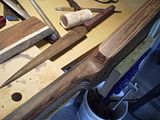
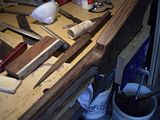
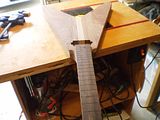
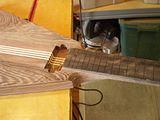
Time to shape the neck. The soft grain in the wenge tears out very easily (like ash) and leaves a bumpy surface. I ended up only using Rasps and Files as any type of blade (scraper, spoke shave) tended to make a mess. I have been experimenting with the trapzoid shaped necks. Not Ola style but more rounded with a flat spot on the back. I make a trapezoid then soften it... not sure it helps yet.
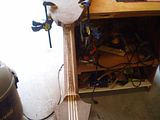
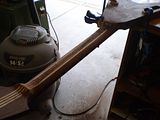
If anyone cares smoothing the neck out with a bastard file then a mill file worked really well on the wenge.
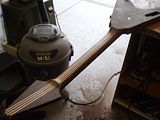
Then a little DA action.
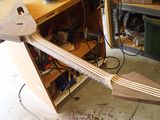
I rounded the heal out a little more after this shot.
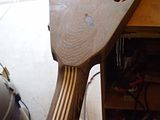
Volute also got a little rounder and smaller after this shot.
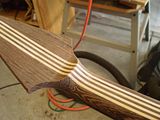
Bridge posts drilled. Stuck the bridge on to make sure hte strings line up. I don't drive the anchors in until much later.
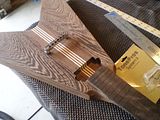
Lets have a look and see how far to recess the bridge... looks like it will only be a little bit.
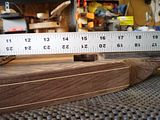
So I was going to copy my Gibson V in measurements because I thought it was a 24.75" scale V. Turns out it is not it is a 24.625". Good thing I double checked before drilling the bridge. That would have made a mess.
All good now but once again this is why you plan everything out first.
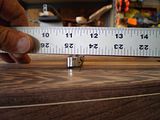
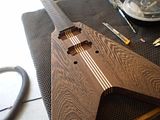
Again ... enough for one day. I am never building another neck through unless someone pays me. (I said that the last time I built one.)
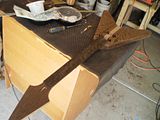
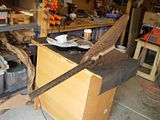
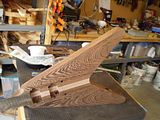