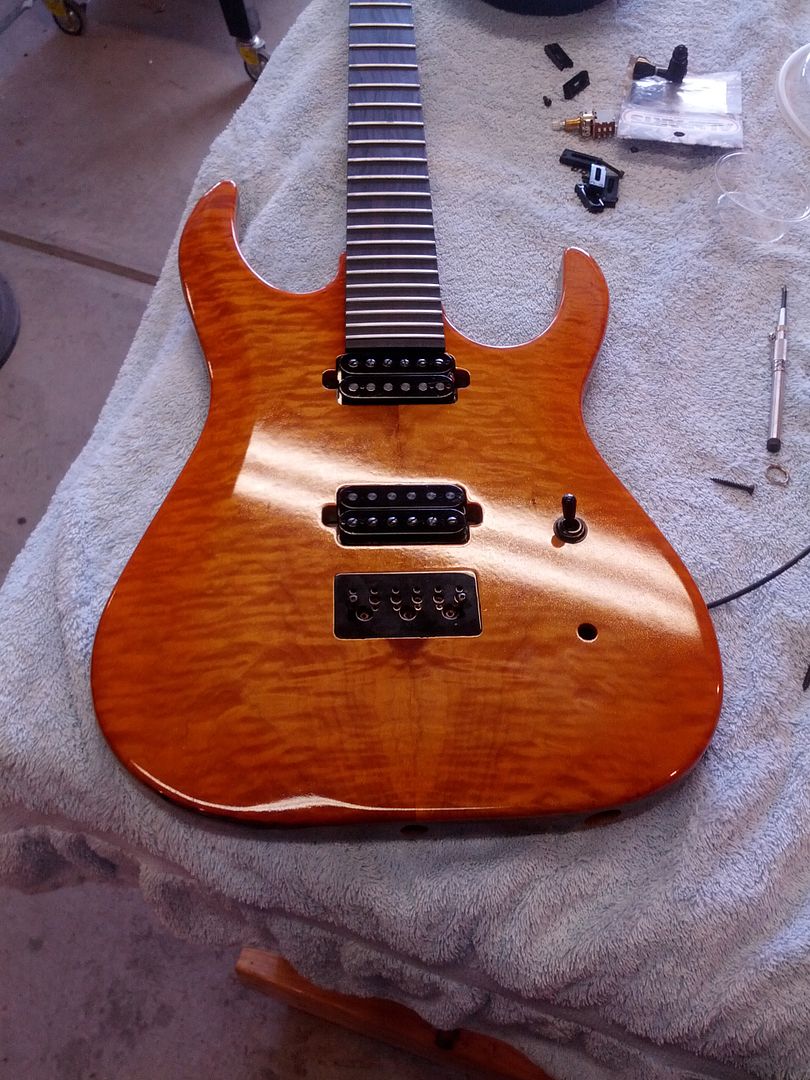
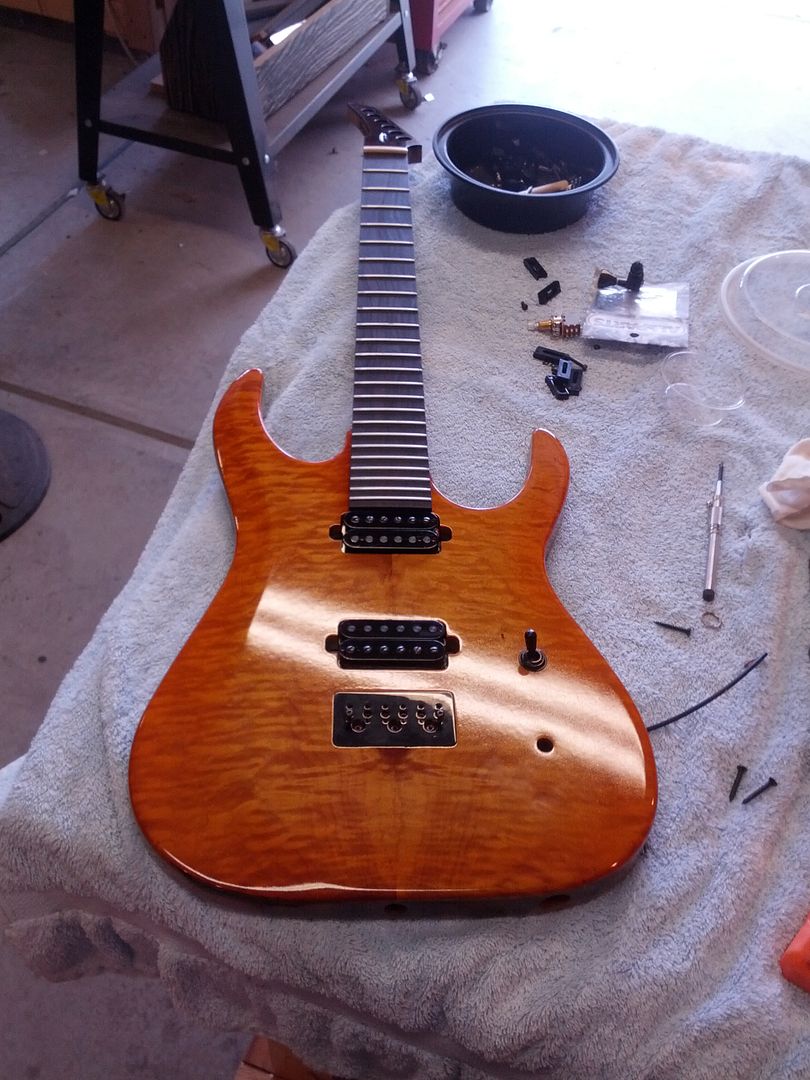
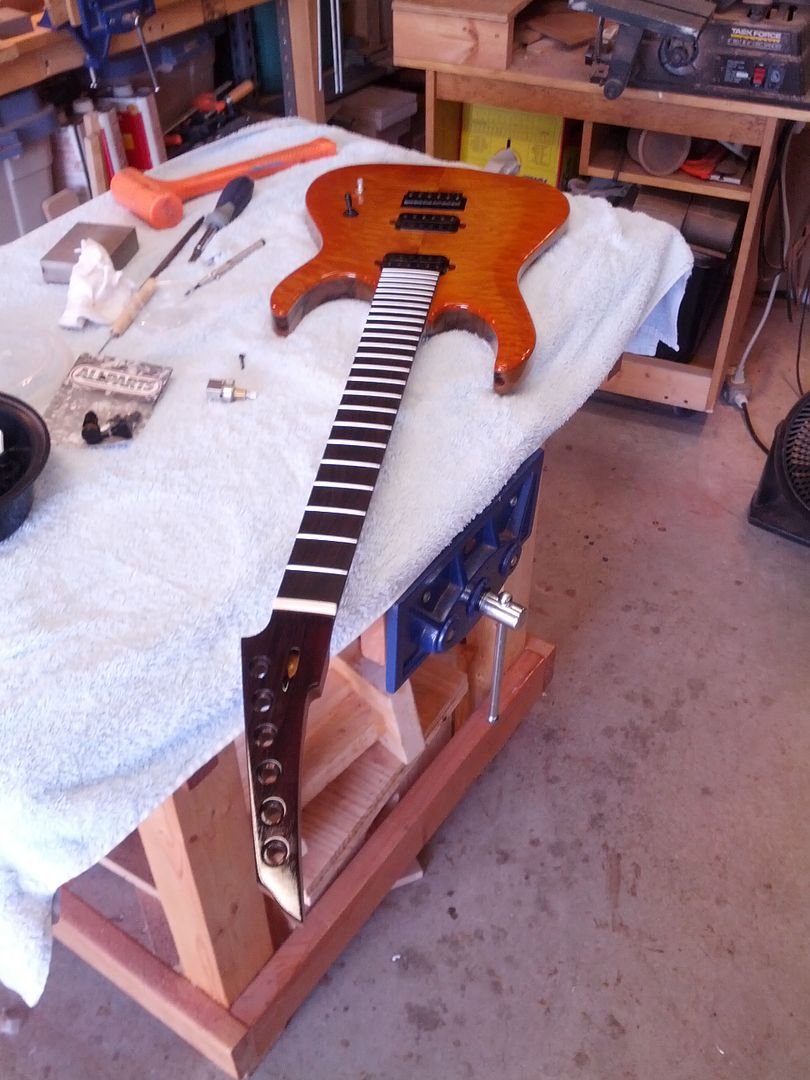
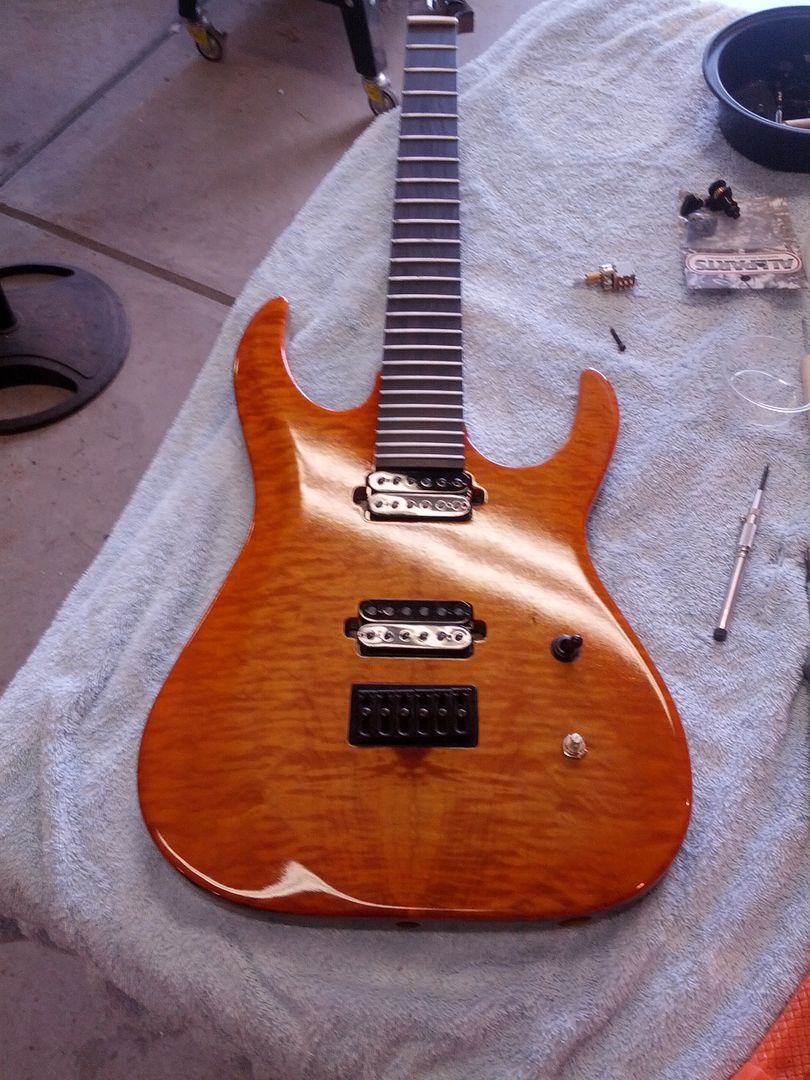
You know I will probably have to take this apart again but it is nice to get a good look at it.
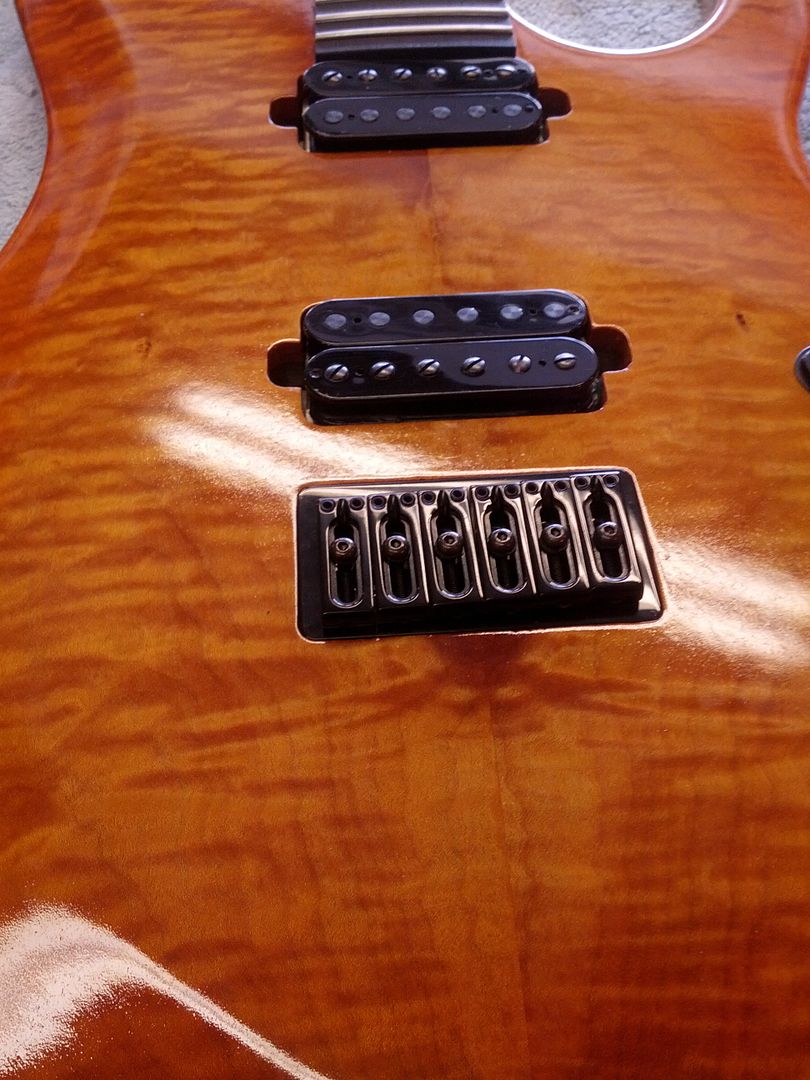
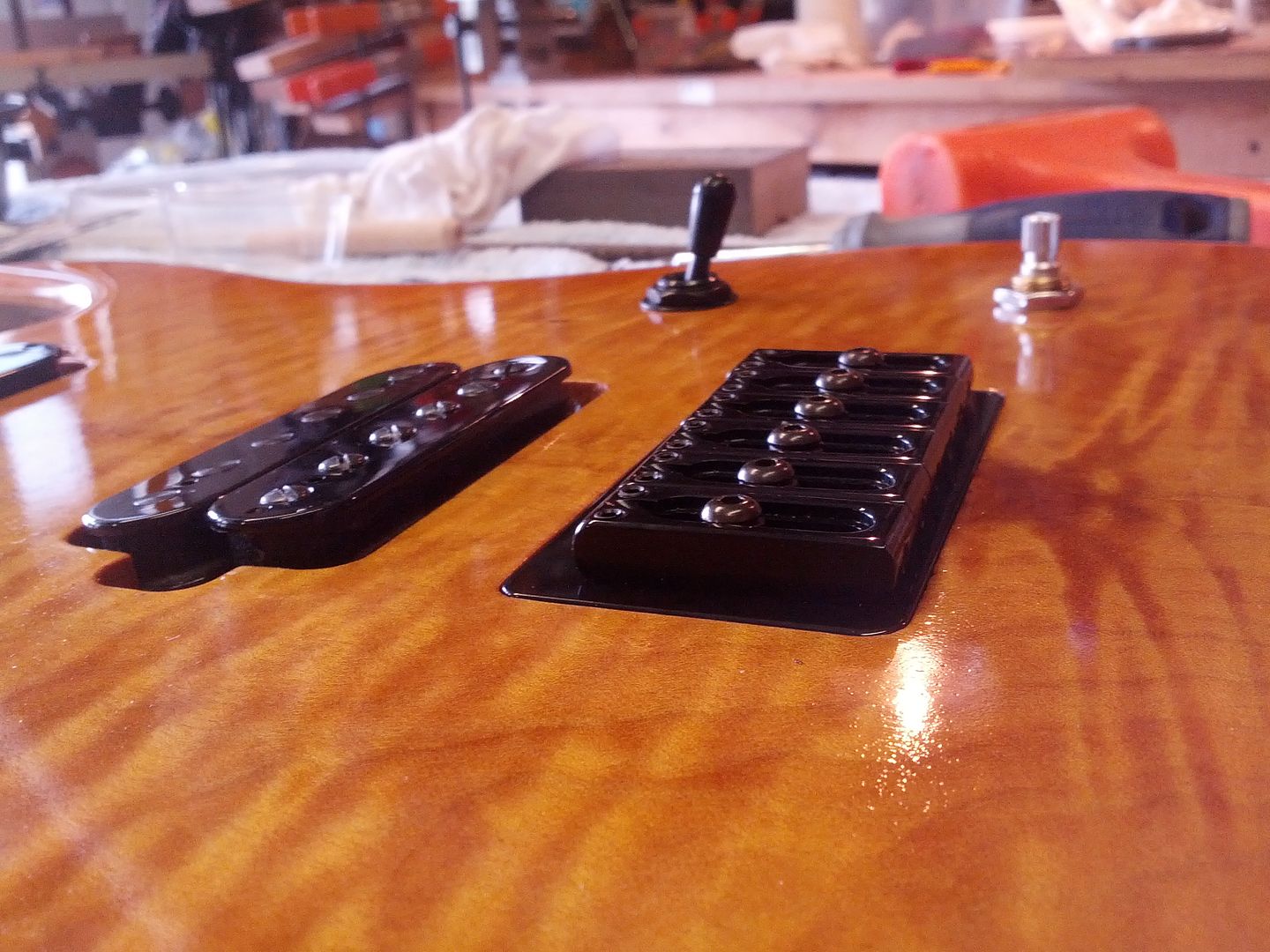
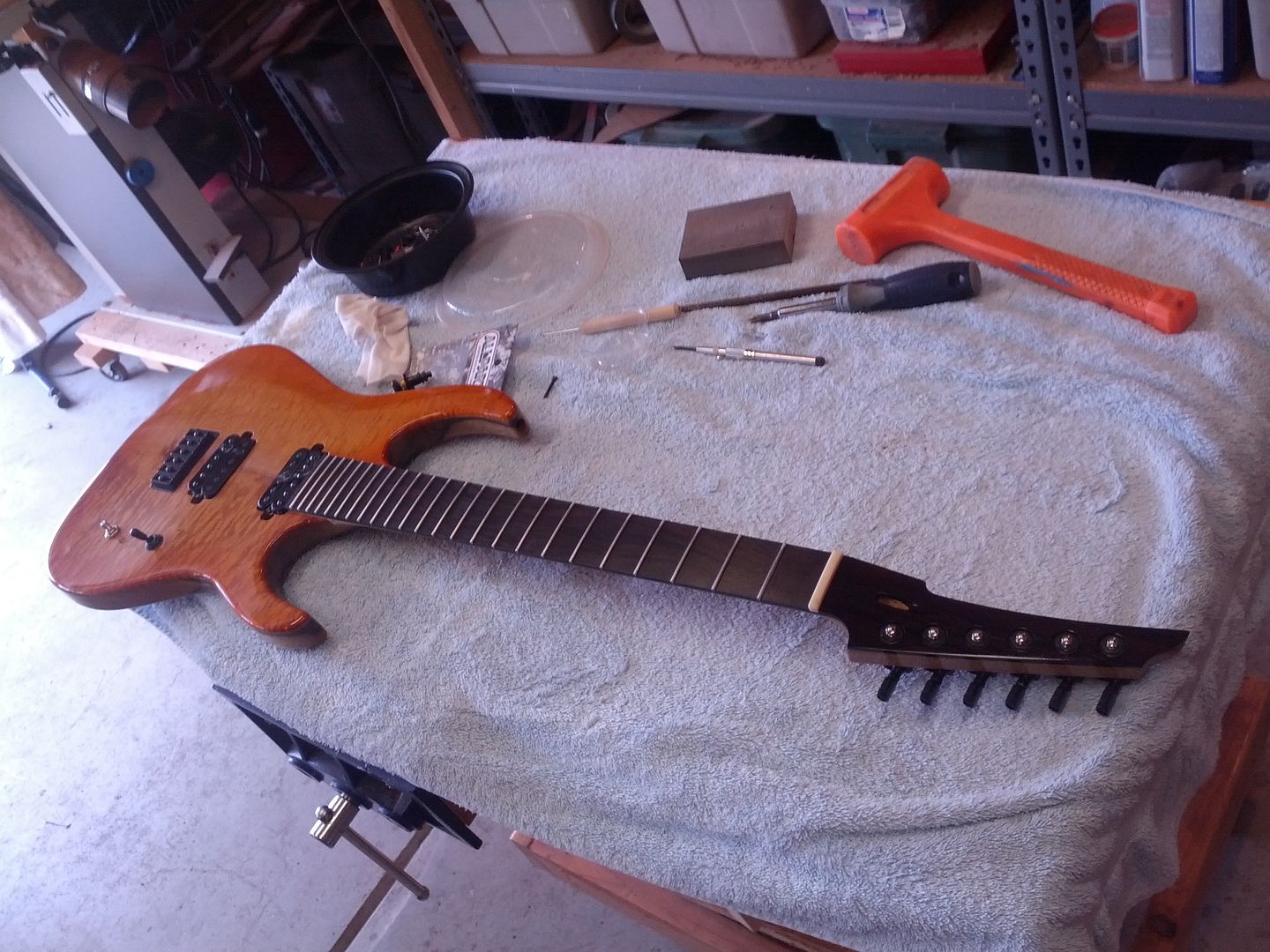
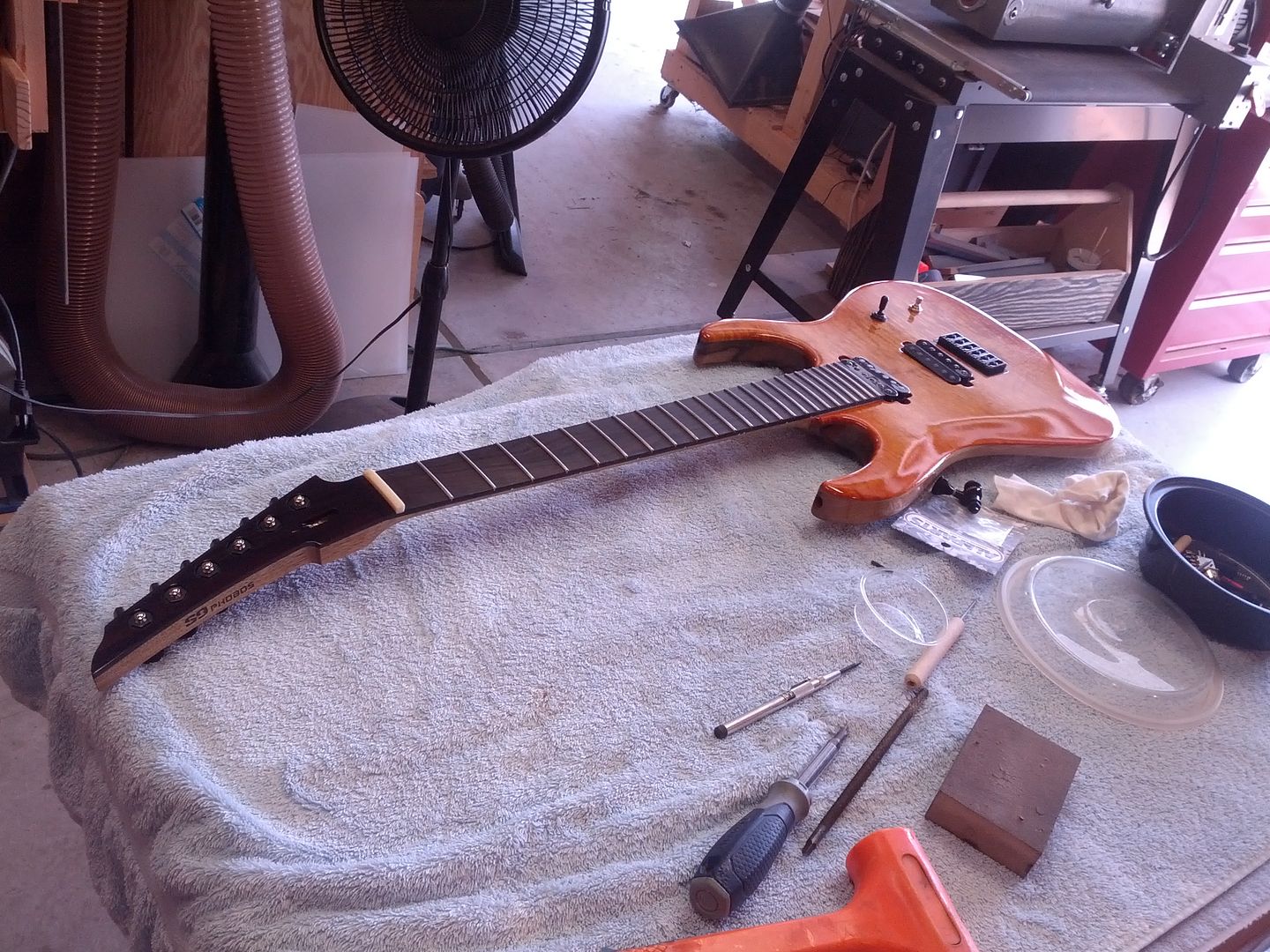
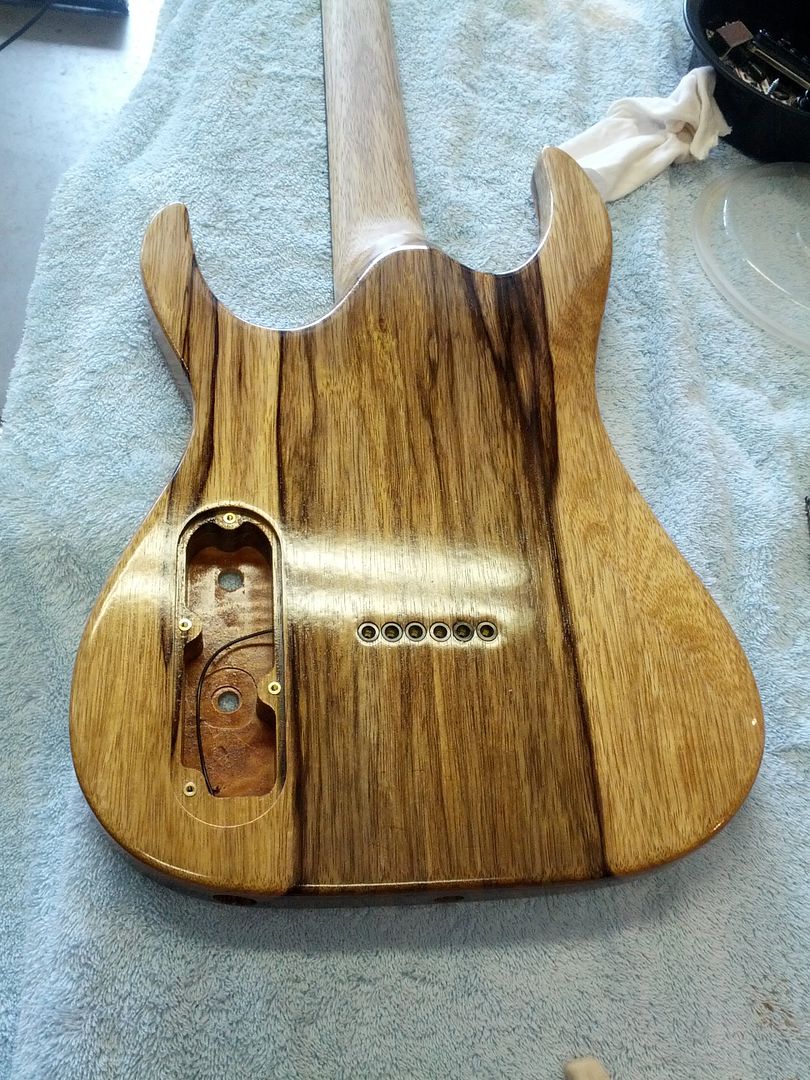
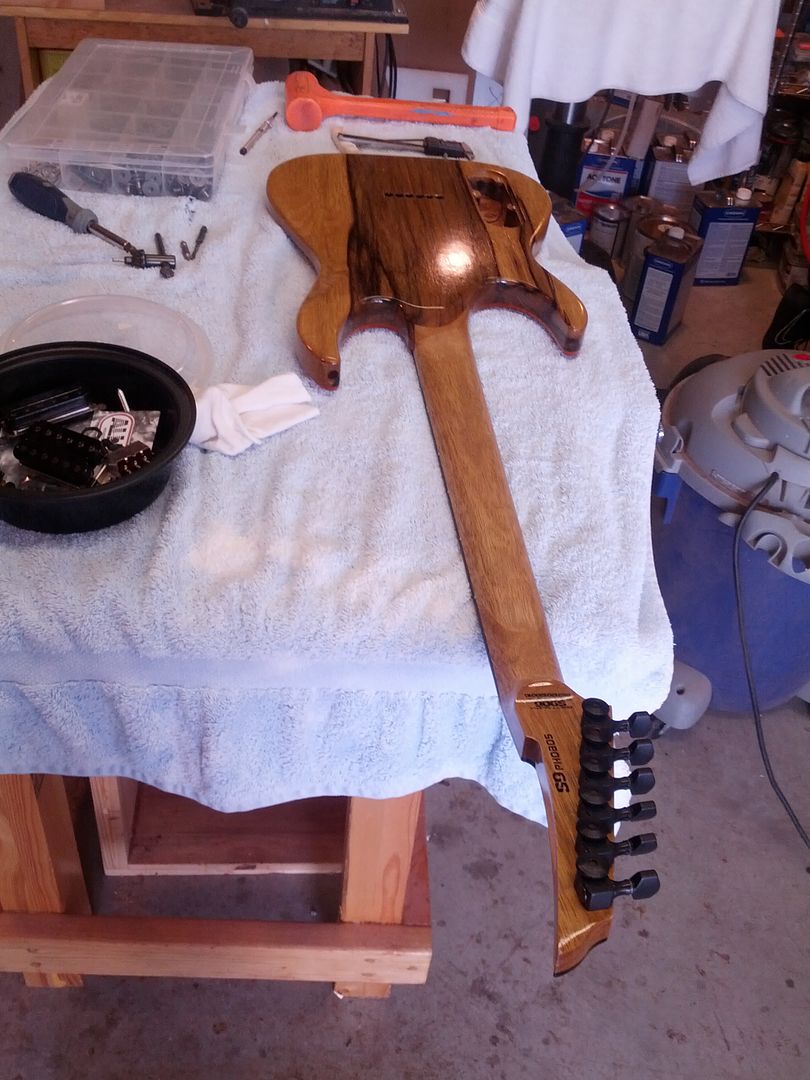
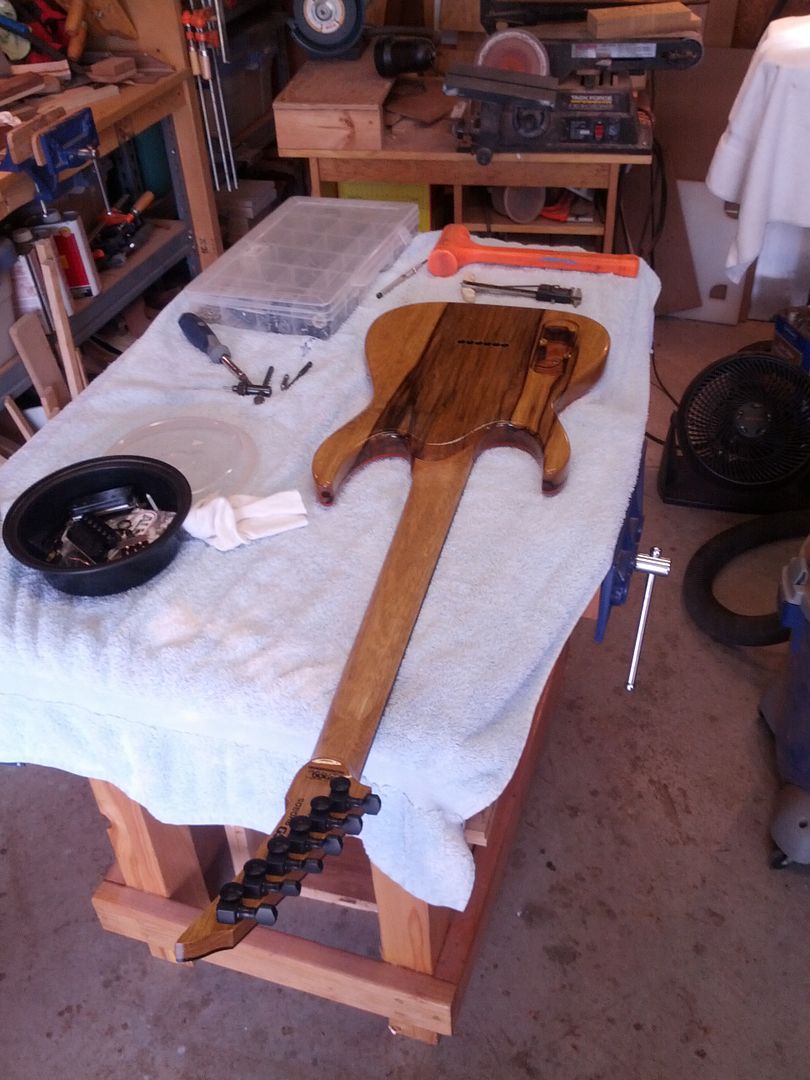
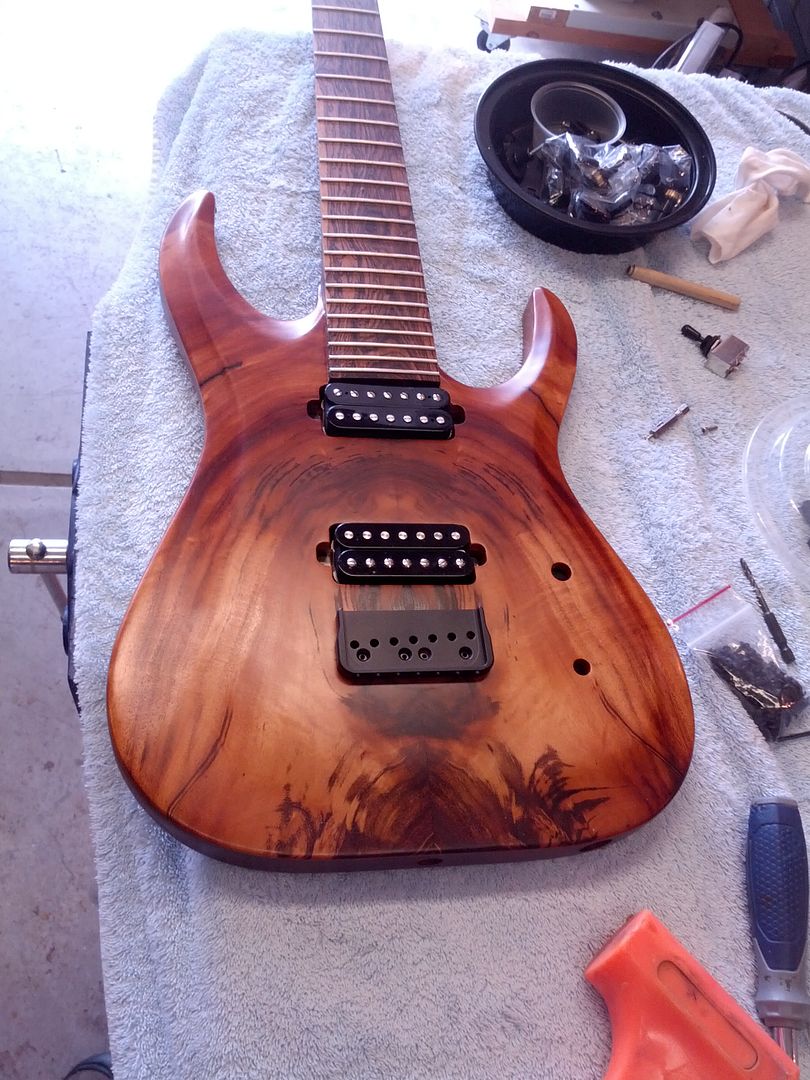
Next up its wookiee time.
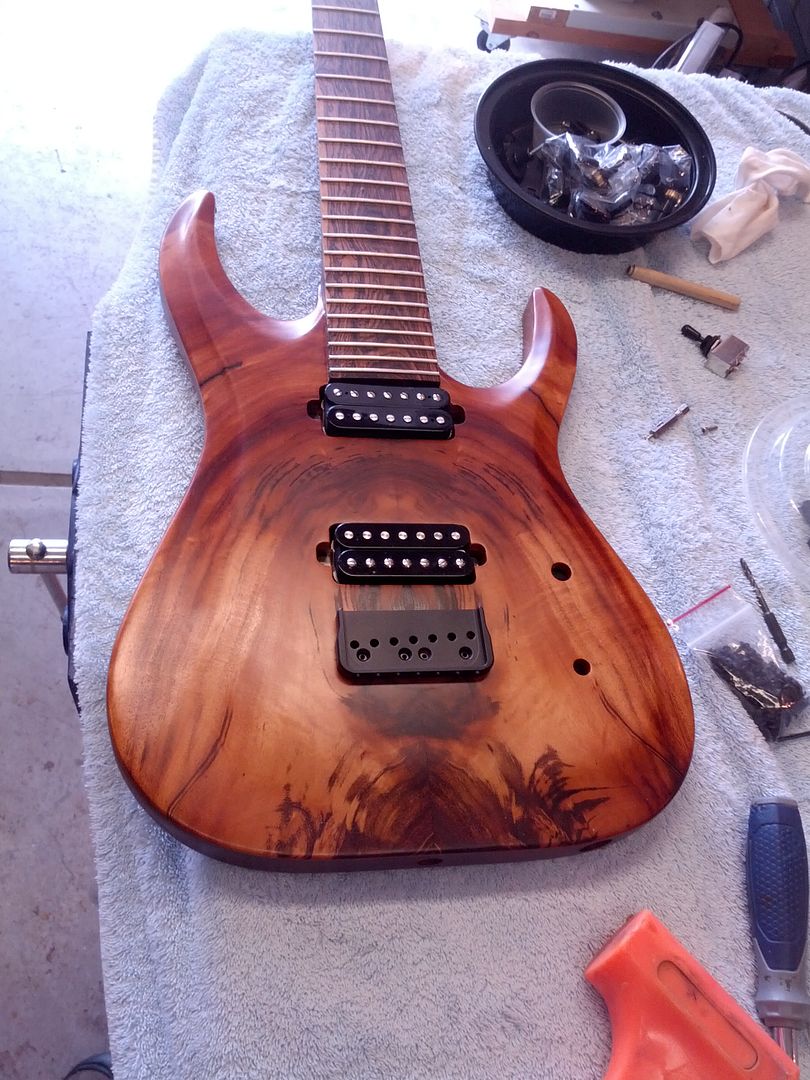
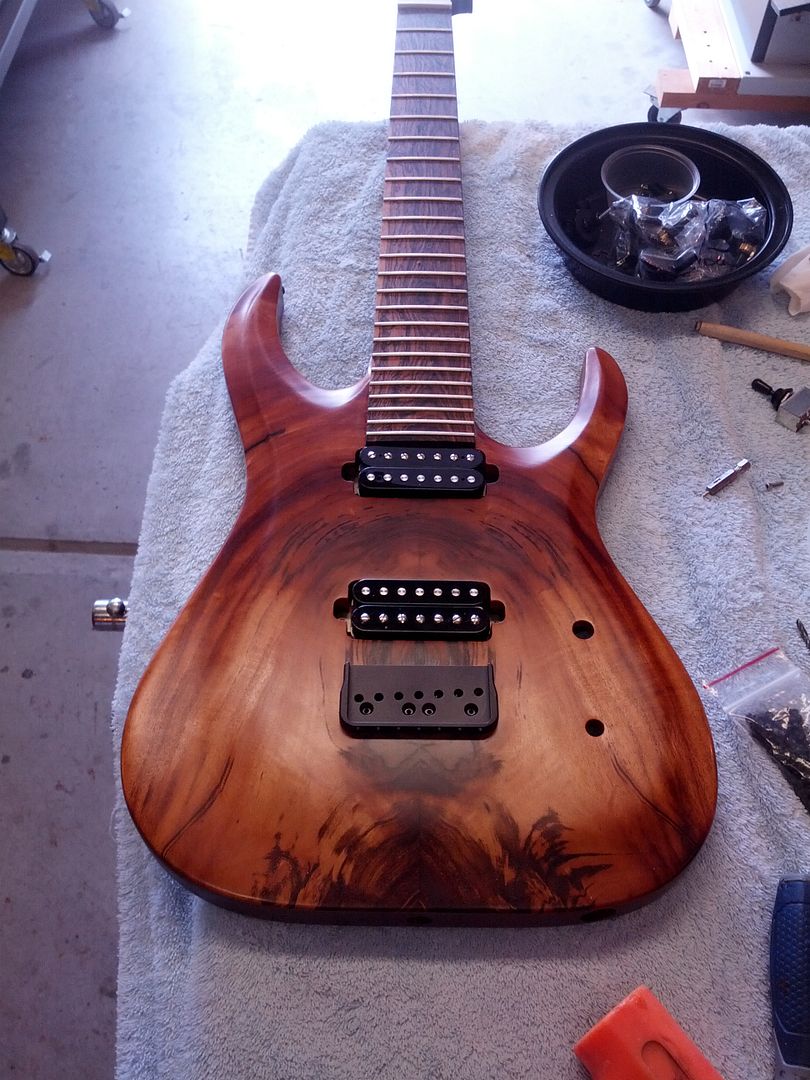
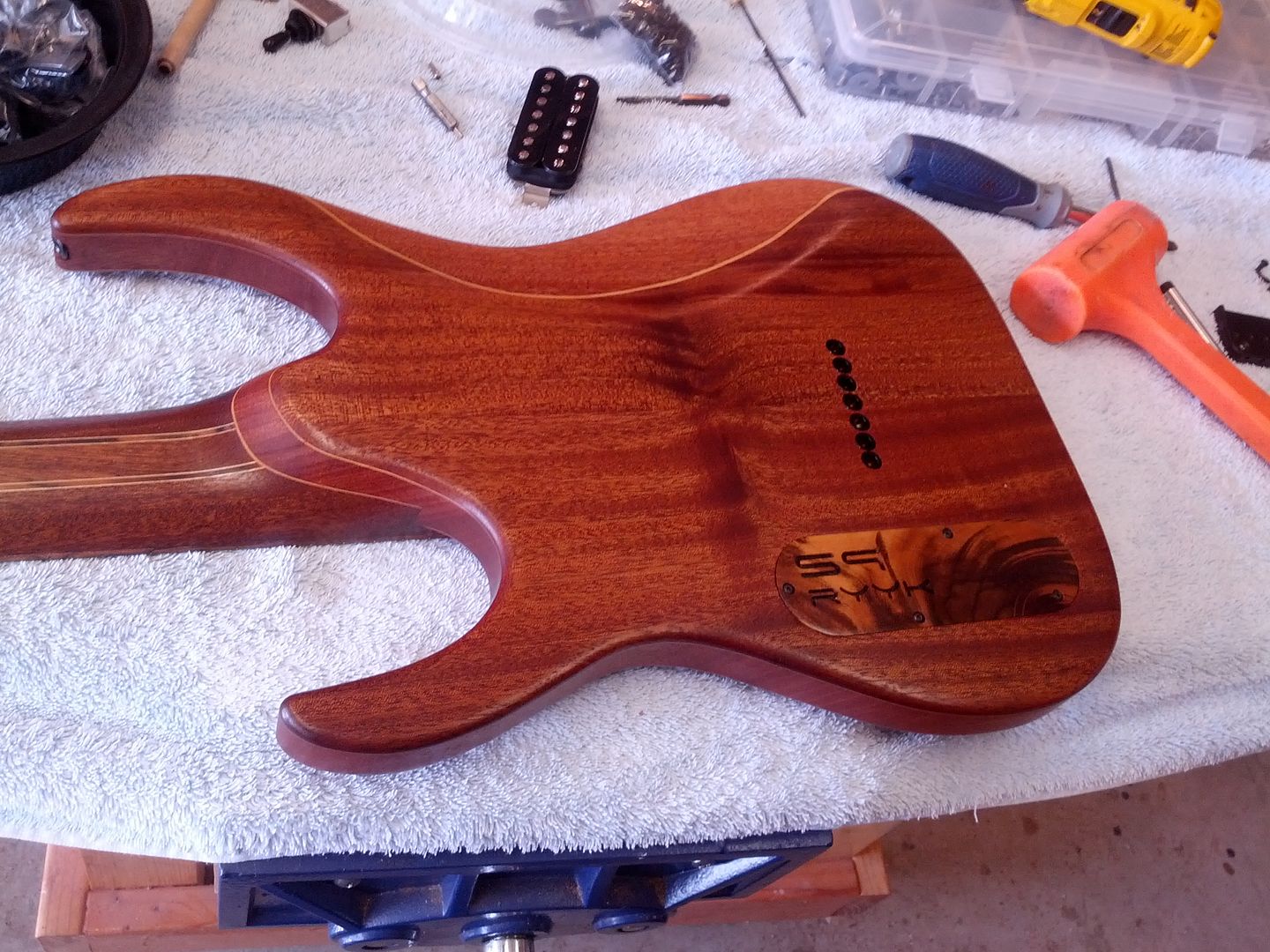
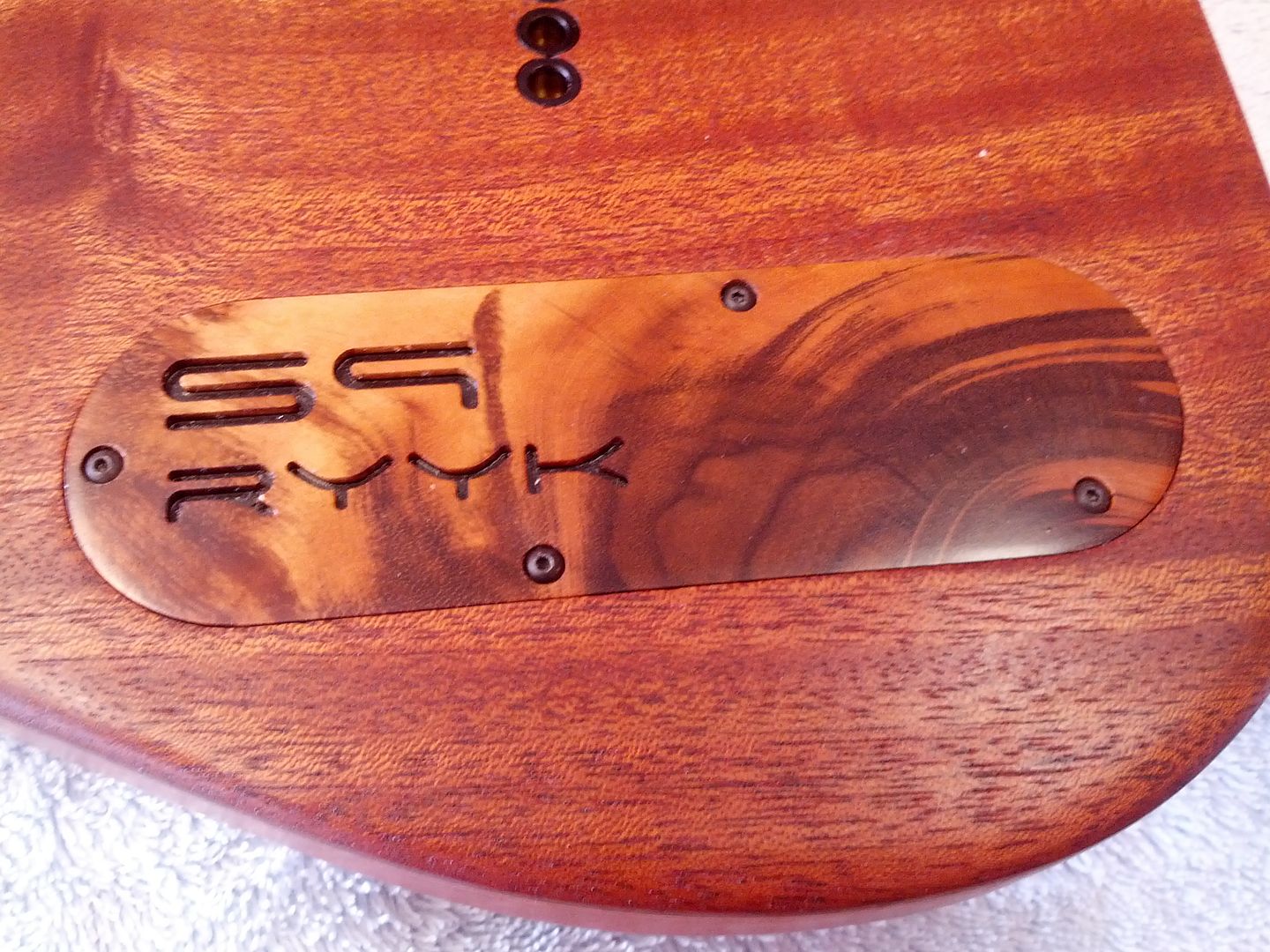
Got distracted... right in the middle of this some friends showed up for a tour of the shop. I will take some more shots this week.
Thursday, July 10, 2014
Caught in a mosh...
Solving the back of the guitar.
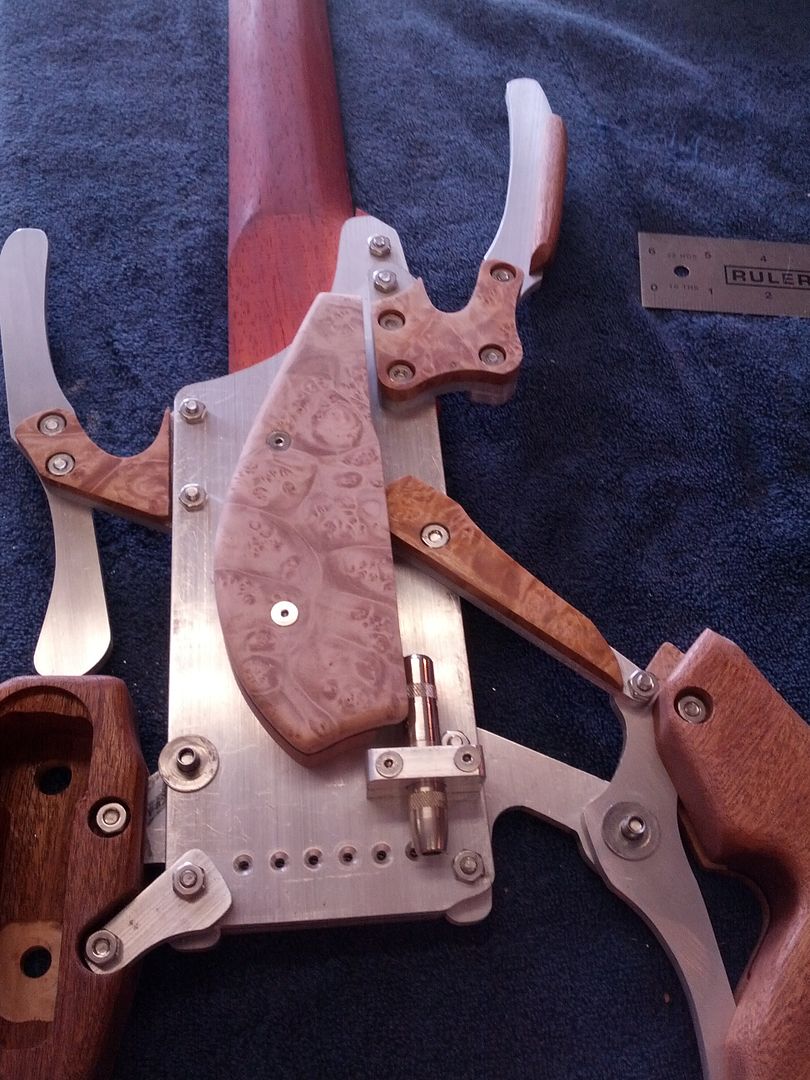
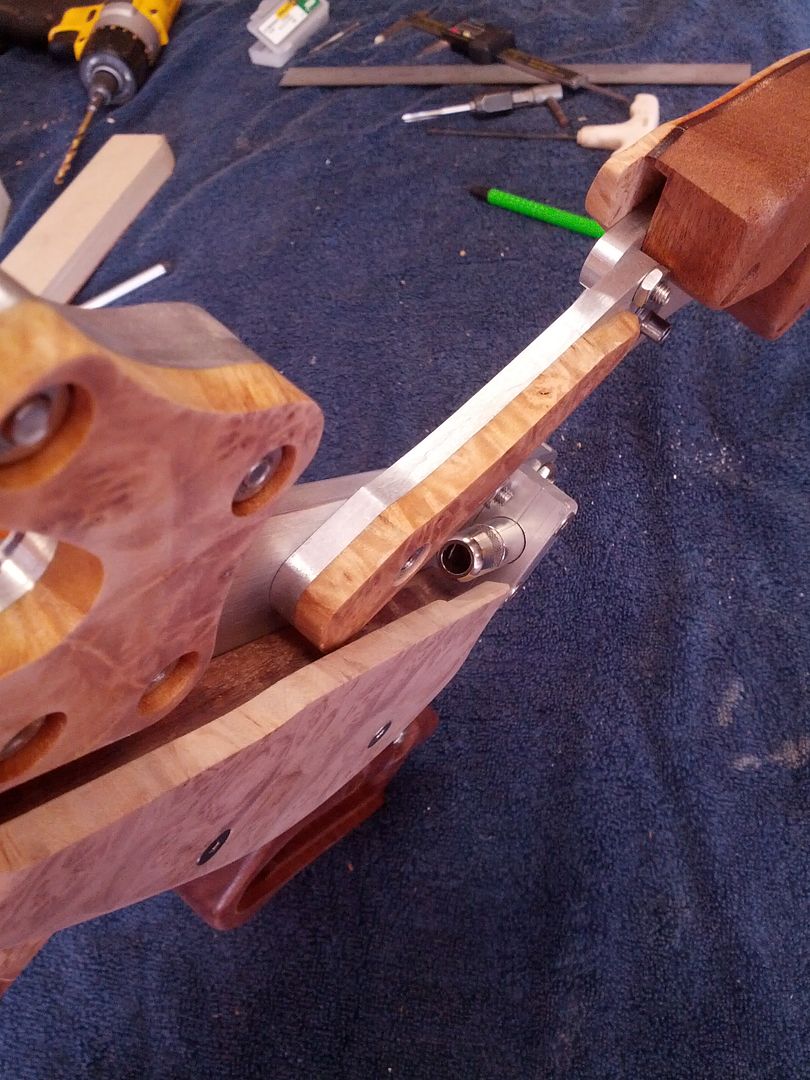
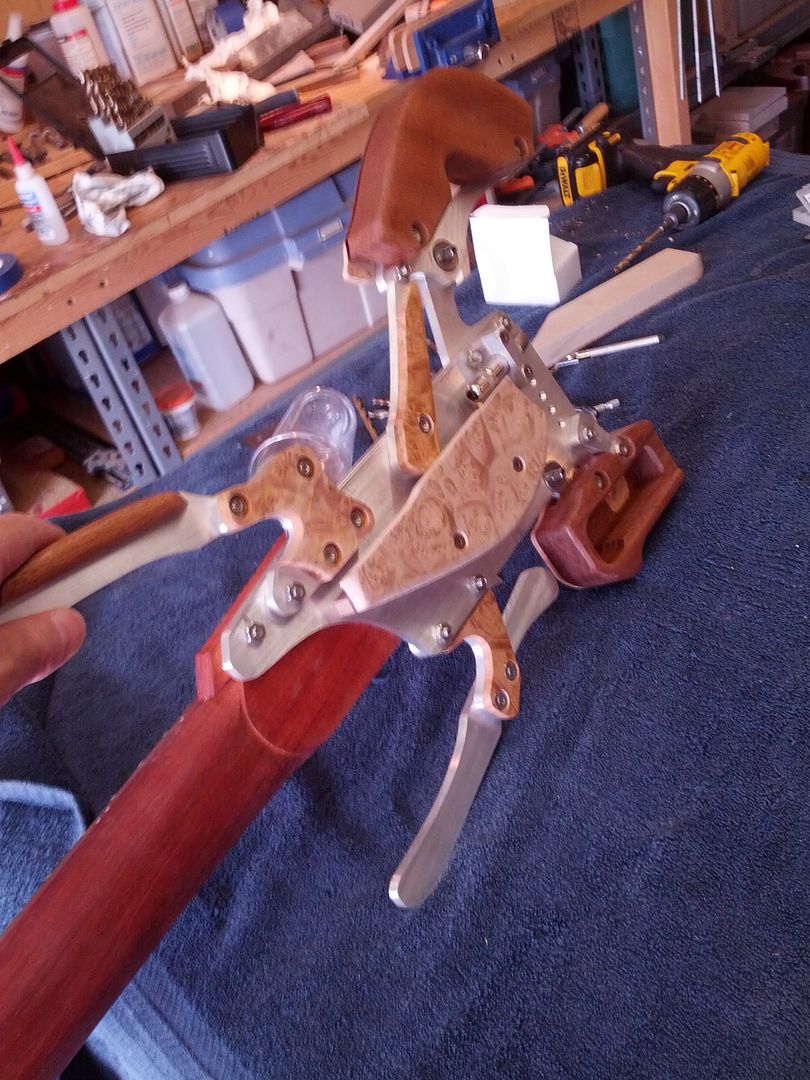
Clean up the neck and get it ready for oil
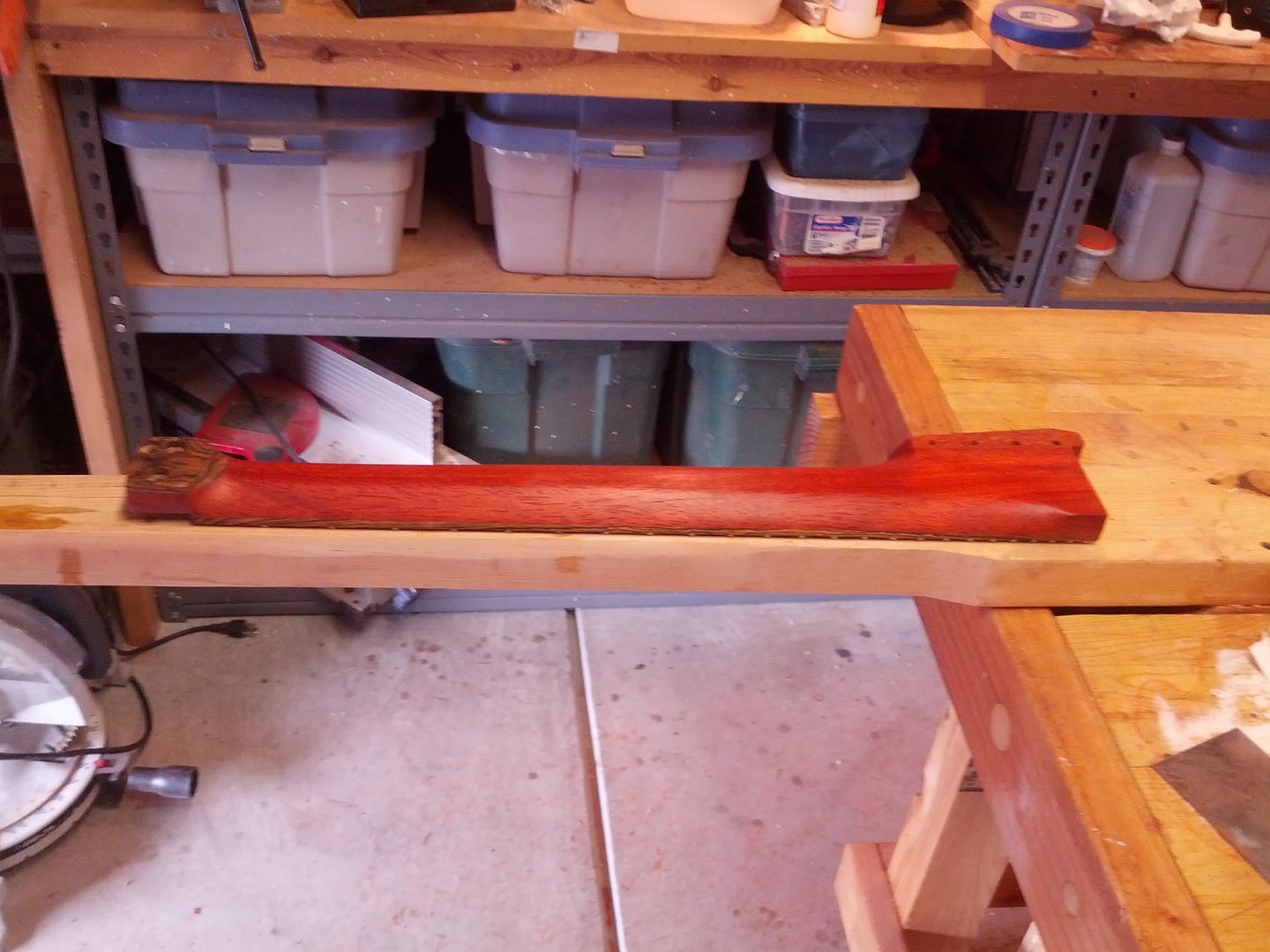
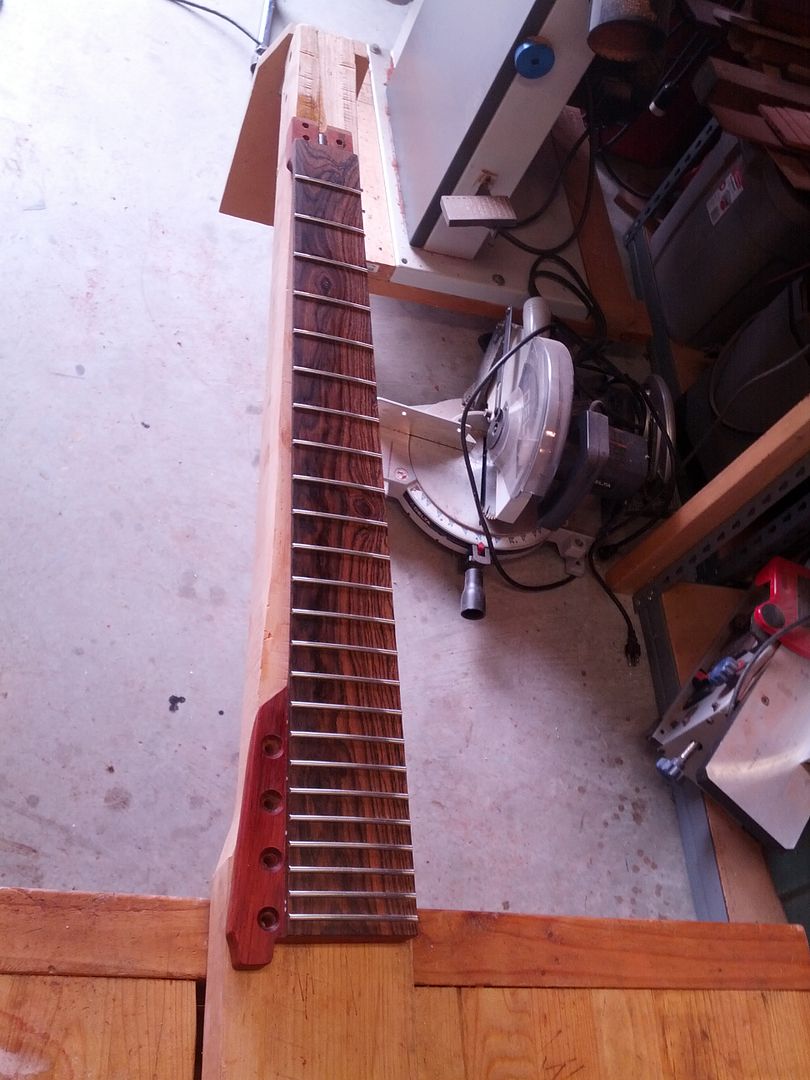
Decent upper fret access
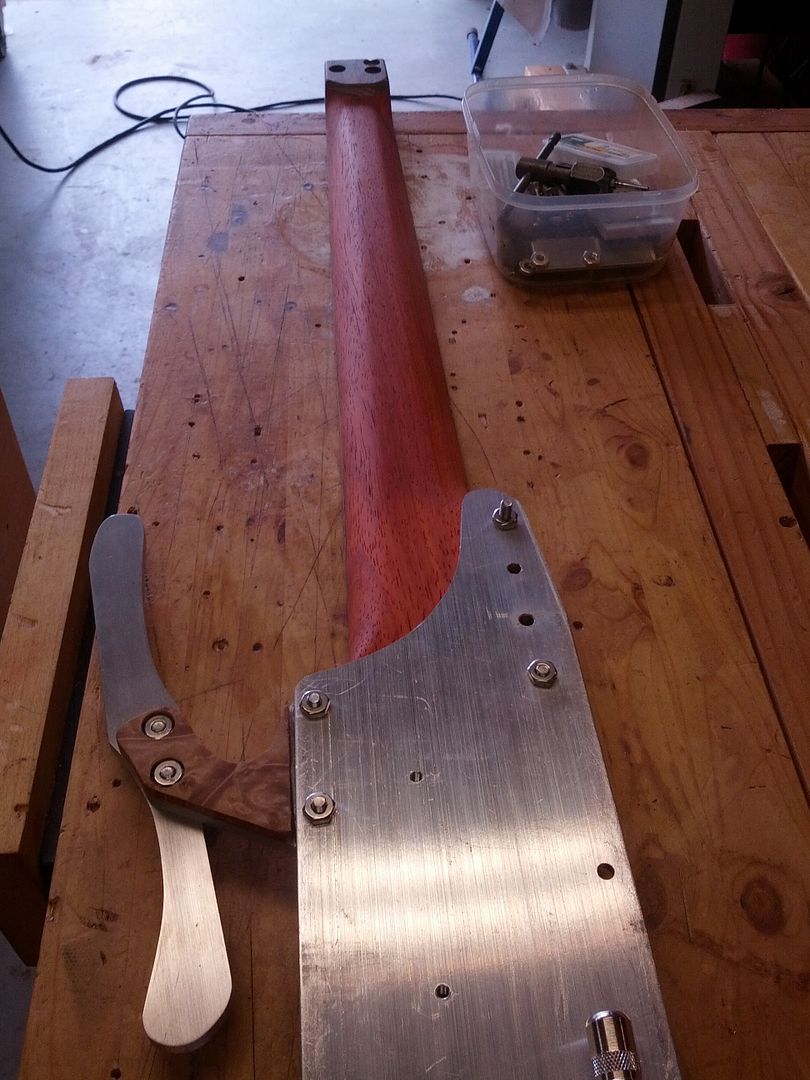
Getting everything lined up. Regular pickups are not going to fit. Concious decision to keep the guitar thin. The 65 year old design is not the only way to build a pickup.
Much thinner designed pickup fits fine. I have several designs that are very thin enough for this design.
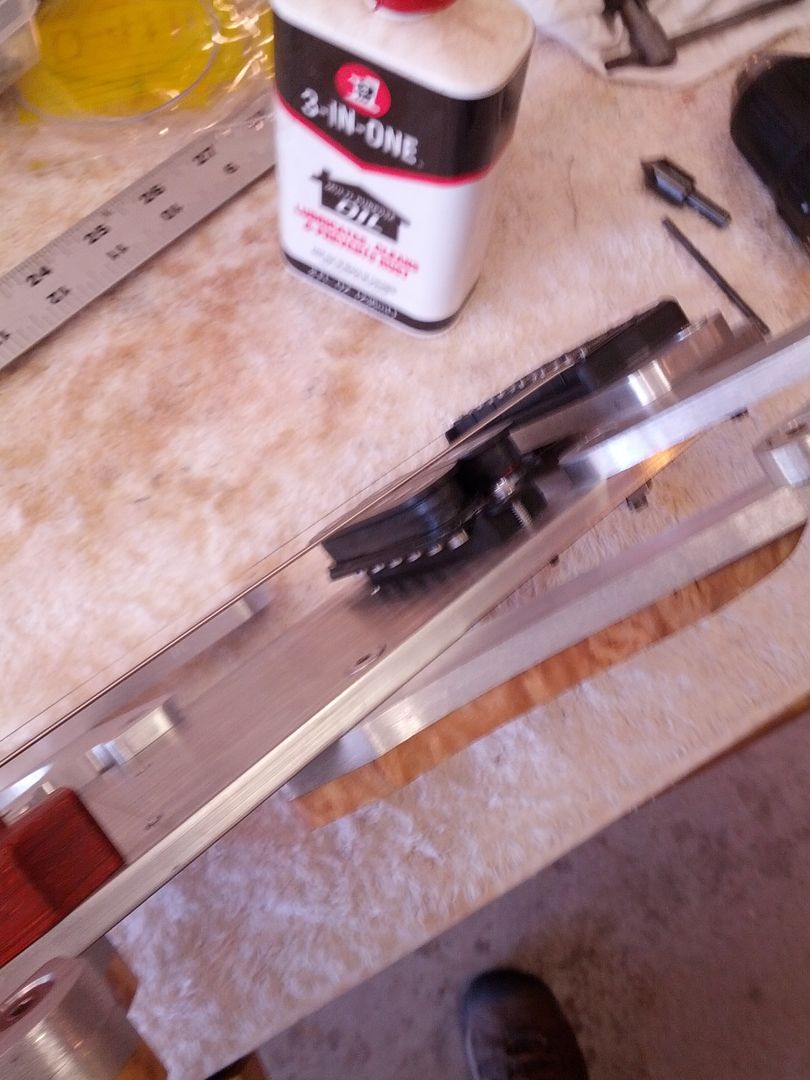
Mounting screws are tapped in to the plate. Long screws are not going to work well. The plate is .25" though so plenty of adjustment room without sticking out the back.
Shorter screws
Tuners installed
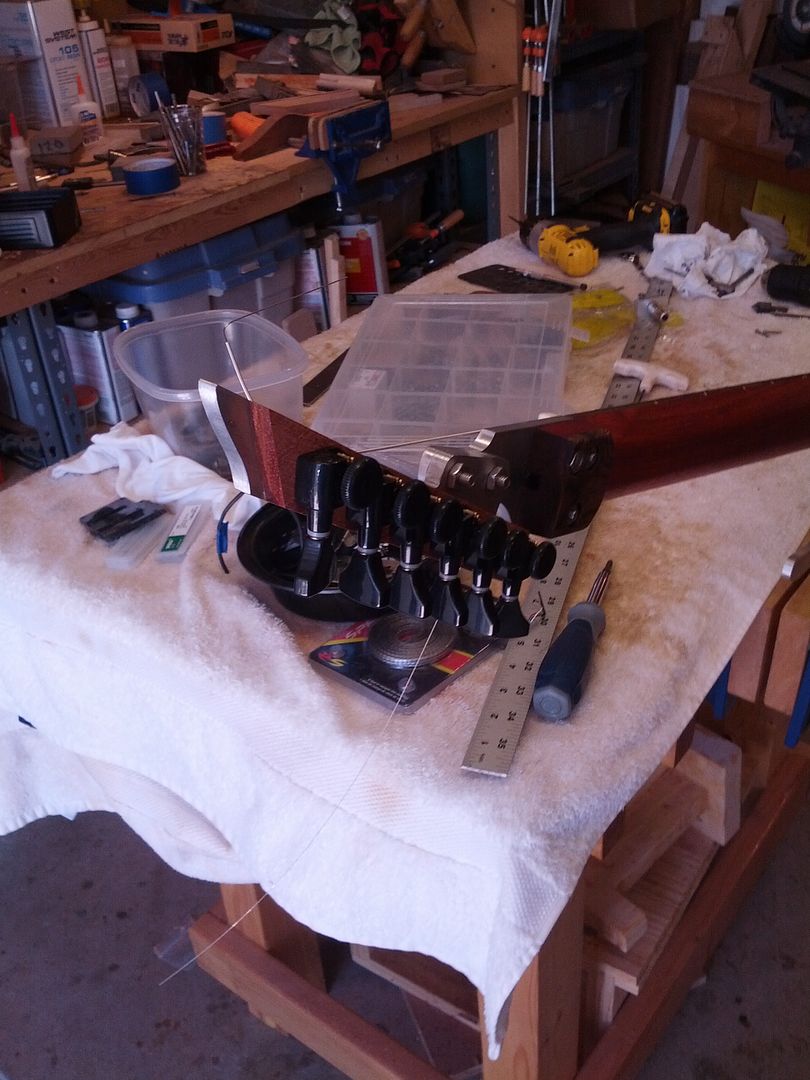
Closer. I did not get the string pull perfectly straight and there is a bit of fan in the strings after the nut. Good thing is it is realatively easy to make a new head piece. Heck of a lot easier than on an S9 set neck.
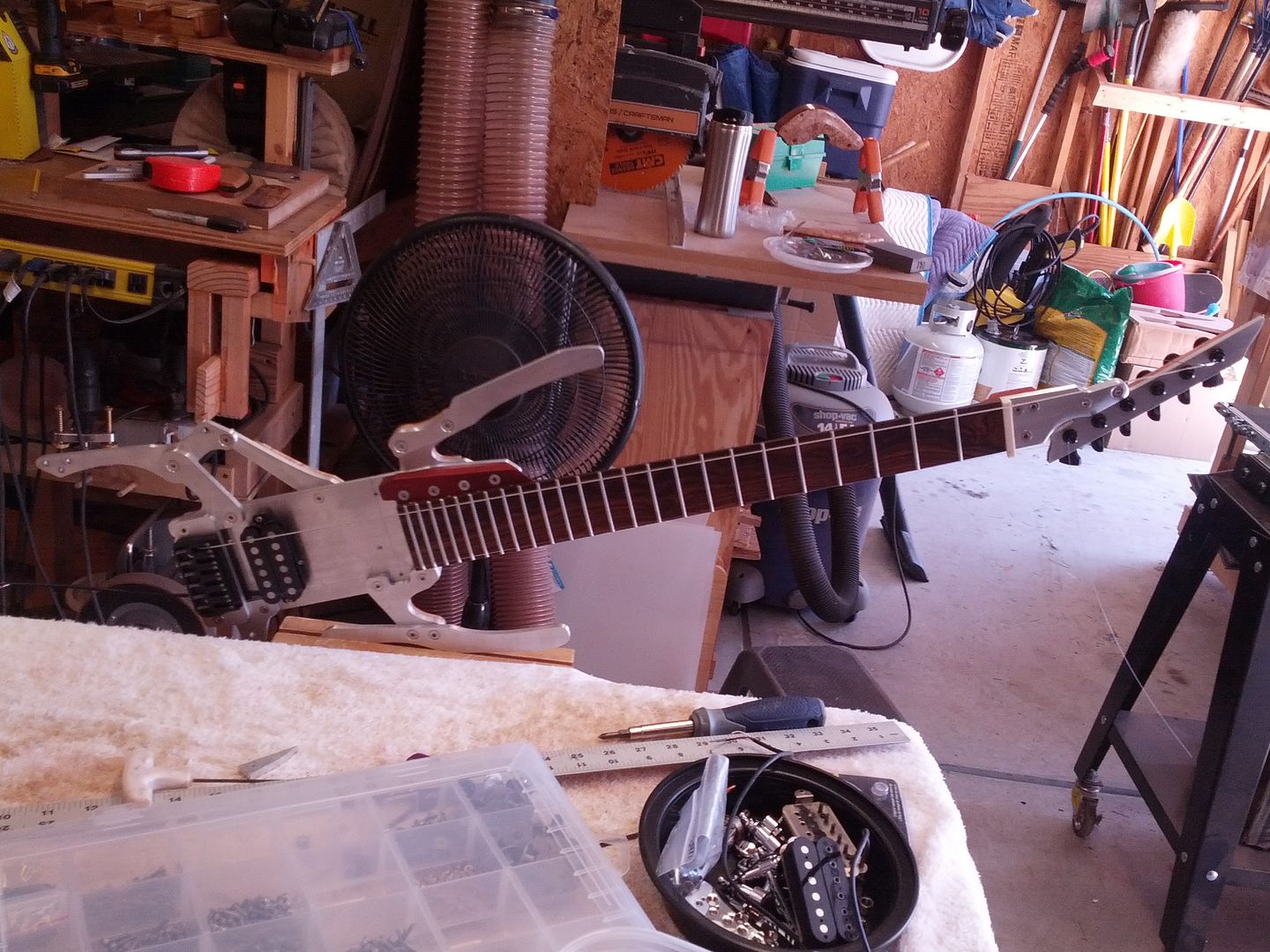
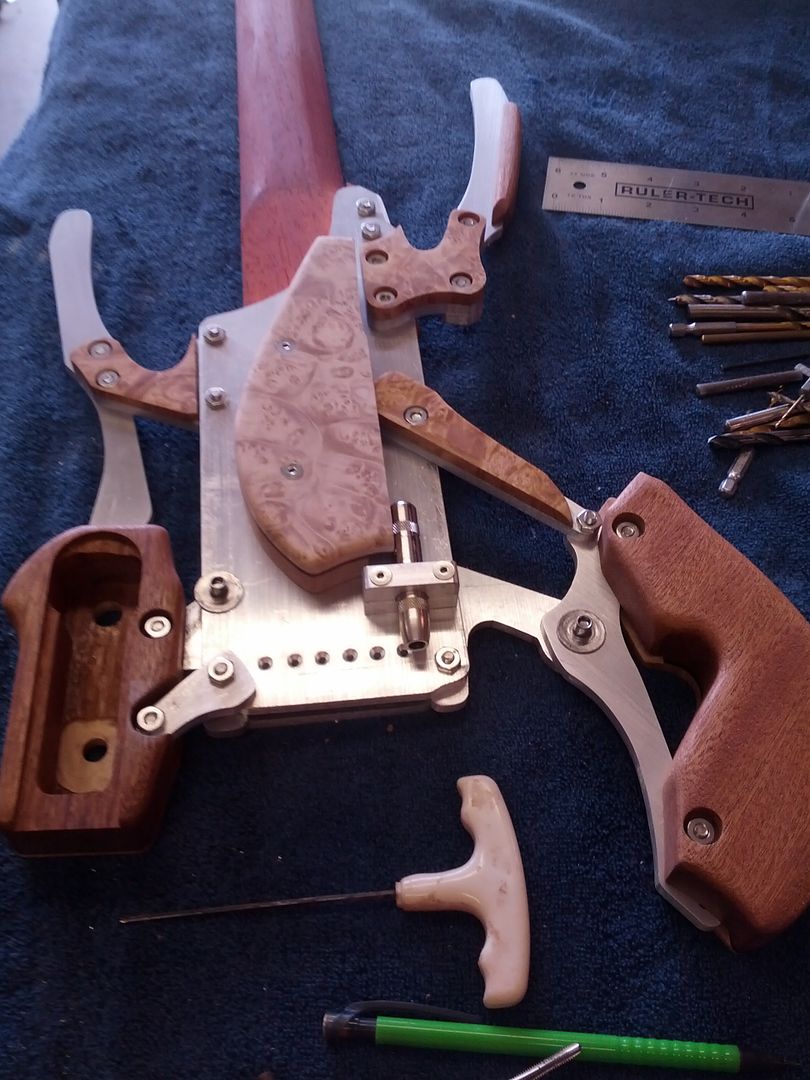
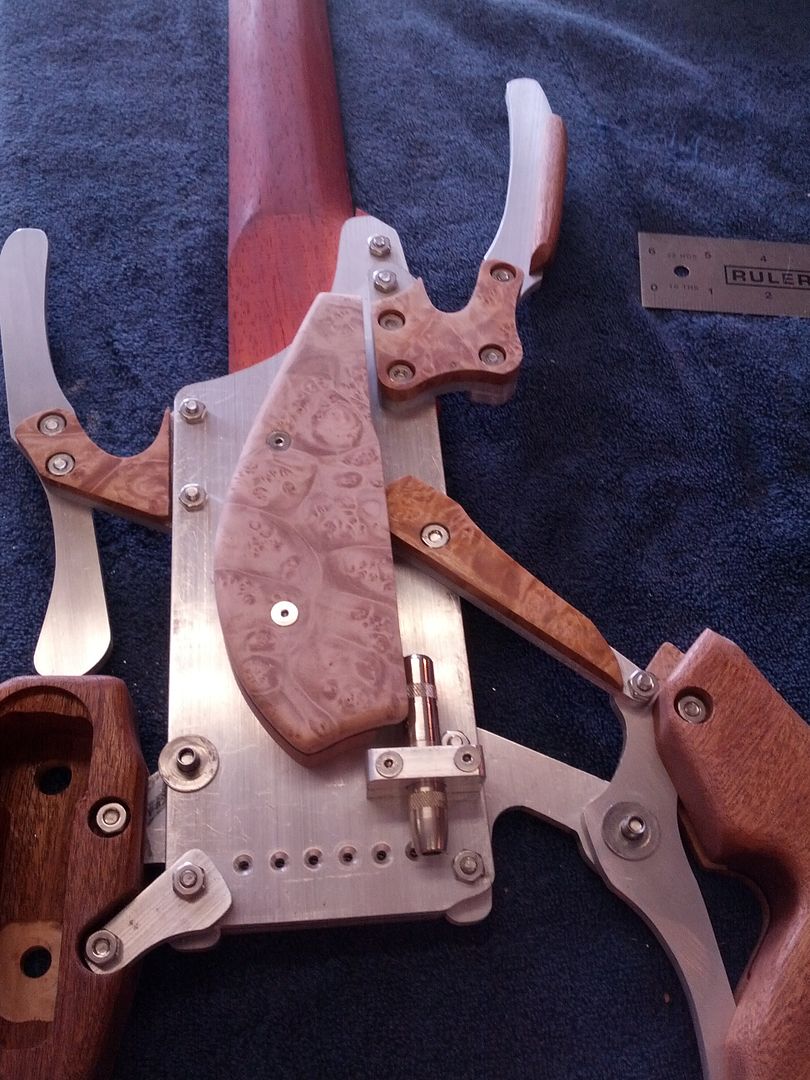
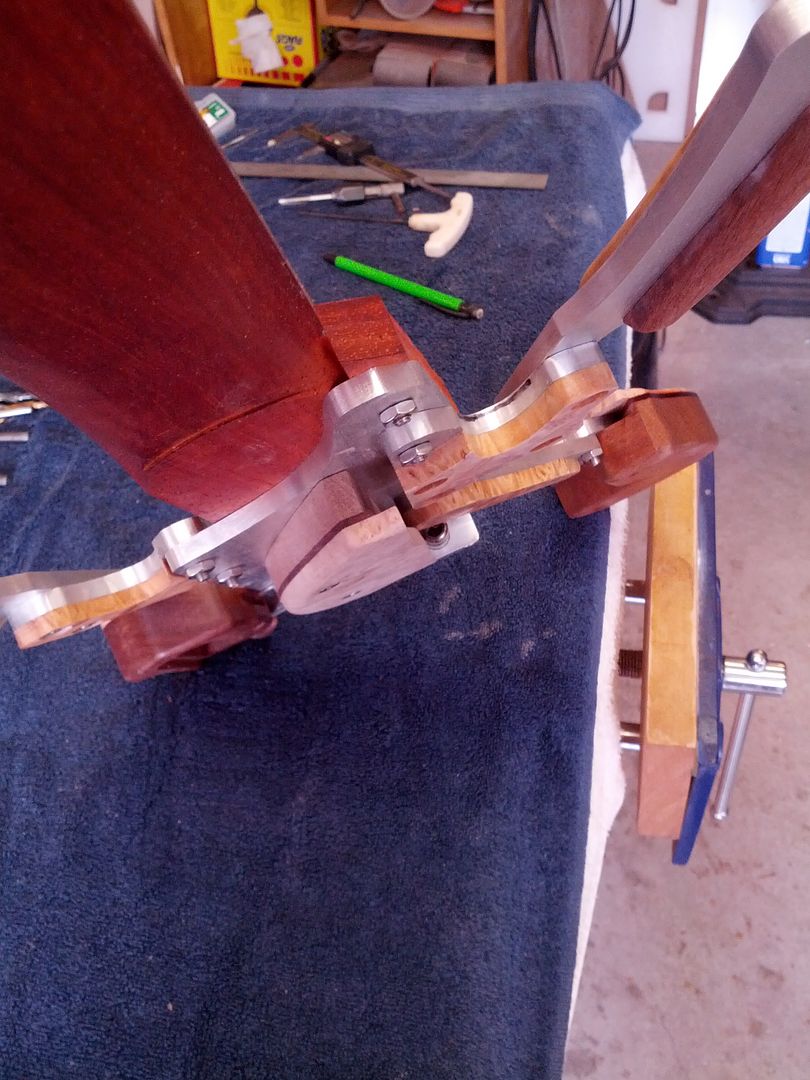
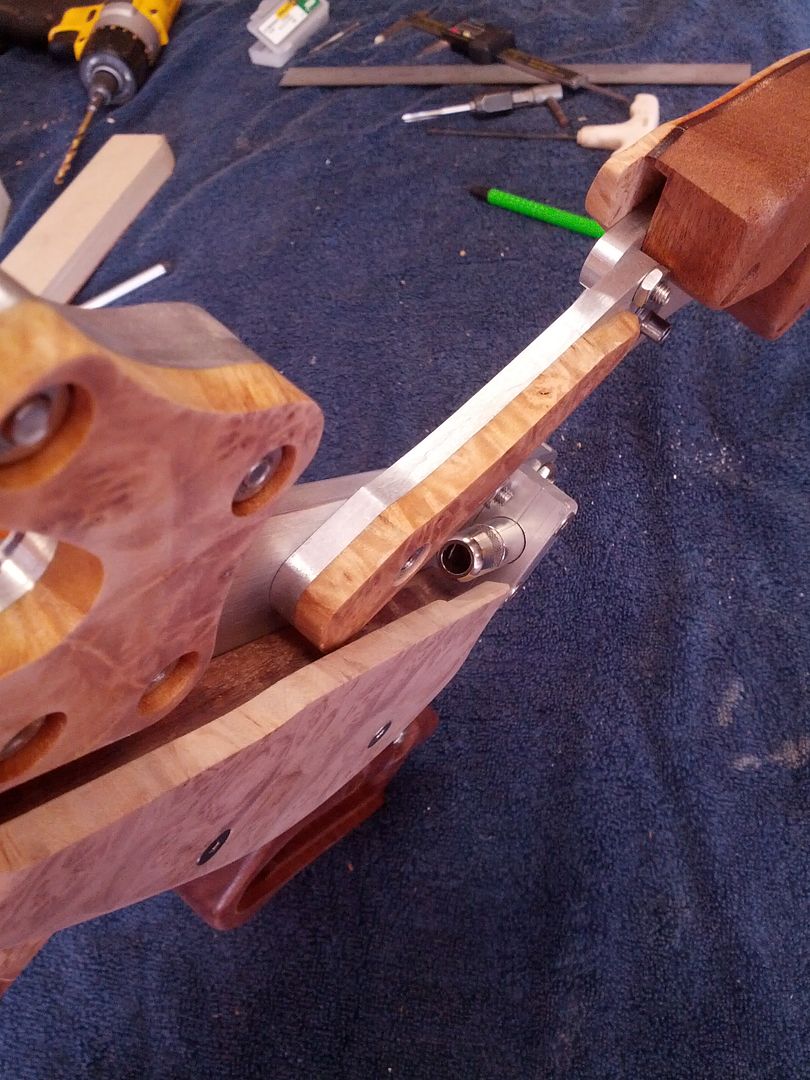
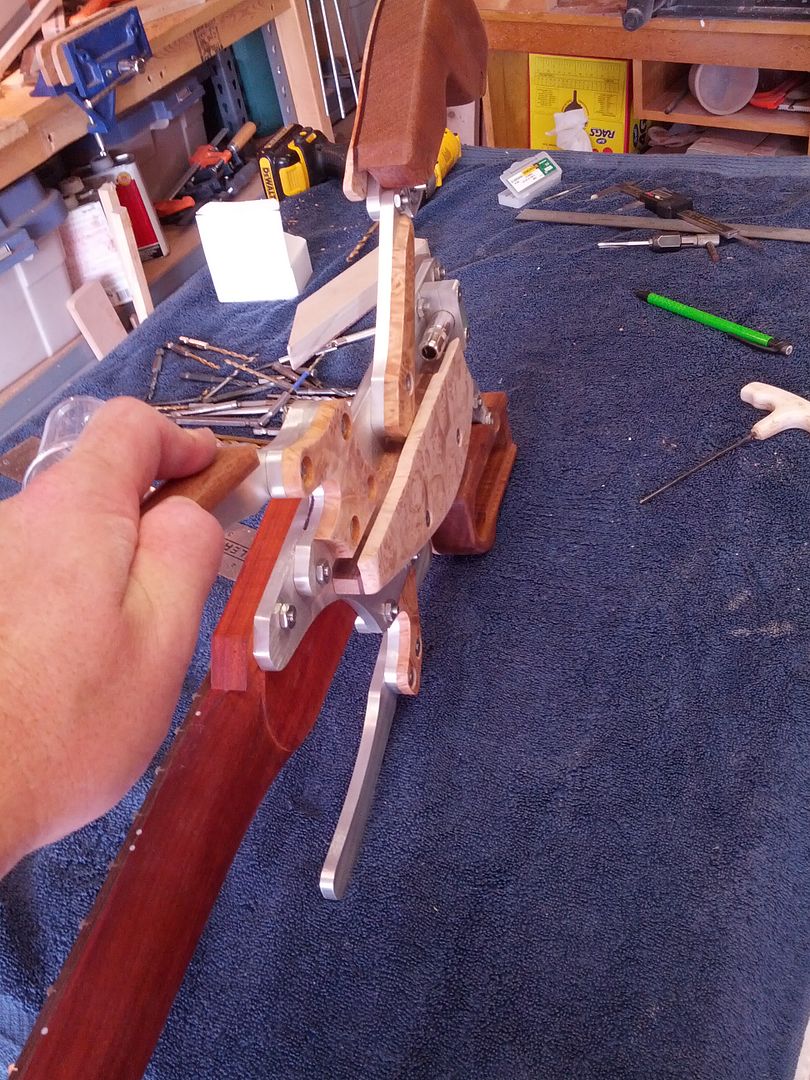
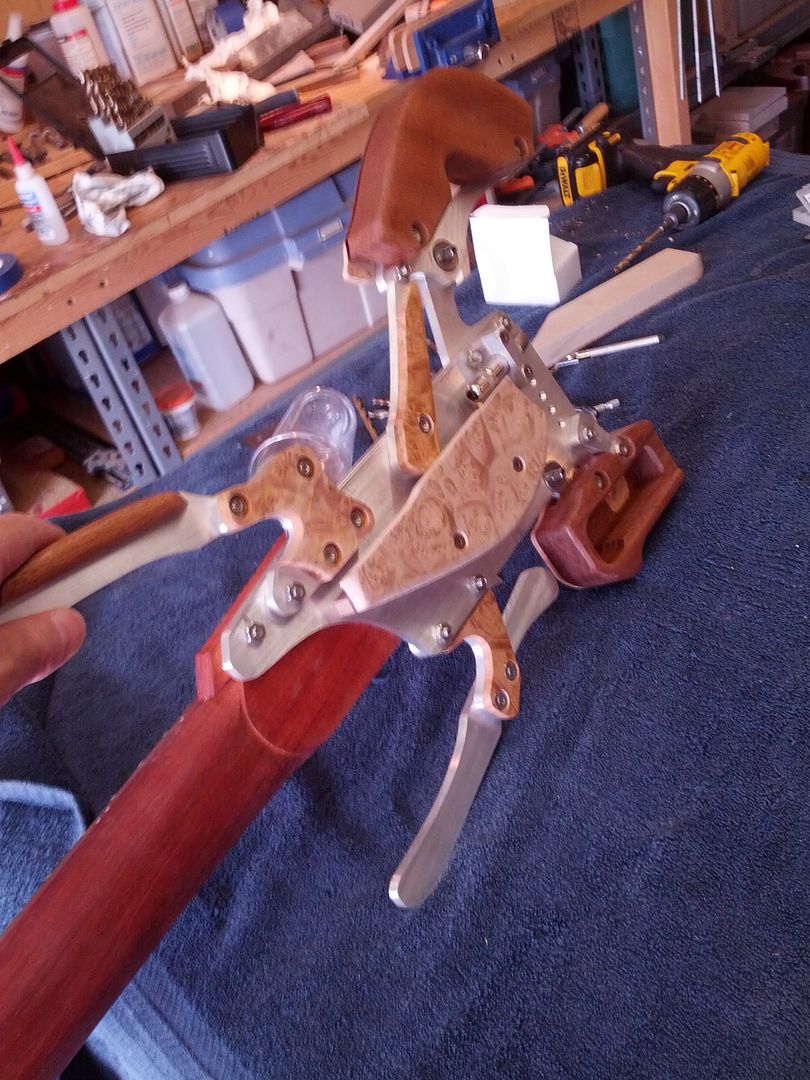
Clean up the neck and get it ready for oil
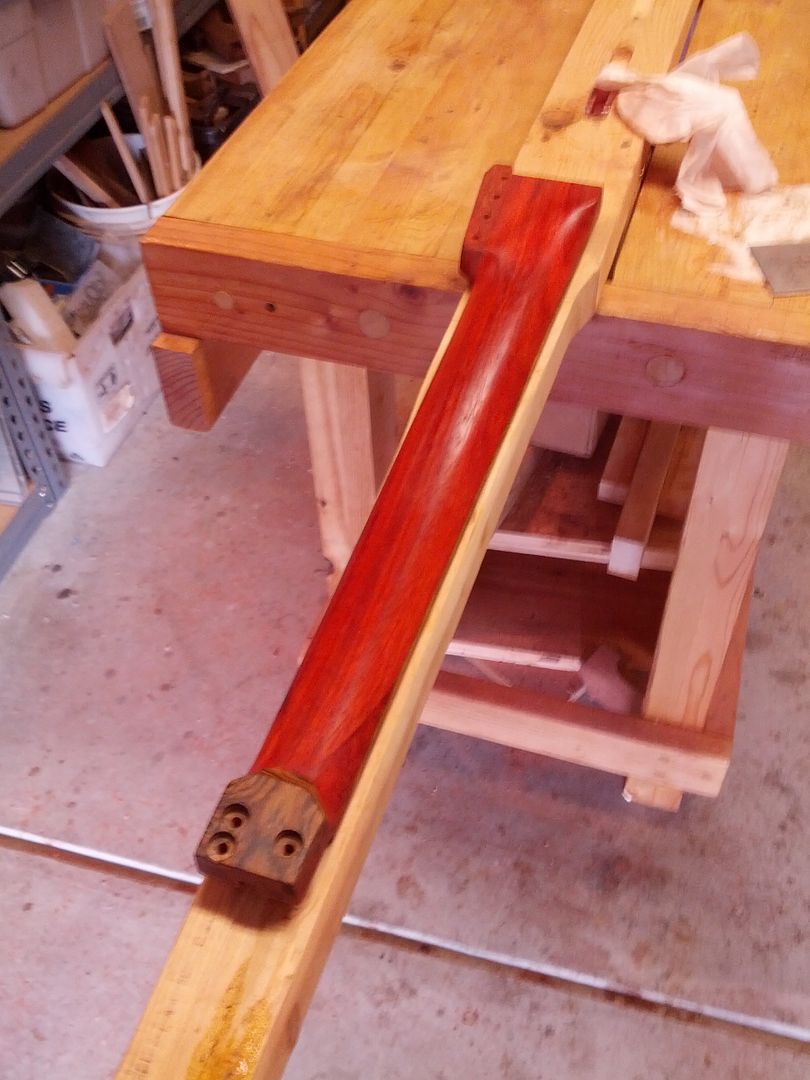
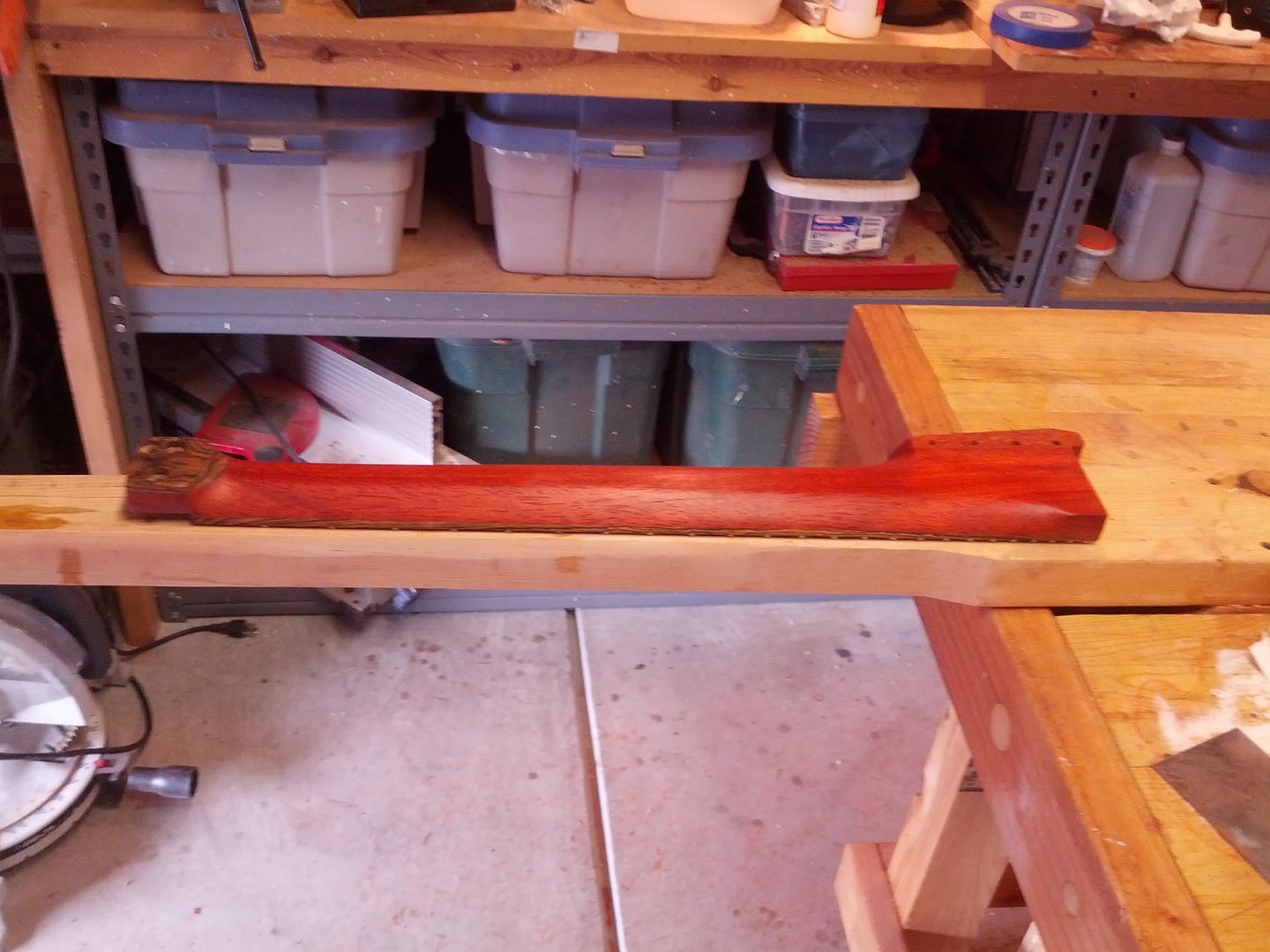
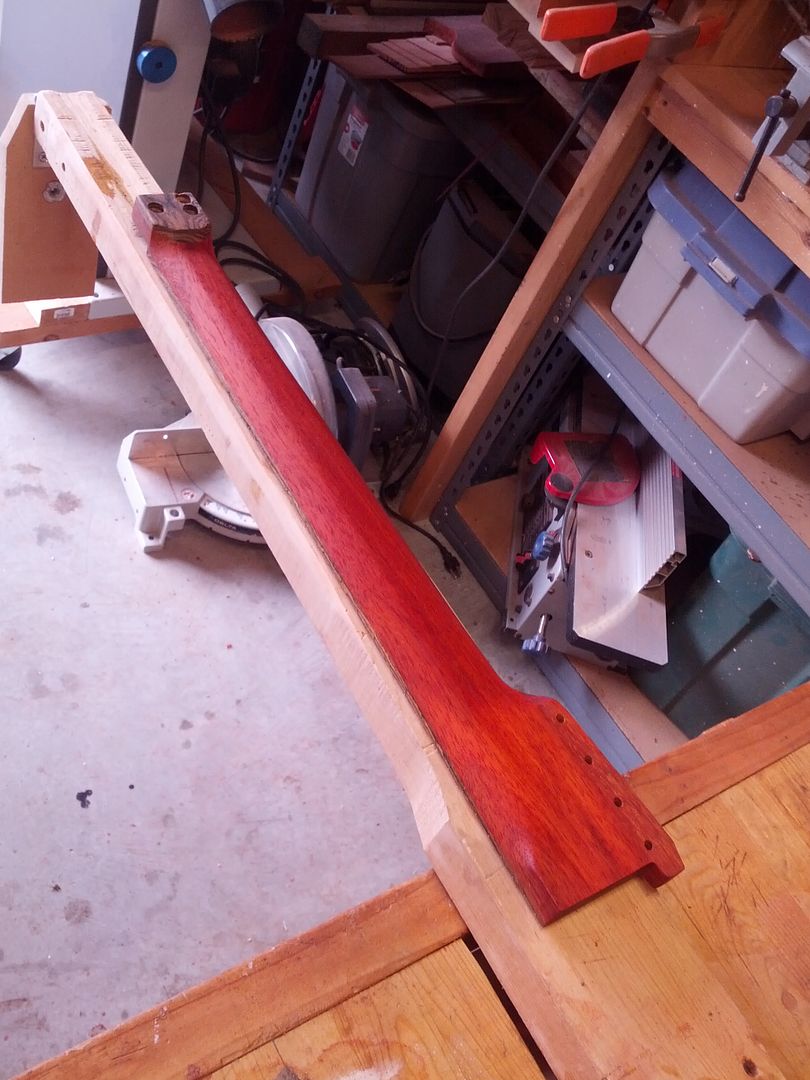
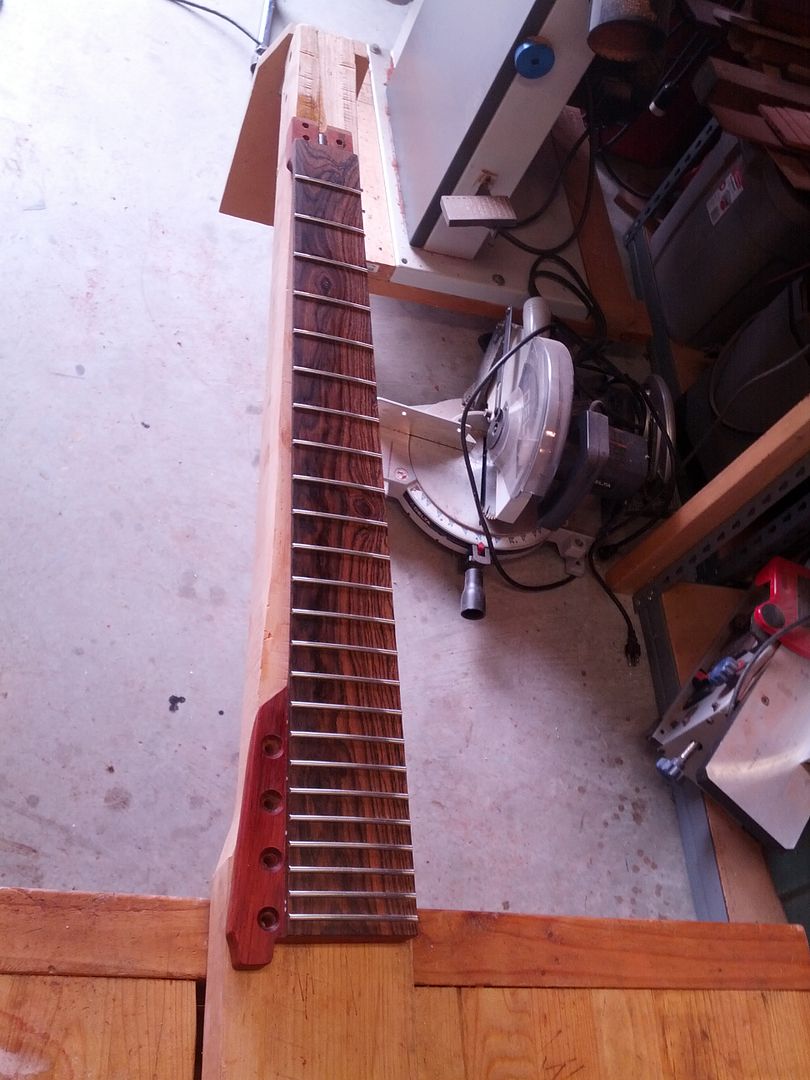
Decent upper fret access
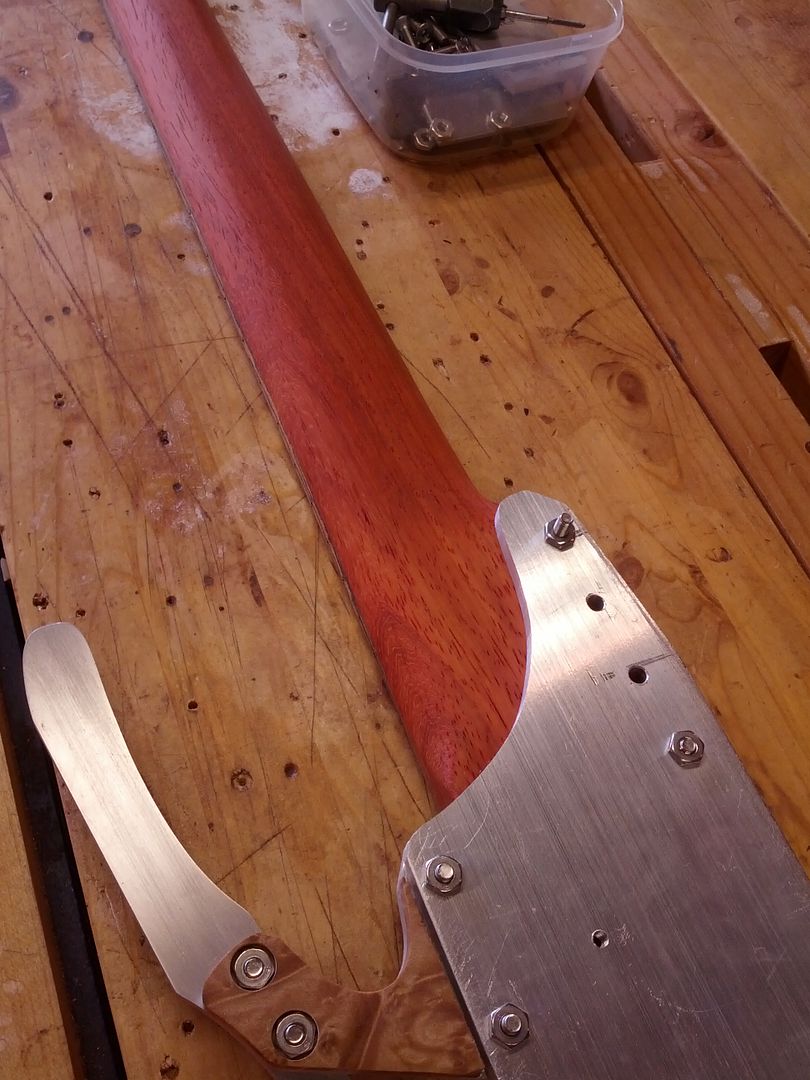
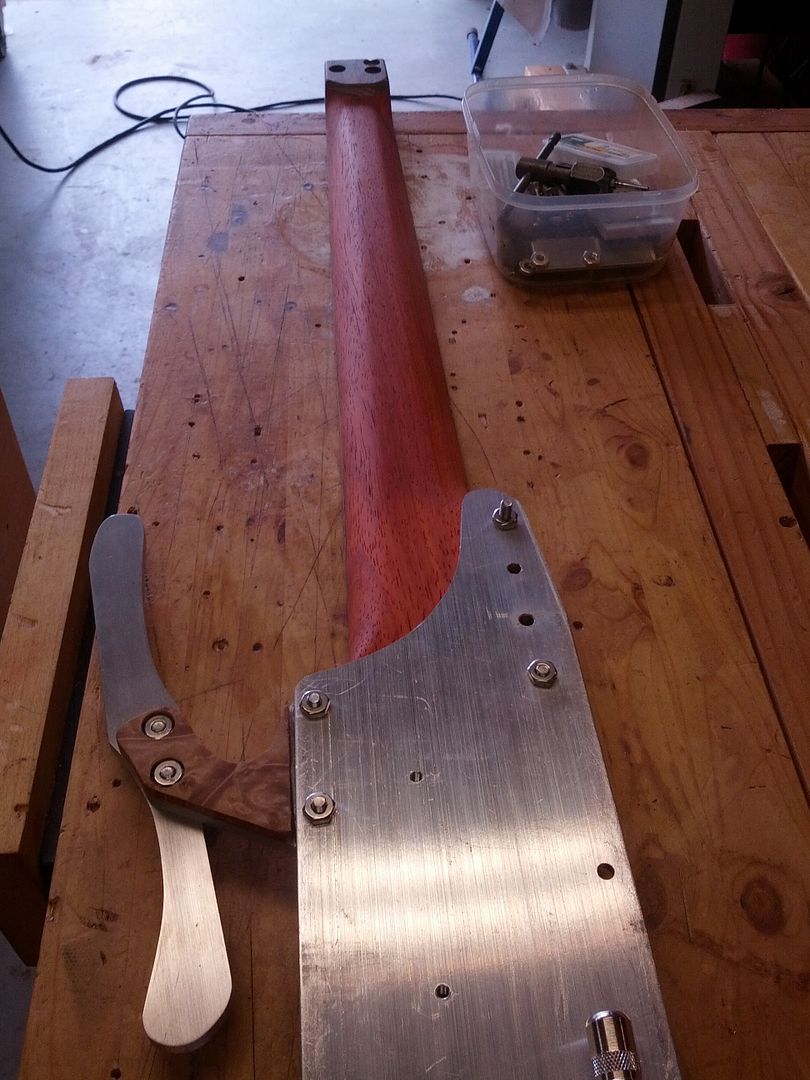
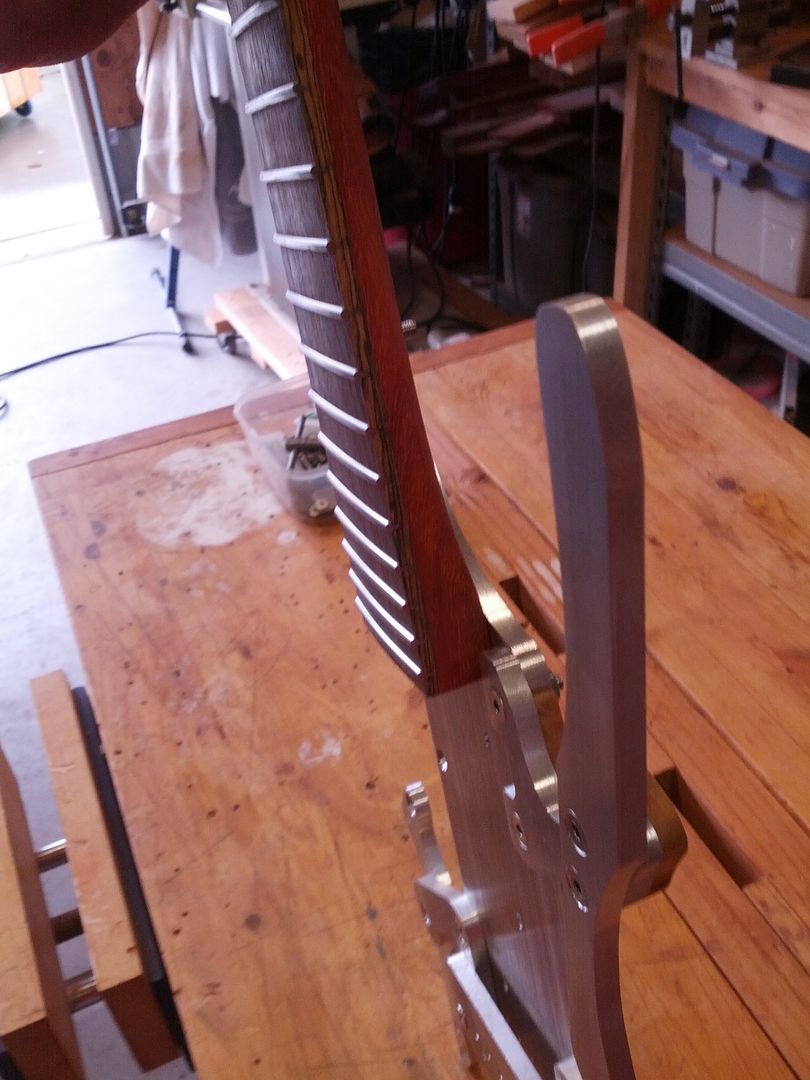
Getting everything lined up. Regular pickups are not going to fit. Concious decision to keep the guitar thin. The 65 year old design is not the only way to build a pickup.

Much thinner designed pickup fits fine. I have several designs that are very thin enough for this design.
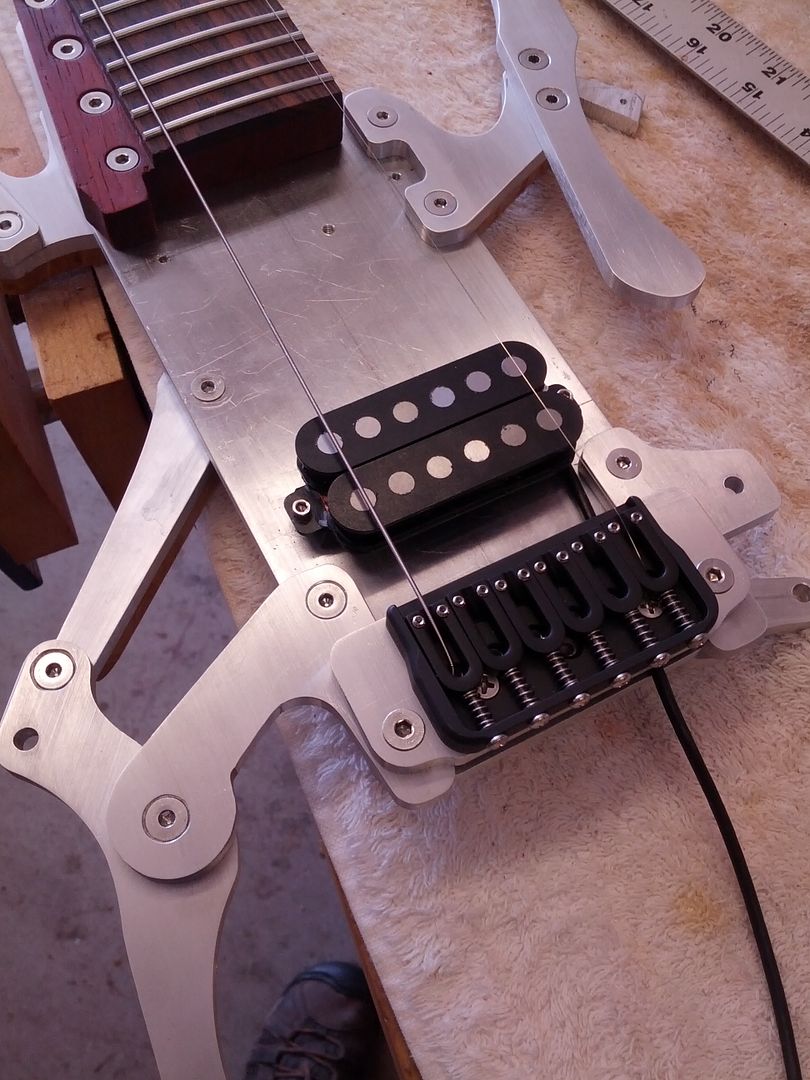
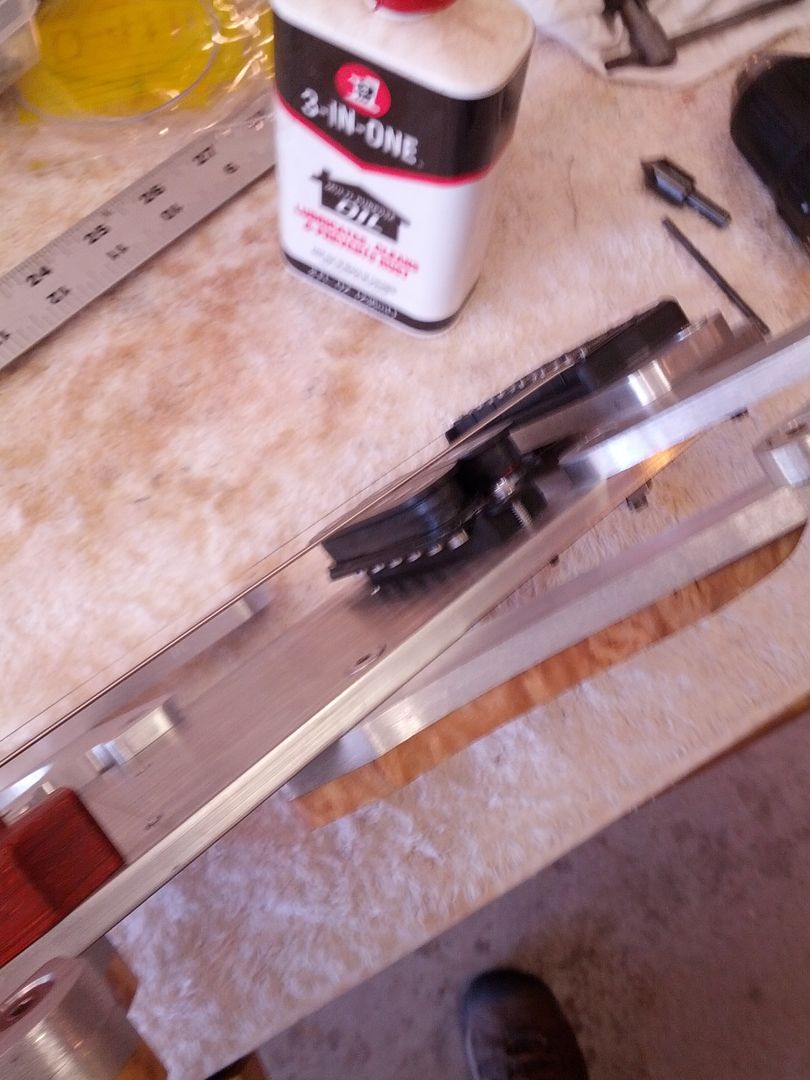
Mounting screws are tapped in to the plate. Long screws are not going to work well. The plate is .25" though so plenty of adjustment room without sticking out the back.
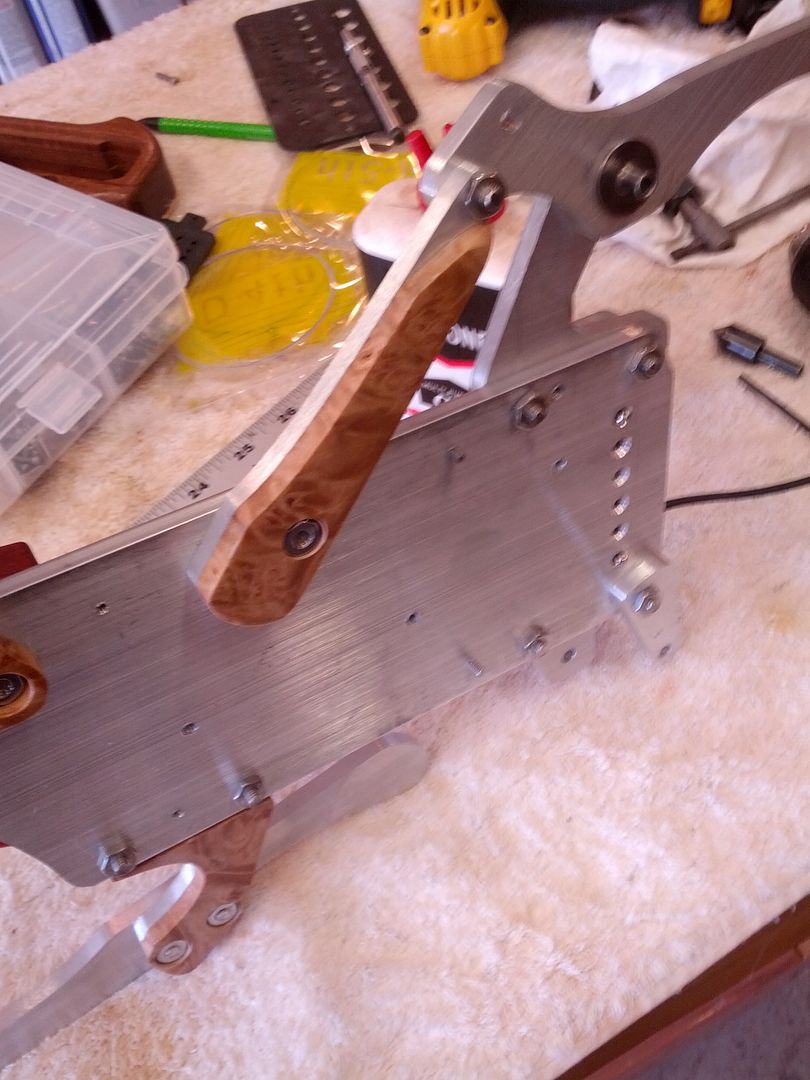
Shorter screws
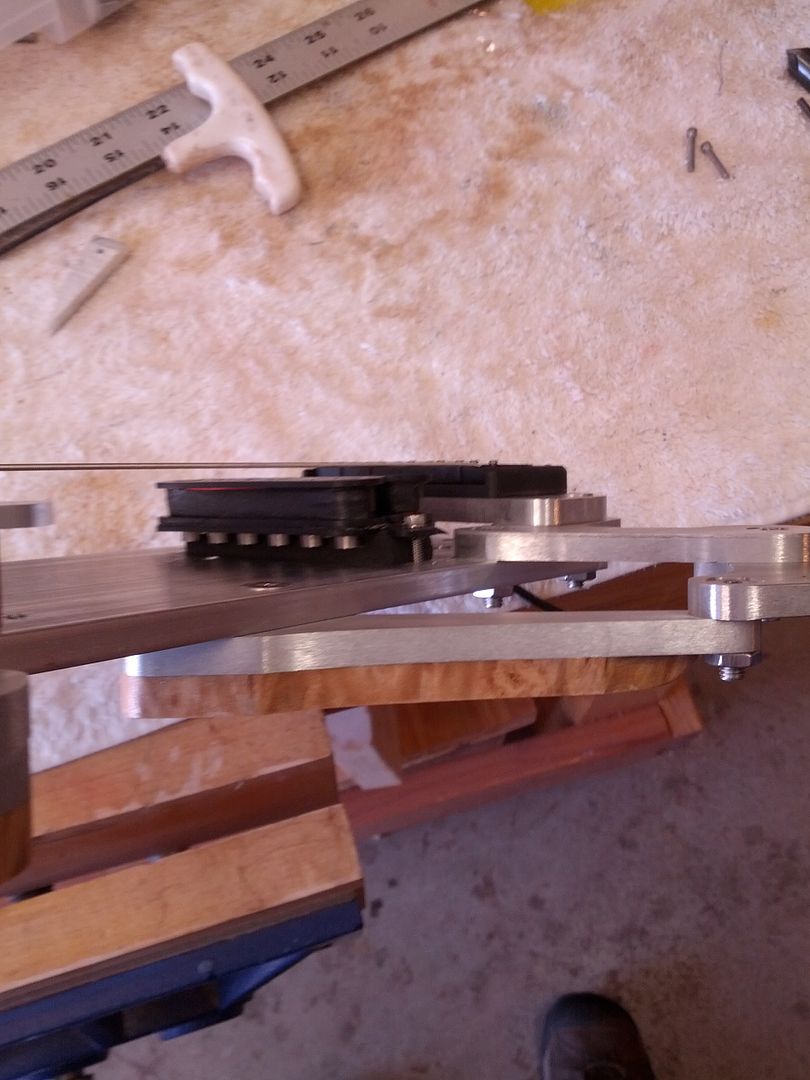
Tuners installed
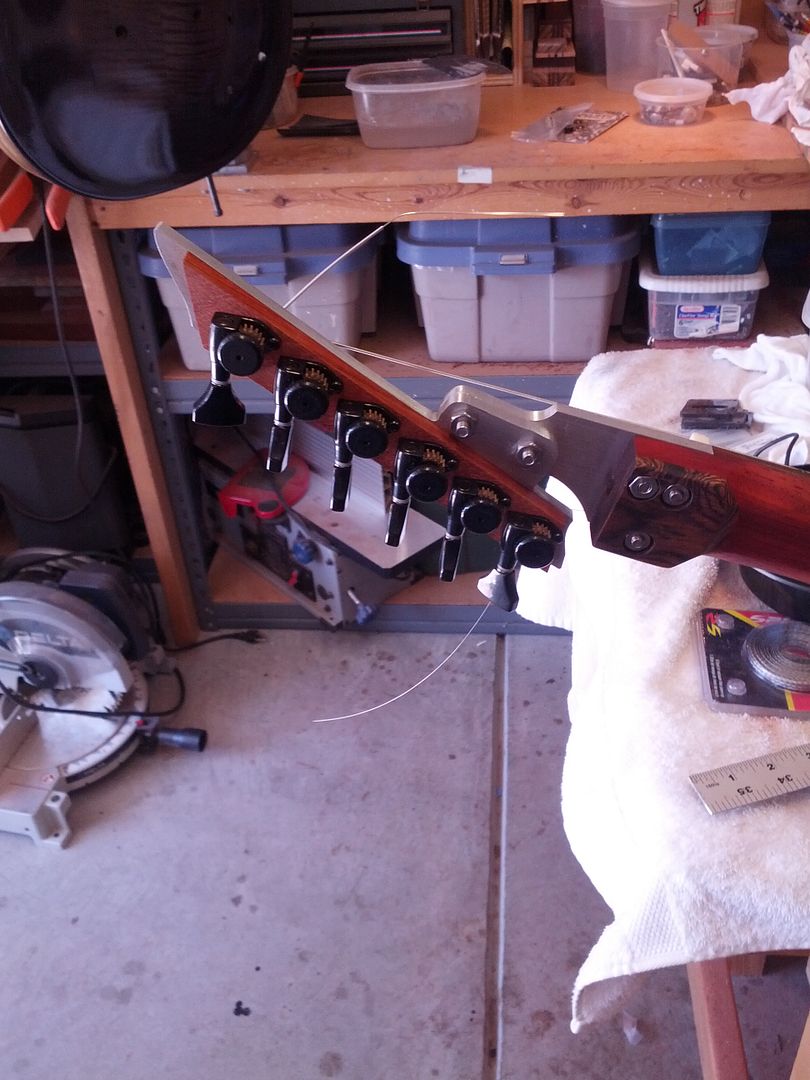
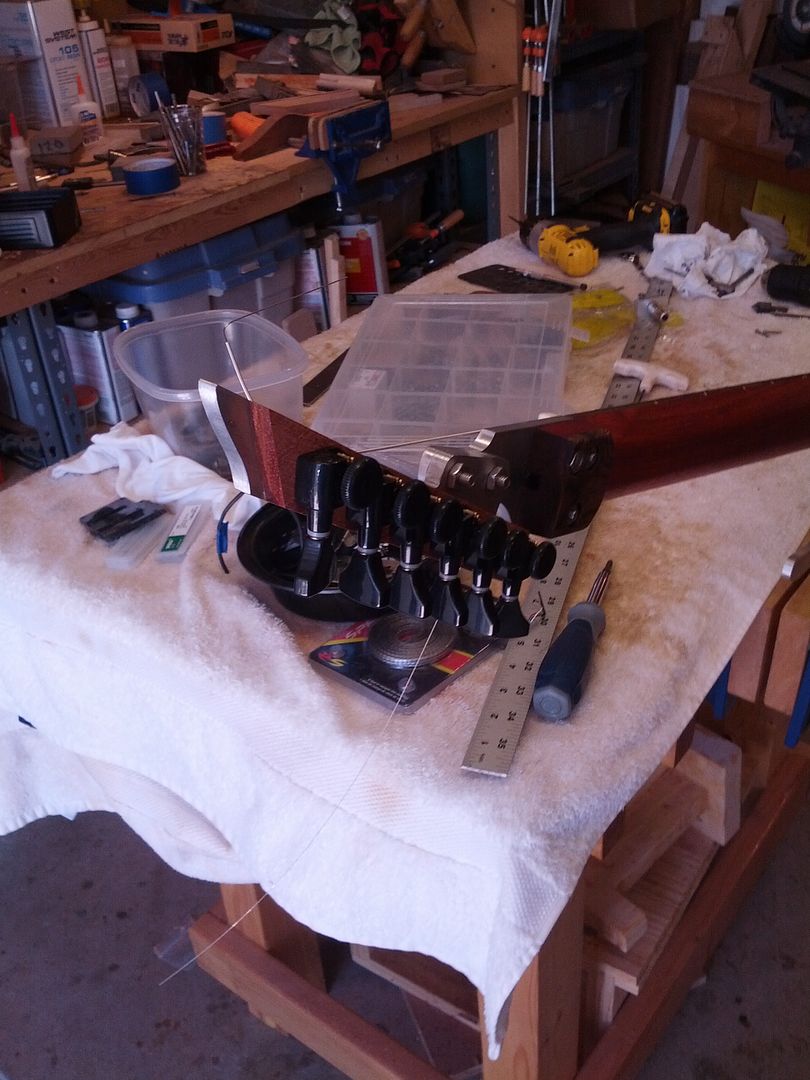
Closer. I did not get the string pull perfectly straight and there is a bit of fan in the strings after the nut. Good thing is it is realatively easy to make a new head piece. Heck of a lot easier than on an S9 set neck.
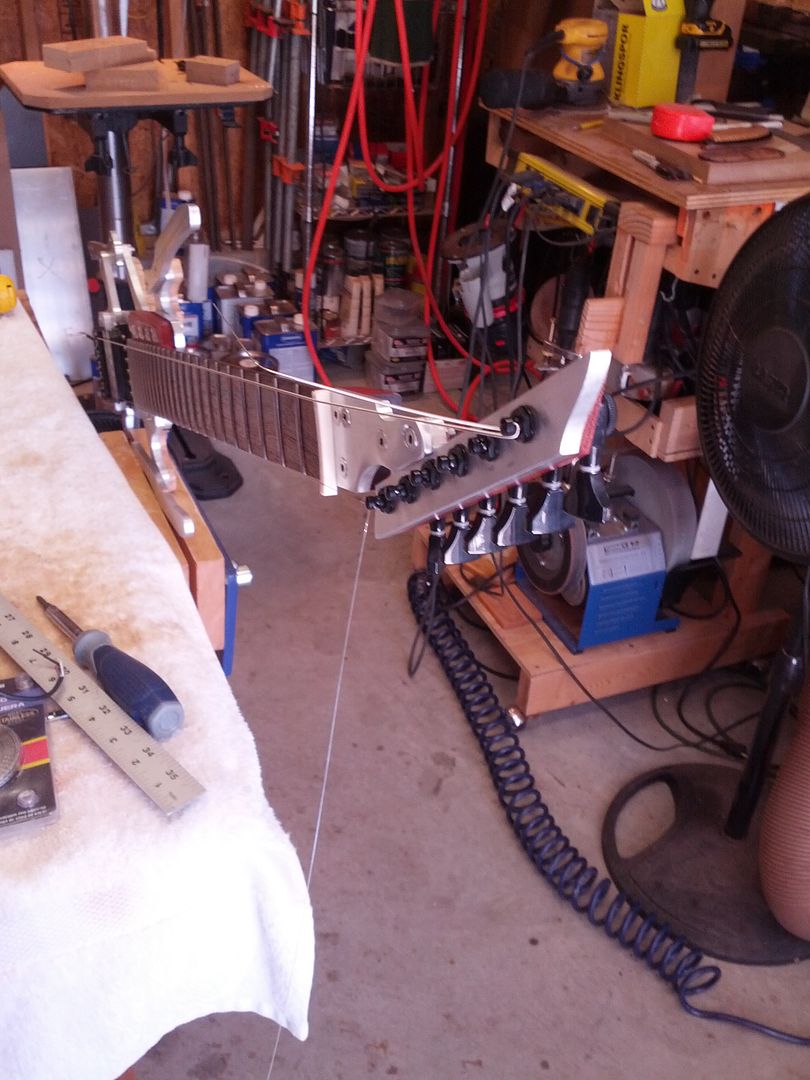
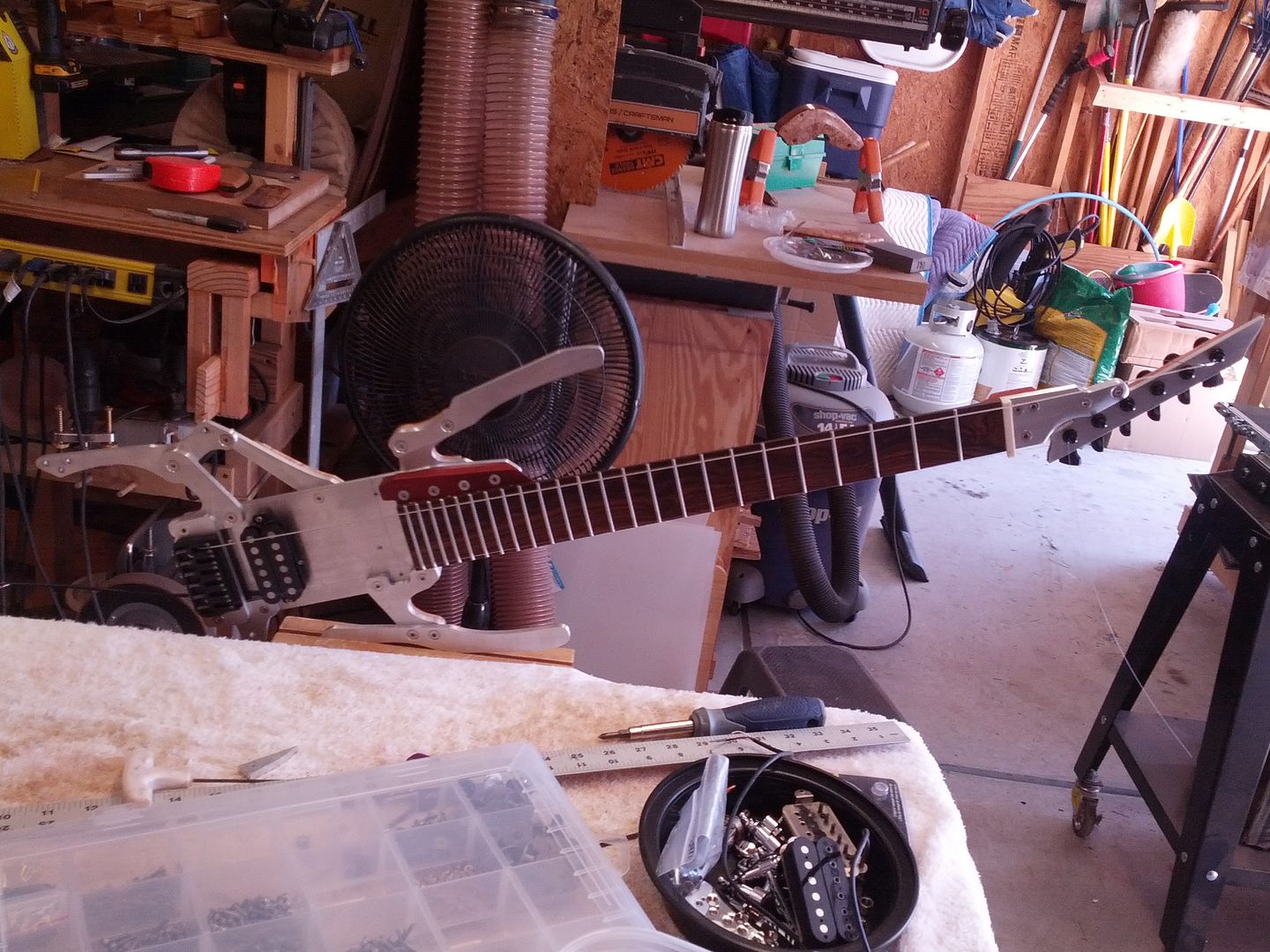
Quick Hits...
Archetype Part V
Covering some bits with left over wood.
This looks dangerous.

This looks cool

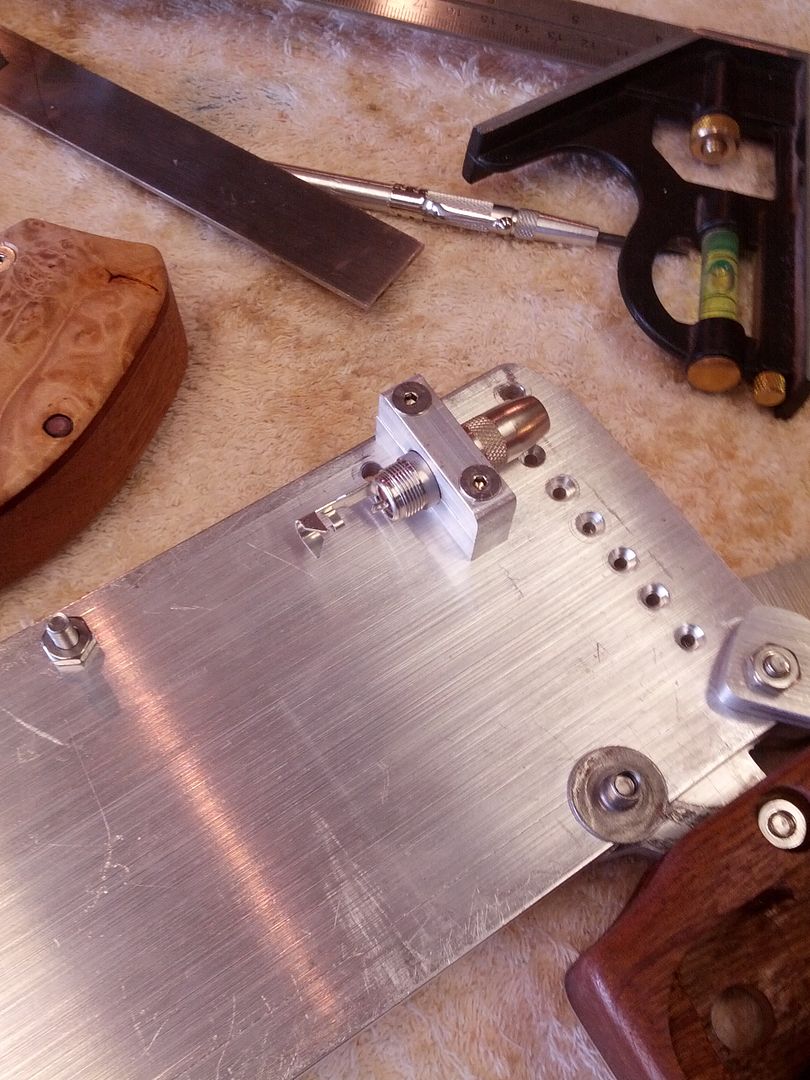
Got it now?

With the wood additions it is a bit more comfortable and I think the input jack is out of the way for now.
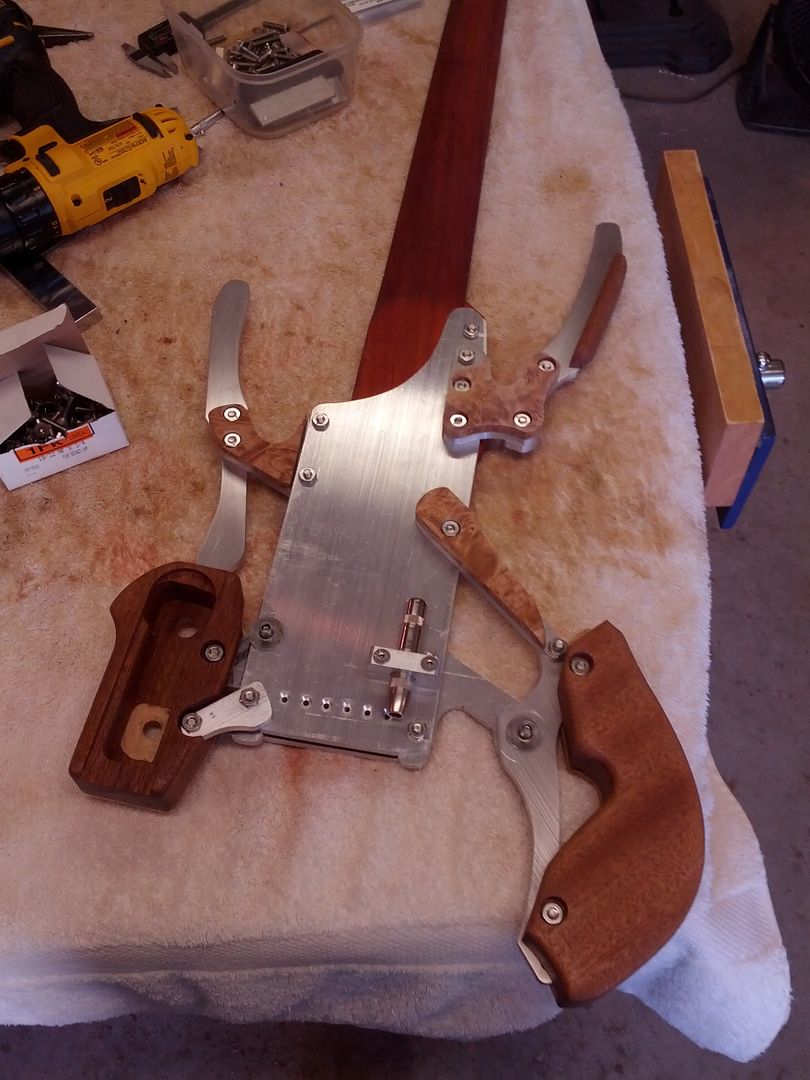

So with that solved I have to get something on the back to make it sit right against the body (belly).

Pickups for Carl.
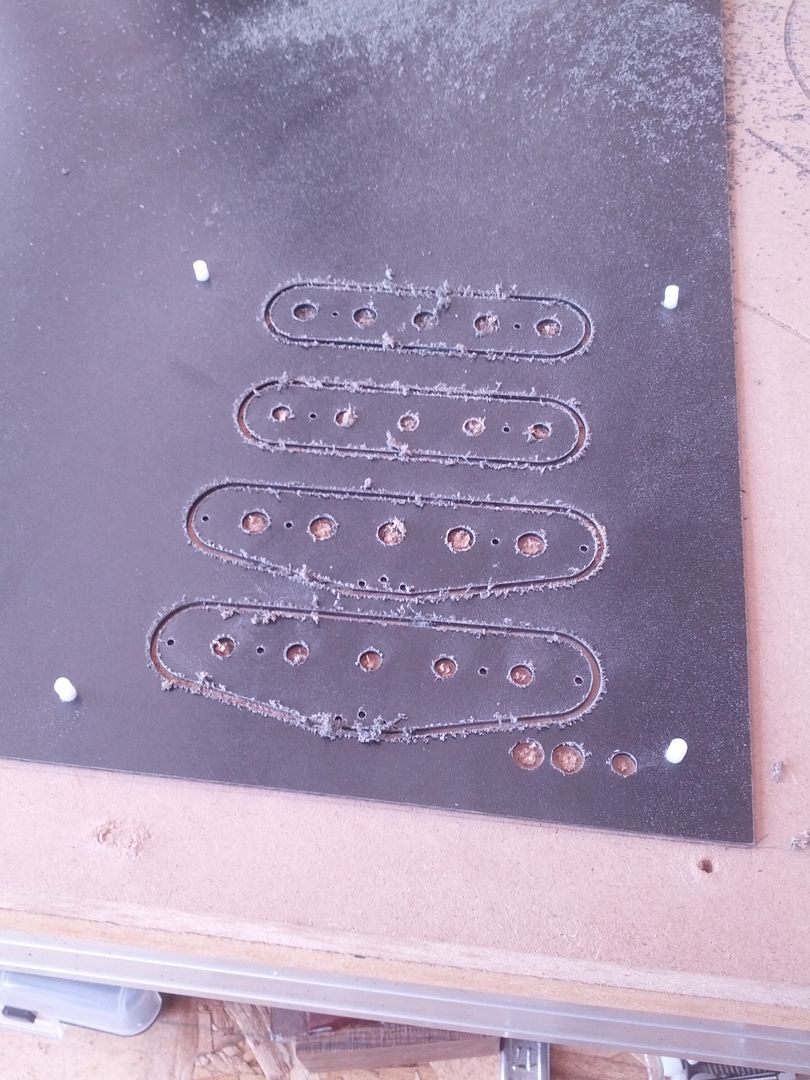
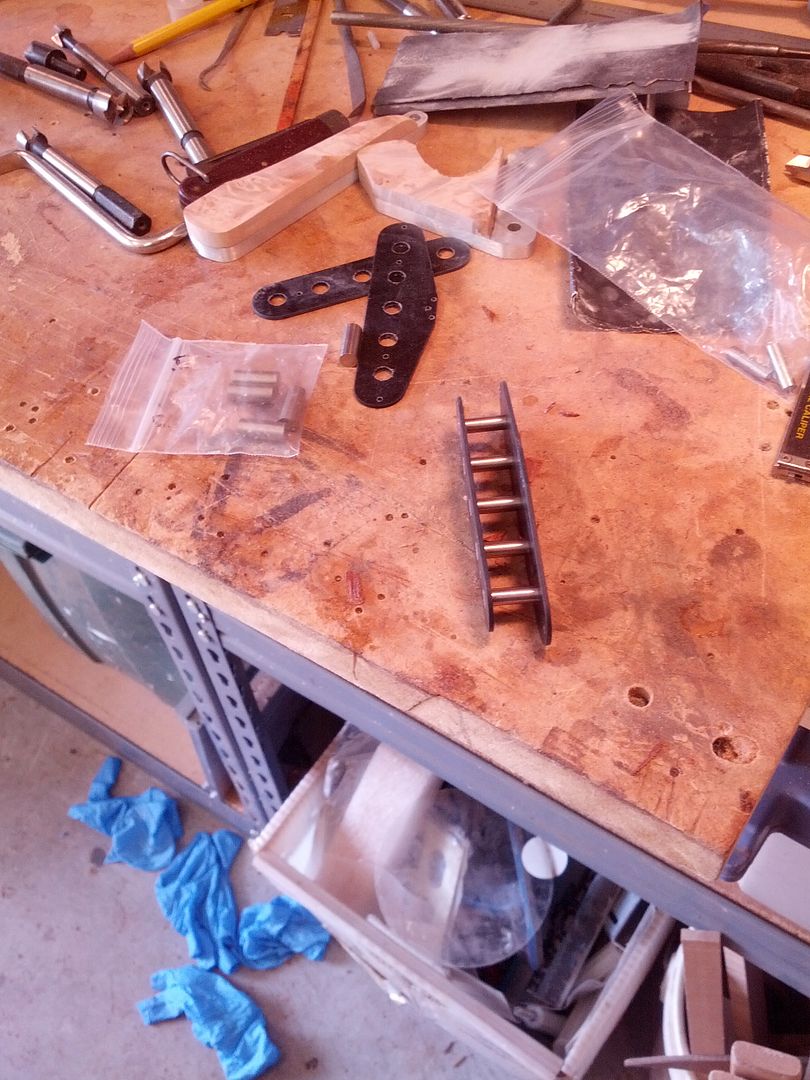
Covering some bits with left over wood.
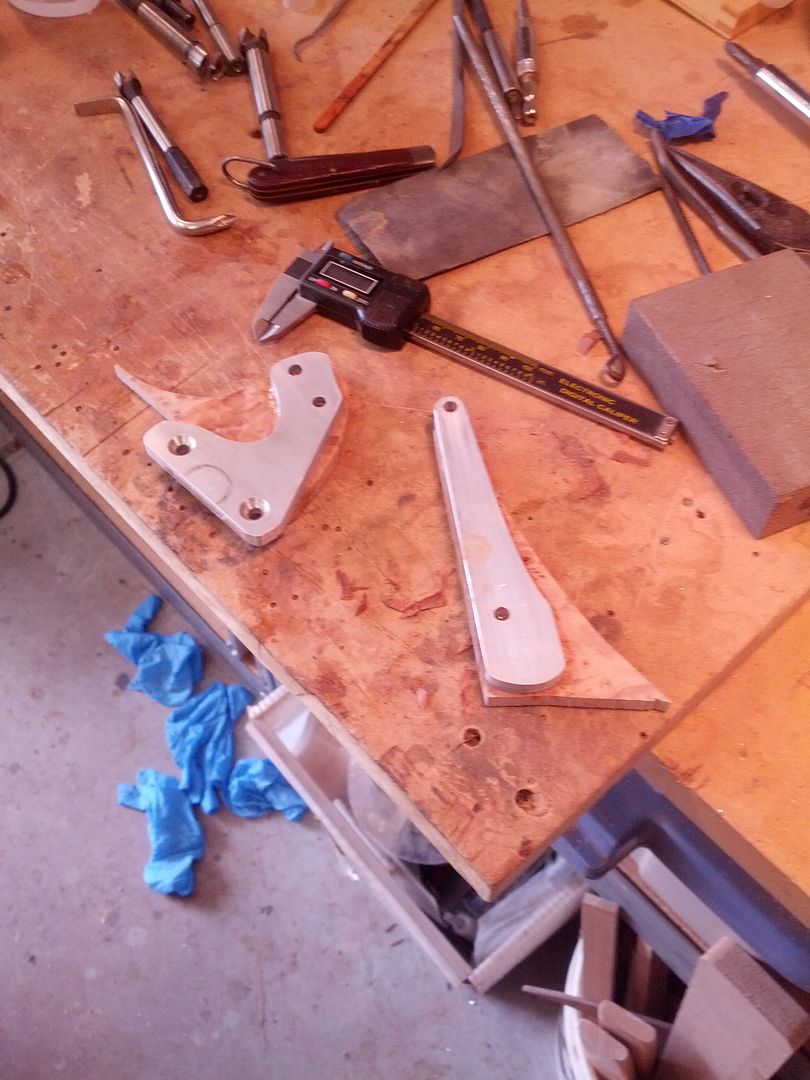
This looks dangerous.
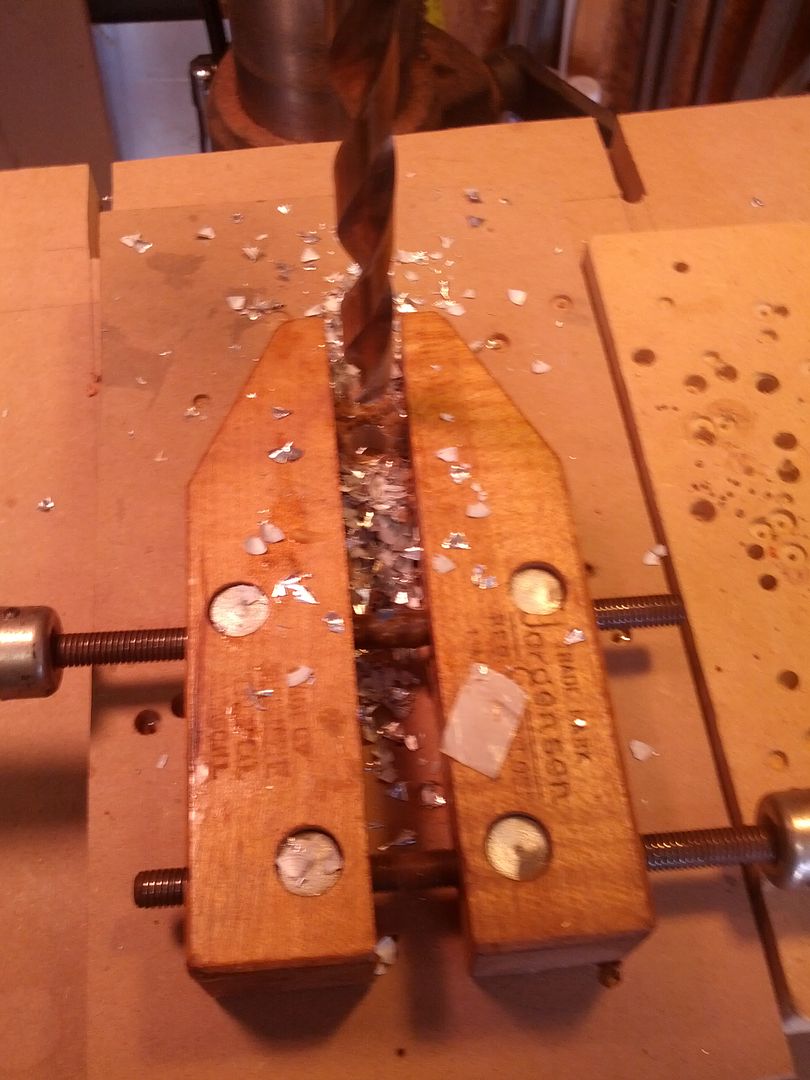

This looks cool



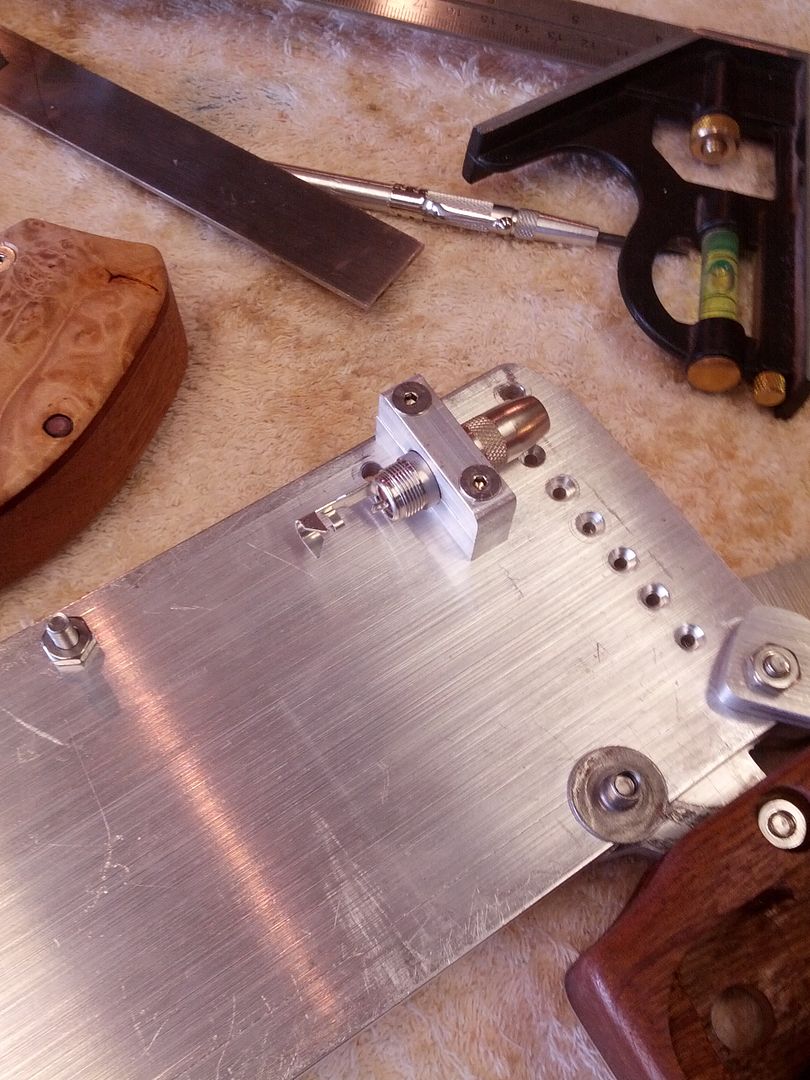
Got it now?


With the wood additions it is a bit more comfortable and I think the input jack is out of the way for now.
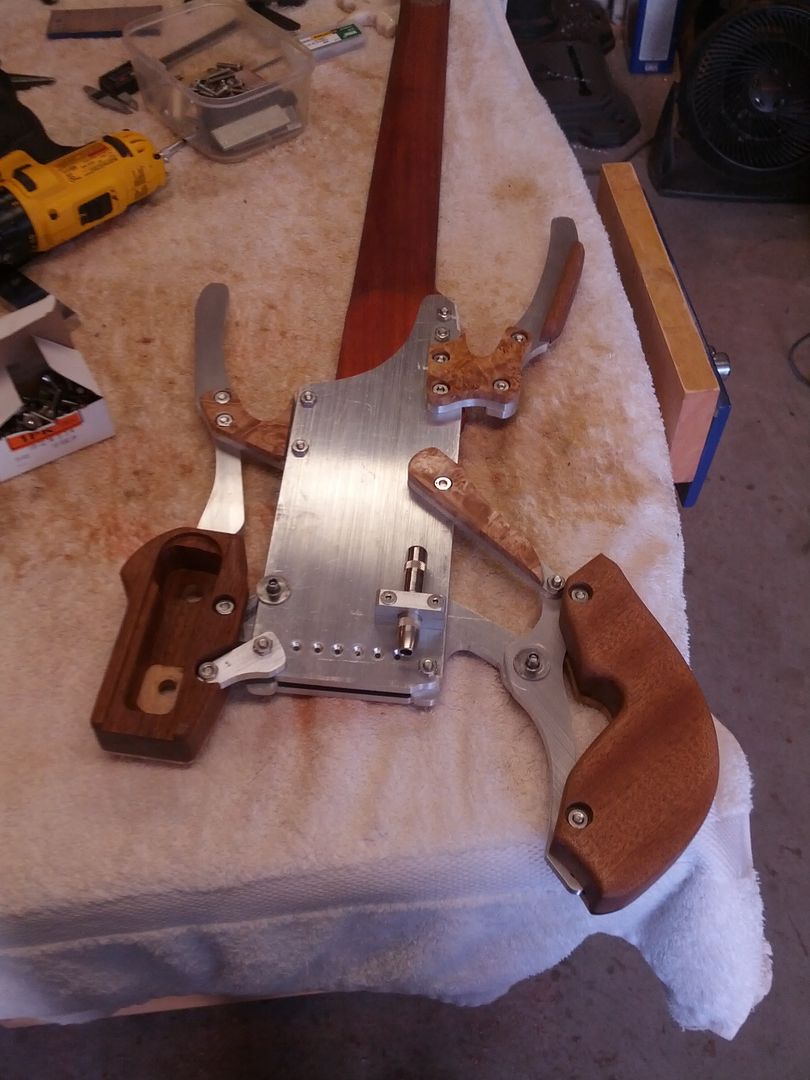
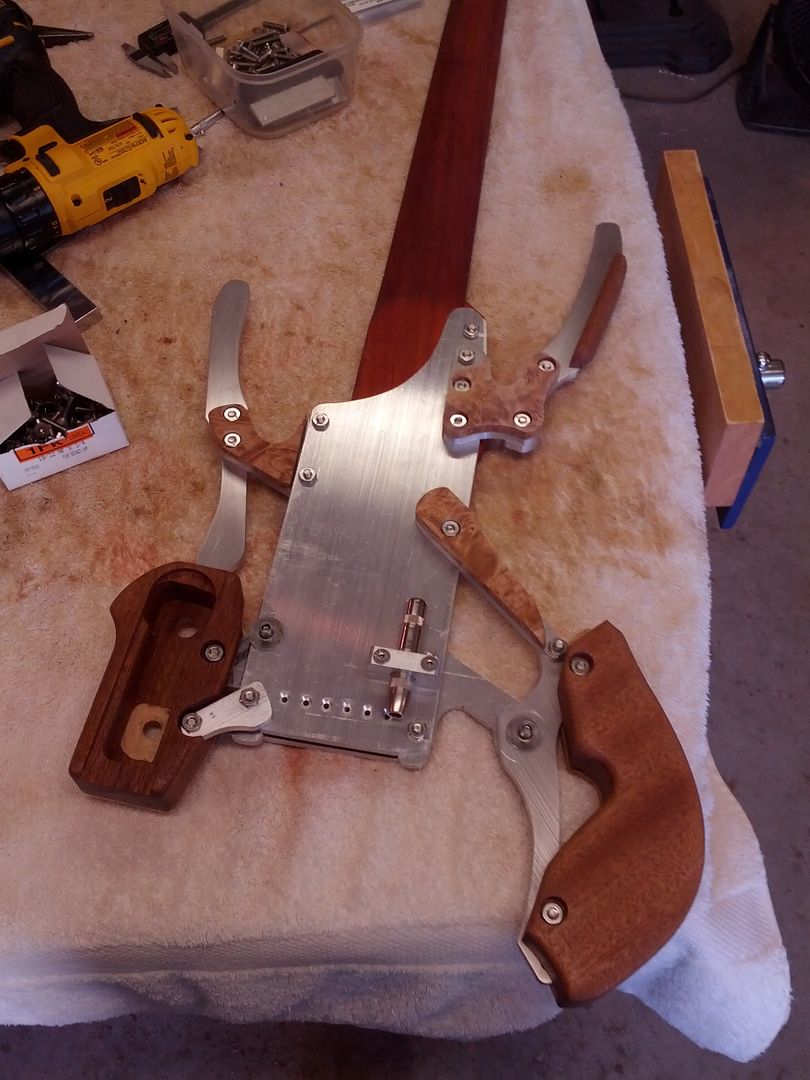


So with that solved I have to get something on the back to make it sit right against the body (belly).


Pickups for Carl.
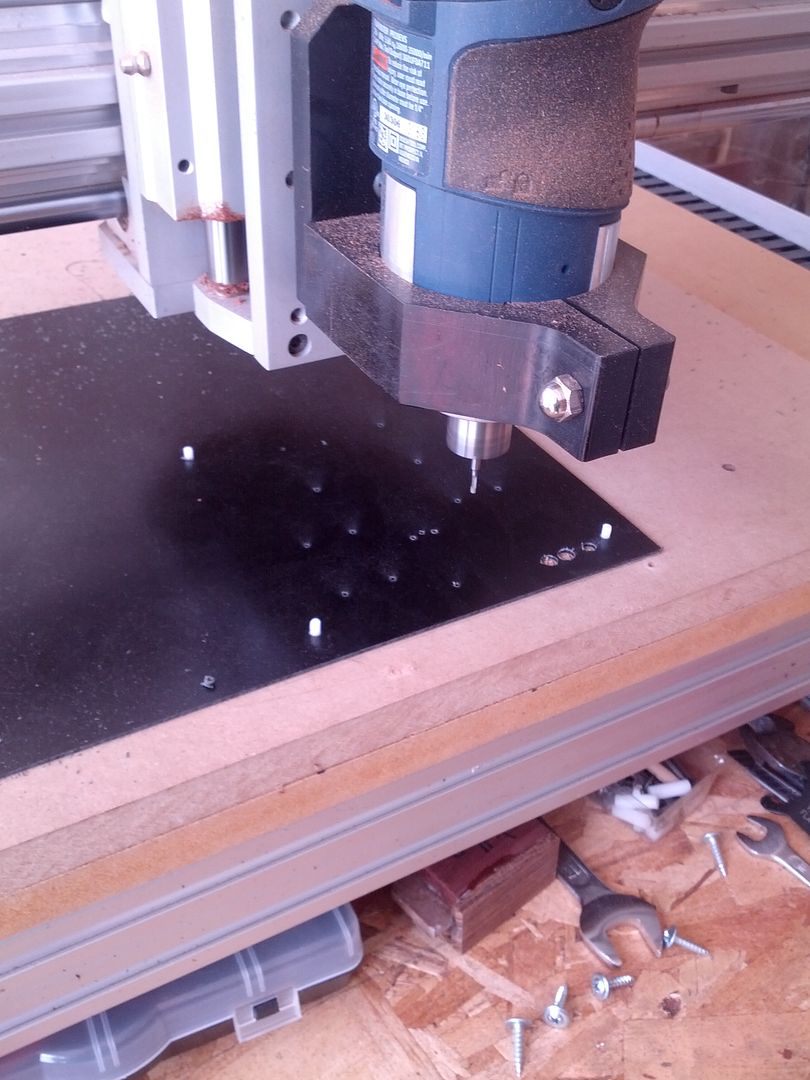
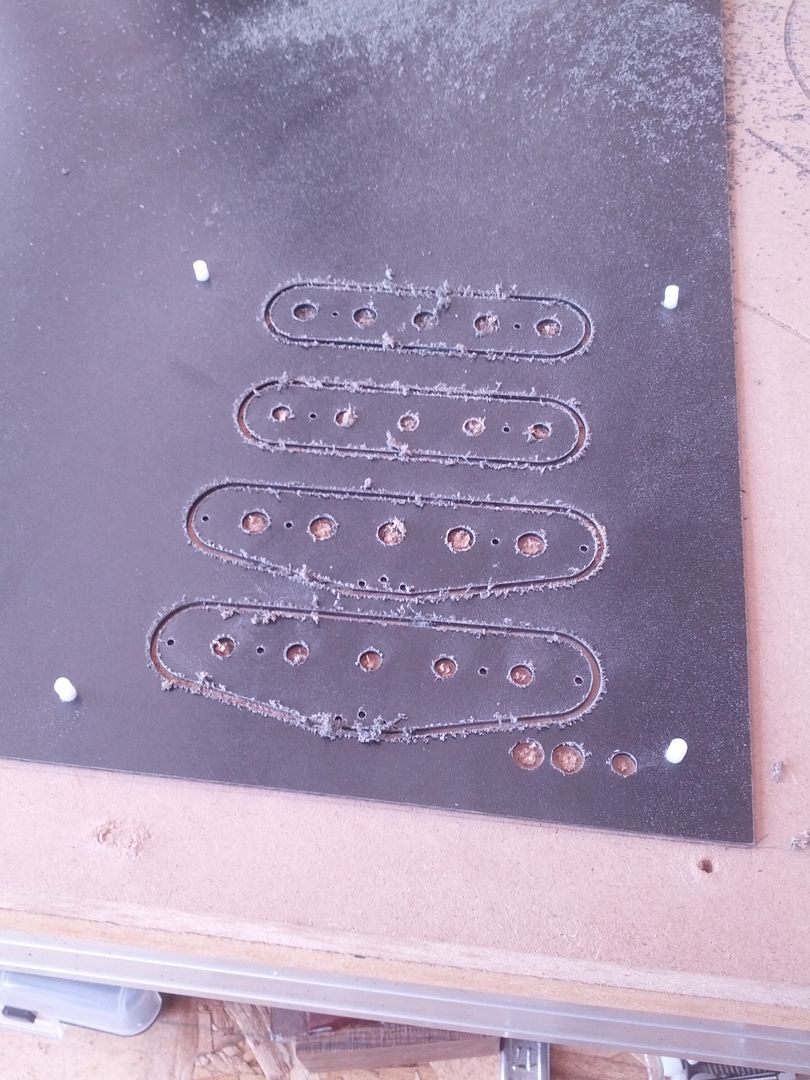
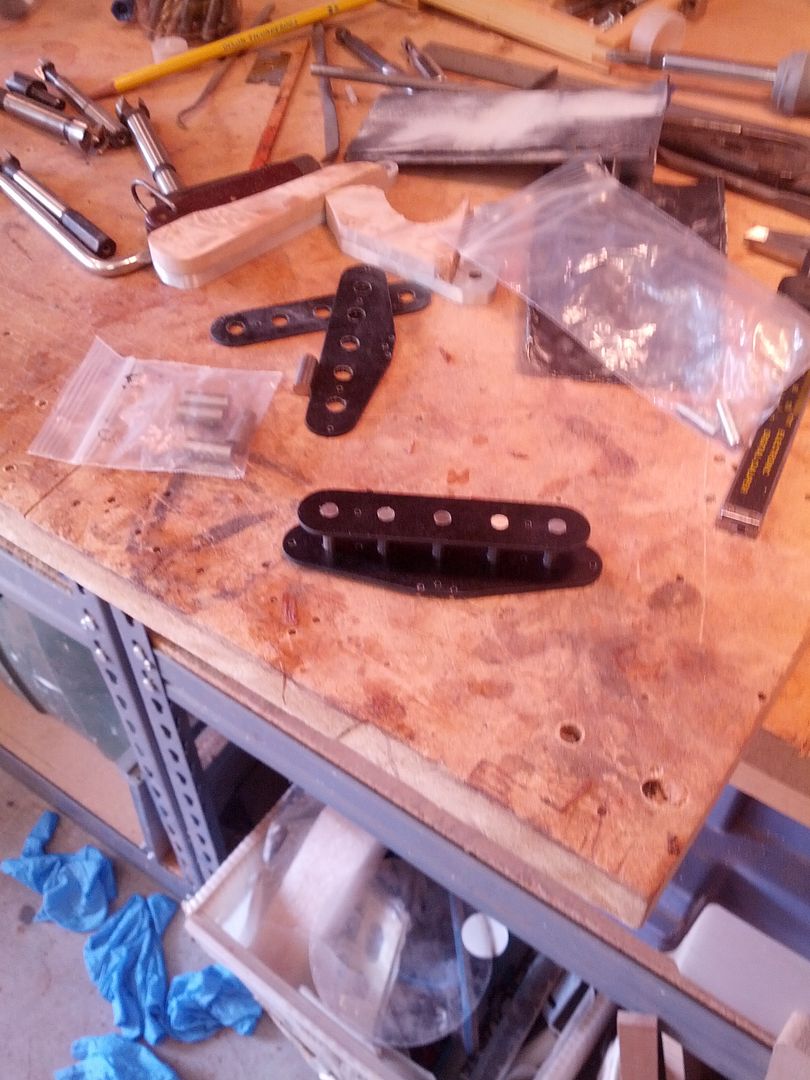
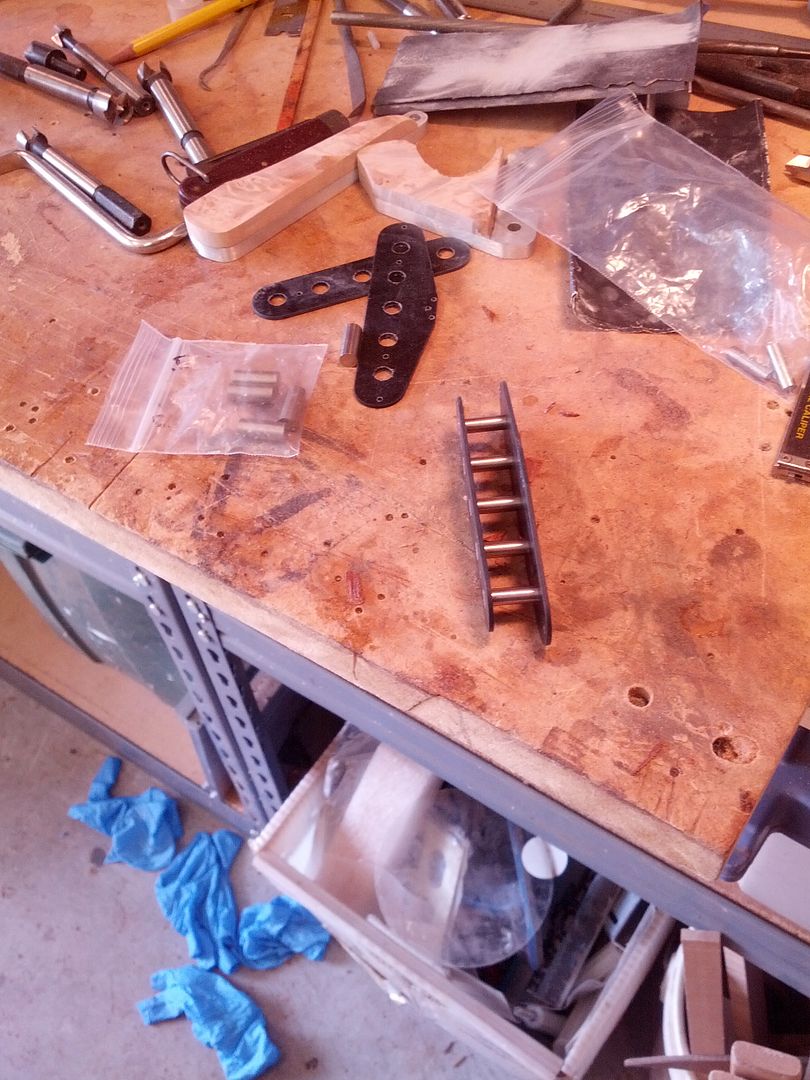
Subscribe to:
Posts (Atom)