Starting on a new bass pickup. While I would love to build this with large pole magnets but they are hard to find and expensive. So the design here will use more conventional parts... actually like hardware store parts. What do you need to build a pickup? Flatwork, Low Carbon Steel, and Magnets. For the pole pieces I want them large so I grabbed a piece of 3/8" cold rolled steel at Lowes. The great thing about the Music Man pickup is the big poles. The bad thing is finding parts. Basically there are no aftermarket parts so we have to do everything from scratch.
I don't have a lathe so I used a hack saw to cut the rods to length. I could use the chop saw and get them perfect but the heat generated in the rod causes the steel to change its character.
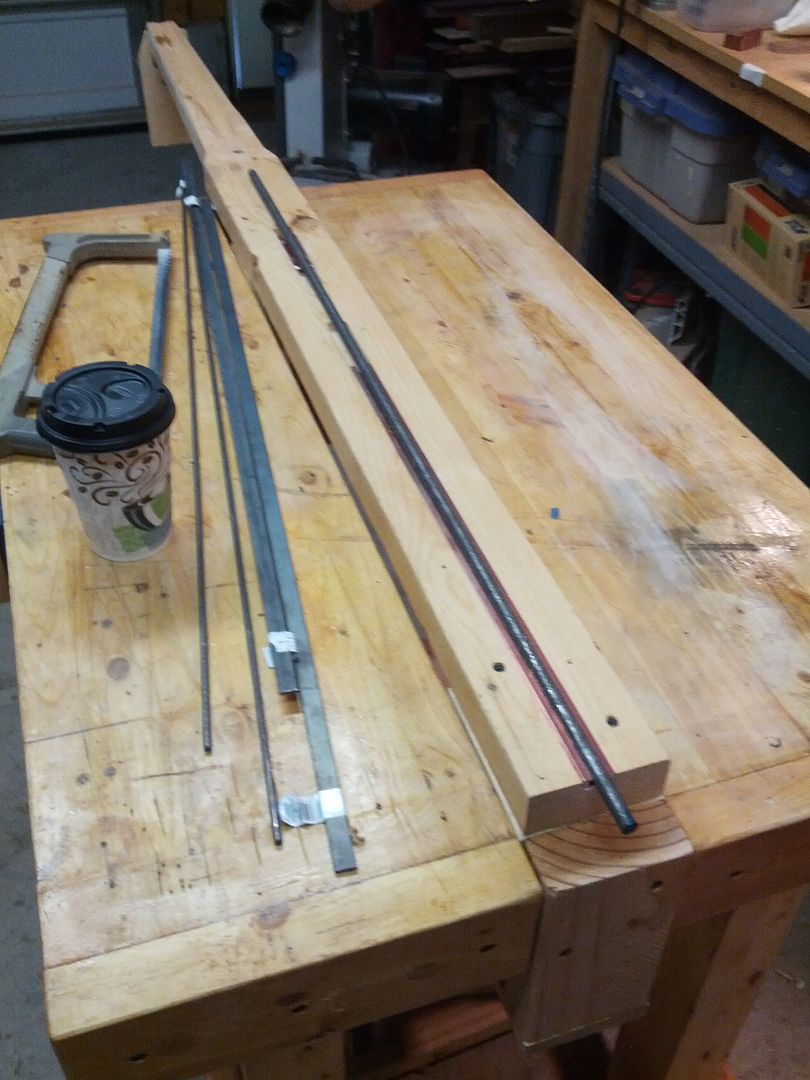

Cutting the rods with the hacksaw leaves a messy end. If you look at steel pole slugs in a humbucker they have a nice circular pattern on them from the lather cutting process. I am going to mock that out. Squared the rods on the disk sander and adjusted the lengths to suit what I am trying to do.
Next I chuck the rod in the drill press.

Then I take a mill file and put a slight bevel on the edge and clean up the face removing as many of the scratches form the sander as I can.

Now the trick. 80 grit PSA on a block of MDF. Turn the drill press on and run the rod down onto the block. This creates the swirls I need. Careful not to push too hard as you can really hurt yourself if the block flies out from under the rod.


I used a wet stone to square the end of the rod before putting the swirls in. This worked better than going straight to the sanding block. The problem with cold rolled steel from Lowes is that it is not very precisely ground and the outside is messy so I have to clean it up with a sanding spong.


And the results.

After cutting the flatware time to put it together.

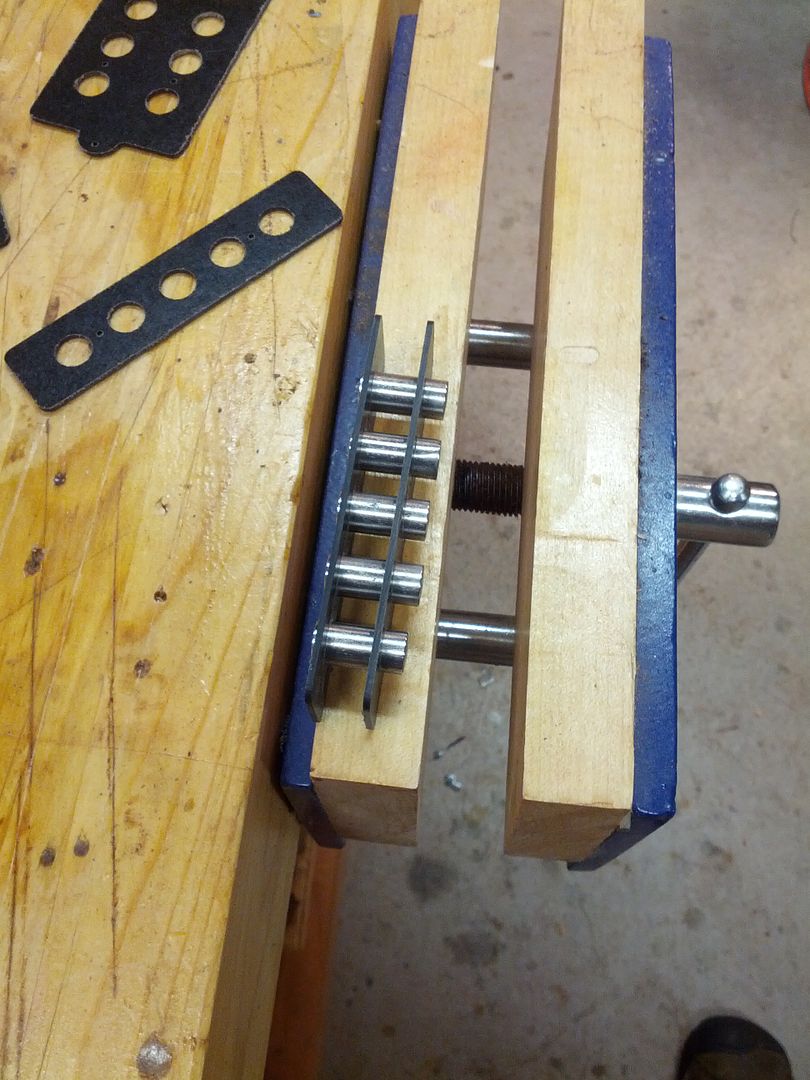
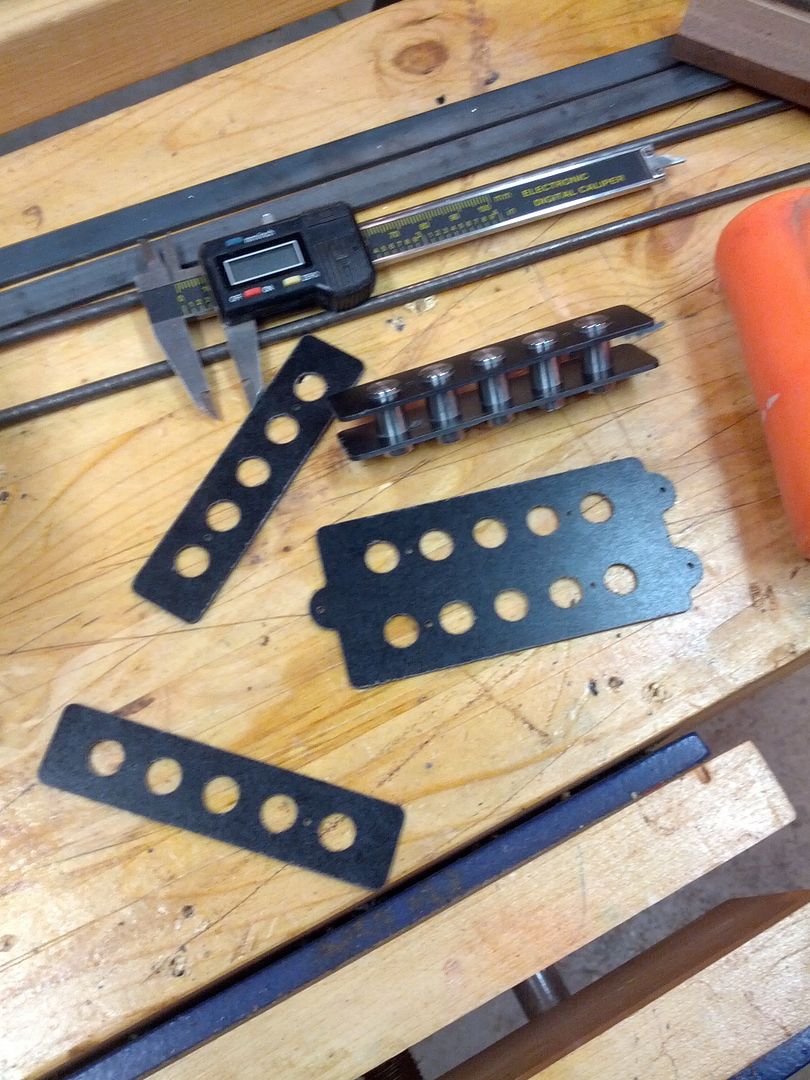







Blades cut from steel and bobbins assembled.
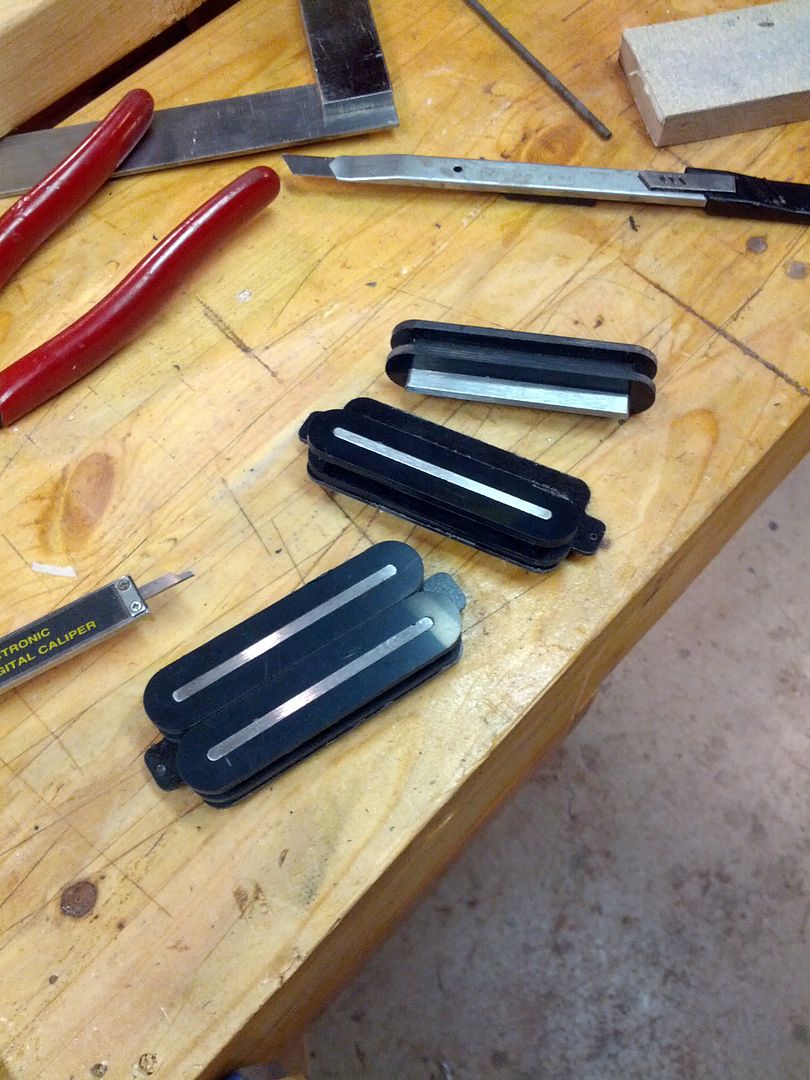

After all the pickup work time to get some stuff done. Trying to never waste wood I get enough out of a 48 x 8 x 4/4 piece of African Mahogany to get a neck blank and a body blank. Then I trim the top to get a headplate from the top as well.

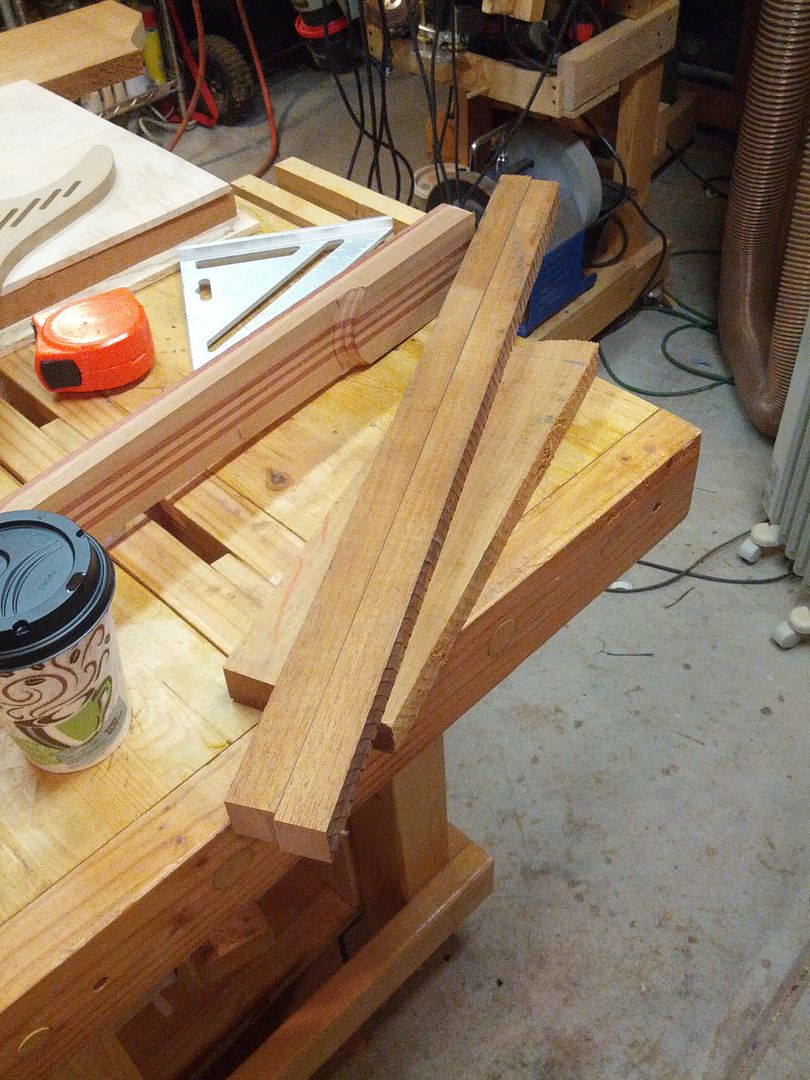

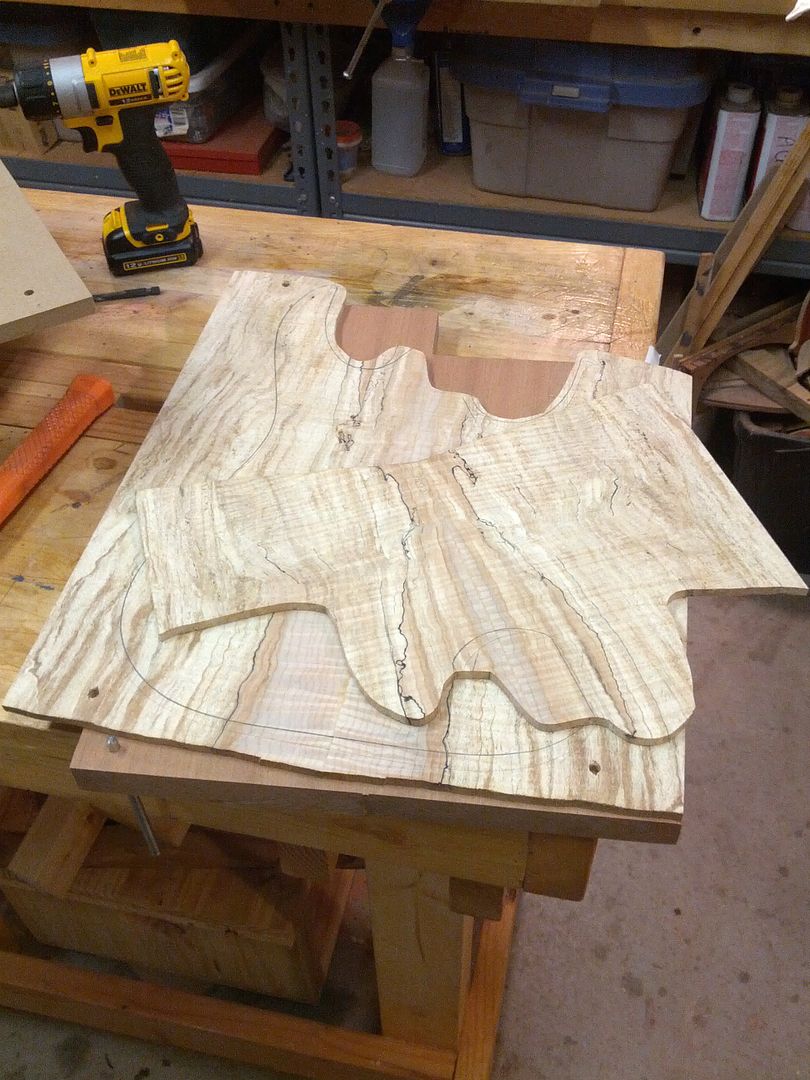

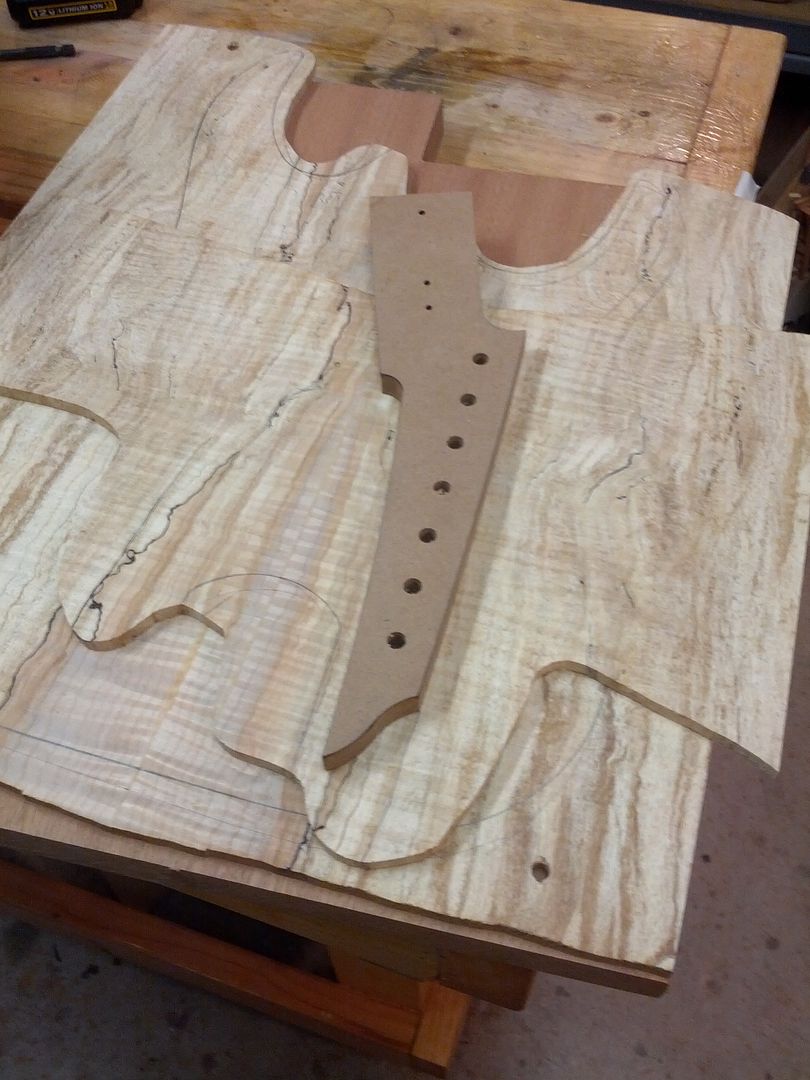