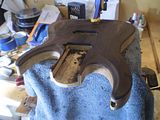
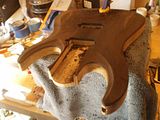
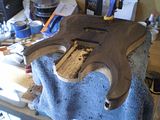
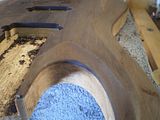
Heavy mineral oil after spending another hour removing scratches. Oil finishes require a lot of attention to detail.
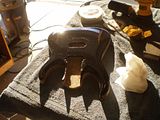
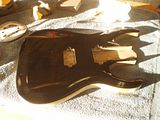
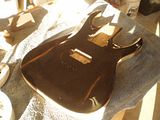
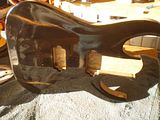
Another look. I really like the brown streaks on each side. Keeps the whole thing from looking like black plastic.
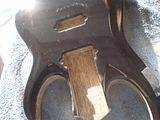
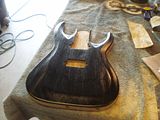
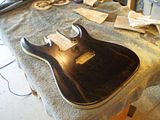
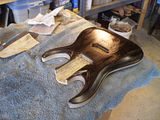
Another look
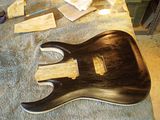
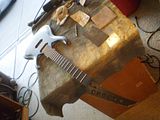
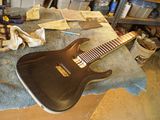
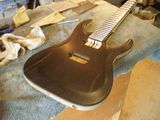
Getting close to gluing the neck and need to clean up the edges of the pocket.
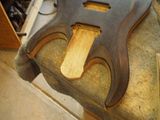
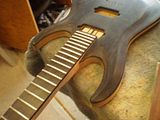
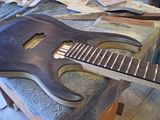
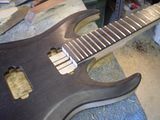
Starting on the neck. Using the Japanese saw rasp. Then moving to the dragon rasps. Finished out with long sanding blocks.
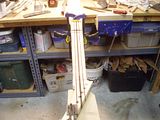
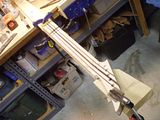
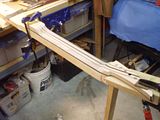
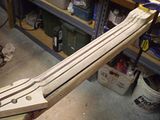
Almost finished. For some reason I didn't get any photos of the finished neck.
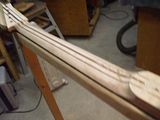
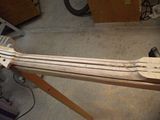
Ready for glue up. Tape everything off to prevent epoxy from getting into the grain.
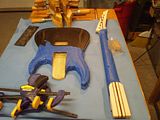
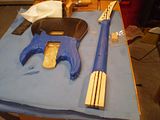
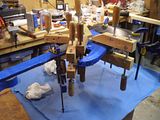
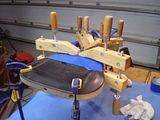